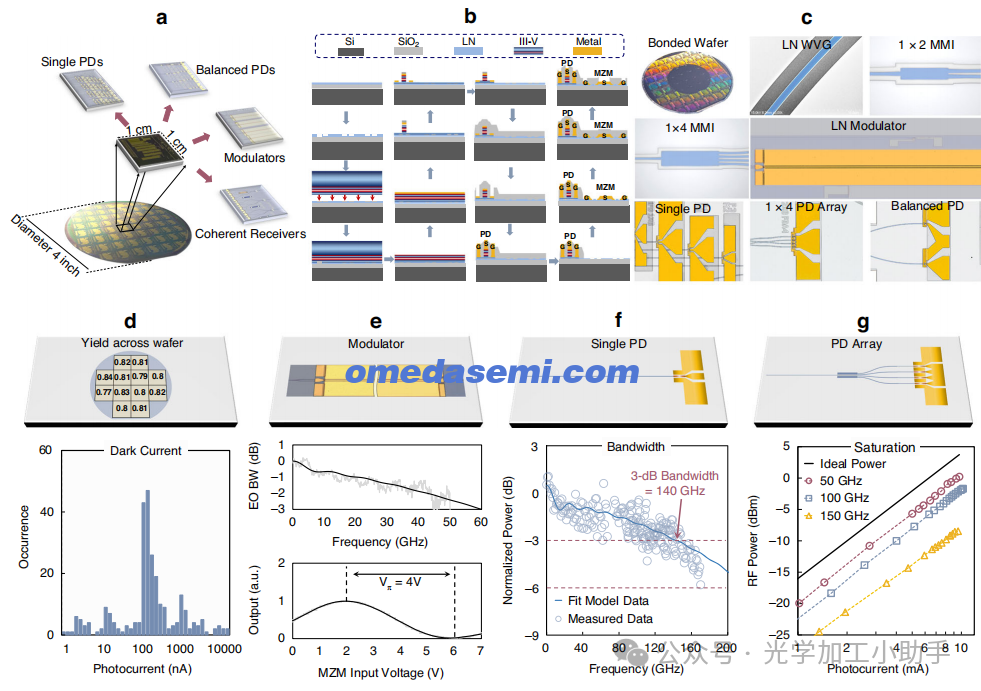
摘要
薄膜铌酸锂(LiNbO3)平台的快速发展已使其成为高性能光子集成电路的首选。然而,该平台的可扩展性和成本效益受到被动和主动组件依赖芯片级制造与集成的限制,迫切需要一个稳健的晶圆级LiNbO3异质集成平台。尽管它在实现超高速光互连以及光学毫米波/太赫兹传感和通信方面起着关键作用,但在LiNbO₃平台上实现超高速光电二极管和光学相干接收器仍然是一个未解决的挑战。主要原因是与直接带隙材料的大规模集成相关的挑战。为了解决这些问题,我们开发了一个可扩展的、高速的InP-LiNbO₃晶圆级异质集成平台。该平台可以制造带宽为140 GHz的超高速光电二极管,能够接收高质量的100-Gbaud脉冲振幅调制(PAM4)信号。此外,我们展示了一款七通道、单极化I-Q相干接收器芯片,具有3.584 Tbit/s的总接收能力。该相干接收器展现了60 GHz的平衡检测带宽,并且共模抑制比(CMRR)超过20 dB。它在100-Gbaud 64-QAM信号下实现了600 Gbit/s λ⁻¹的接收能力,在128-Gbaud 16-QAM信号下实现了512 Gbit/s λ⁻¹的接收能力。此外,200 Gbit/s和400 Gbit/s容量下分别实现了9.6 fJ bit⁻¹和13.5 fJ bit⁻¹的低能耗。我们的工作为实现PB级超大规模数据中心互连以及光学毫米波/太赫兹传感和通信提供了可行的路径。
ALOOI晶圆;--氧化铝薄膜晶圆,键合工艺和镀膜工艺
TAOOI晶圆--氧化钽薄膜晶圆,镀膜工艺
SINOI晶圆;--超低损耗氮化硅薄膜晶圆,
SICOI晶圆;新型量子光学平台
6寸LTOI晶圆批量供应;铌酸锂的有力的竞争对手,薄膜钽酸锂晶圆
8寸LNOI晶圆;8寸LNOI助力更大规模薄膜铌酸锂产品量产
LN/LT-SOI/Si/SIN W2W&D2W异质集成
流片: 6寸 氮化硅 铌酸锂 硅光 超高性价比流片, 1个BLOCK的价格买一整片晶圆
划重点--全国产-超高性价比-6 寸硅光-氮化硅-铌酸锂流片白皮书
引言
基于云的人工智能(AI)服务的快速发展正在推动超大规模数据中心集群中的数据流量达到PB级别。这一数据流量的激增对超大容量解决方案提出了强烈需求。超大规模数据中心内部的高速互连对于系统的最佳性能至关重要。然而,传统的电气互连受到物理限制的制约,限制了其带宽、能效和延迟,这对于超大规模系统而言是一个瓶颈。集成光子互连作为一种有前景的替代方案,提供了更高的带宽、更低的延迟和更好的能效。电光(E-O)和光电(O-E)转换的性能对集成光子互连至关重要。为了满足每通道数Tbps和PBps的光互连要求,所需的300 Gbaud E-O和O-E接口在相干收发器中的模拟带宽应大于150 GHz。除了超大规模AI集群,6G通信研究的持续进展正在推动向更高频段的重大转变,包括毫米波(mmWave)和太赫兹(THz)波段。这一转变是由于较低频段的频谱拥挤以及mmWave和THz波段中可用的广泛连续带宽,这对于满足下一代网络中超高速数据率和低延迟通信的日益增长的需求至关重要。光子技术在毫米波和太赫兹传感和通信系统中提供了显著优势,包括大调制带宽、低噪声mmWave/THz信号生成和真实时间延迟能力。
图1 光互连和光学毫米波/太赫兹传感与通信的系统架构。DSP 数字信号处理器,ASIC 应用特定集成电路,TRx 光学收发器,IMDD 强度调制与直接检测,PD 光电二极管,MZM 马赫-曾德调制器,MWP 微波光子学
图1展示了光互连和光学毫米波/太赫兹传感与通信的应用和系统架构。
然而,光子集成平台上电光调制和光电检测的典型带宽,包括硅光子(SOI)、氮化硅(Si3N4)和磷化铟(InP),通常限制在几十GHz。薄膜LiNbO3因其强大的电光系数、紧密的模场约束和广泛的透明窗口,已成为高性能光子集成平台,特别适用于高速应用。最先进的薄膜LiNbO3 I-Q调制器,凭借大Pockels系数(32 pm·V−1),已展示出超过110 GHz的带宽和小于1 V的半波电压(Vπ)。理论上,薄膜LiNbO3调制器的带宽估计超过300 GHz。此外,多个电泵激光器和高速光电二极管已在薄膜LiNbO3平台上通过混合和异质技术得以实现。尽管迄今为止LiNbO3集成器件取得了显著进展,但LiNbO3集成光子的广泛应用仍受到几个关键因素的限制。首先,这些器件的制造通常依赖于电子束光刻,这是一个芯片级工艺,给大规模、成本效益的生产带来了重大挑战。其次,薄膜LiNbO₃上主动器件的异质集成仍然主要在芯片级进行。开发晶圆级异质集成工艺对于薄膜LiNbO3平台上主动器件的集成至关重要,这对于实现大规模薄膜LiNbO3光子集成电路具有重要意义。第三,作为超大容量光互连、超高速光子计算和高性能微波/毫米波/太赫兹光子学的核心组件,薄膜LiNbO₃平台上尚未报道超高速光电二极管和相干接收器芯片,因为缺乏可靠的晶圆级异质集成平台。此外,在同一芯片上实现毫米波/太赫兹调制器、光电探测器和相干接收器的单片集成仍然存在关键技术差距,以满足毫米波/太赫兹光子应用对性能的严格要求。
在本文中,据我们所知,我们首次展示了一个超高速相干接收器芯片及其与高速调制器在可扩展的InP-LiNbO₃晶圆级集成平台上的单芯片集成。一个单芯片包含七通道单极化I-Q相干接收器,展示了3.584 Tbit/s的总数据容量。I-Q相干接收器芯片包括一个紧凑的高性能2 × 4 90°光学混合器和一个高速平衡光电二极管阵列。单通道相干接收器成功接收了128 Gbaud 16-QAM信号(512 Gbit/s)和100 Gbaud 64-QAM信号(600 Gbit/s)。在1040 km和25 km的传输后,成功解调了100 Gbaud QPSK和16-QAM信号。值得注意的是,在200 Gbit/s和400 Gbit/s容量下,分别实现了9.6 fJ bit⁻¹和13.5 fJ bit⁻¹的超低能耗。该单极化相干接收器的性能超越了所有先前展示的集成相干接收器芯片,在带宽、容量和能效方面设立了新的记录。我们的工作为PB级超大规模数据中心互连、微波/毫米波/太赫兹光子信号生成与处理以及全光子毫米波/太赫兹集成传感与通信提供了潜在的解决方案。
结果
制造
图2 晶圆级薄膜LiNbO3异质集成平台。
a 4英寸晶圆级InP-LiNbO3异质集成平台的示意图。
b 异质集成平台的制造过程。
c 键合晶圆的照片;制造的薄膜LiNbO3波导(WVG)、1 × N MMI耦合器、调制器、单光电二极管(PD)、1 × 4光电二极管阵列和平衡光电二极管的假彩色显微镜图像。
d 单光电二极管的暗电流分布统计及晶圆上基于芯片位置的产率。
e 制造的强度调制器的示意图、测量的电光(EO)响应和半波电压。
f 单光电二极管的示意图和频率响应。
g 1 × 4光电二极管阵列的示意图和射频输出功率。
图2a展示了晶圆级异质集成平台的示意图。单光电二极管(PD)、光电二极管阵列、平衡光电二极管、光学混合器、强度调制器和相干接收器设计在一个尺寸为1 × 1 cm的掩模上。与我们之前的外延层相比,本研究中的外延层设计为在晶圆键合后形成n-mesa-down结构。该设计旨在降低串联电阻,提高带宽并增加输出射频功率。具有n-mesa-down结构和p-mesa-down结构的异质集成光电二极管的模拟串联电阻在补充说明1中有详细说明。InP/InGaAs晶圆的外延层采用金属有机化学气相沉积(MOCVD)方法在半绝缘InP基板上生长,具体内容详见补充说明1。
主要制造过程如图2b所示。首先,在晶圆级别制造薄膜LiNbO3波导和被动器件。使用氩气干法刻蚀形成低损耗的脊形波导和高性能的多模干涉(MMI)耦合器。薄膜LiNbO3波导的总厚度为600 nm,板材厚度为300 nm。图2c展示了制造的波导和1×N MMI耦合器的假彩色显微镜图像。在对被动组件进行干法刻蚀后,薄膜LiNbO3晶圆进行了彻底的抛光和清洁。随后,将一个2英寸InP/InGaAs晶圆键合到薄膜LiNbO3晶圆上。使用氯化氢(HCl)进行选择性湿法刻蚀以去除InP基板,湿法刻蚀精确地停止在InGaAs p接触层。接着,在p接触层上沉积金属。光电二极管的主动区域采用双mesa结构,p mesa使用基于氯的干法刻蚀工艺刻蚀到n接触层。相同的干法刻蚀工艺用于刻蚀n mesa。接着进行n接触金属沉积,以防止可能的氧化。然后应用湿法刻蚀暴露LiNbO3表面,防止潜在损伤。整个晶圆表面沉积了600 nm的SiO2层作为钝化层,以减少暗电流,并保护波导和被动器件免受后续工艺中的杂质影响。p和n接触金属堆上的SiO2通过干法刻蚀形成金属通孔。通过电镀和剥离创建金属电极。在光电二极管制造完成后,调制器区域的SiO2钝化层被刻蚀,以暴露LN波导。然后在LN上沉积金属以形成传输线。整个晶圆上沉积了SiO2包覆层,然后通过干法刻蚀打开pad区域上的SiO2包覆层。晶圆被切割成1 × 1 cm的芯片,并对其进行侧面抛光以减少耦合损失。更多细节请参见“方法”部分。
器件设计与特性
1 × N MMI耦合器,基于自成像原理,用于均匀分配光到1 × N光电二极管阵列中。1 × 2、1 × 3和1 × 4 MMI耦合器的尺寸分别为6 × 26 µm、6 × 38 µm和6 × 52 µm。基于从同一晶圆中随机选择的200多个单光电二极管的I-V特性,晶圆级异质集成的制造产率估计超过80%。图2d显示了在-4 V偏置电压下的暗电流统计数据。大多数器件的暗电流低于300 nA,有些器件的暗电流低至几个nA(见补充说明2)。图2e展示了制造的强度调制器的示意图和性能。基于测量的S参数,提取的特征阻抗和微波有效折射率分别为45 Ω和2.15。强度调制器表现出了超过50 GHz的3 dB带宽和4 V的半波电压。更多关于强度调制器的细节可见补充说明3。
带宽和输出射频功率使用外差技术测量,具体内容见补充说明4。光电二极管的频率响应在固定光电流下进行表征,使用四个覆盖DC–67 GHz、75–110 GHz、90–140 GHz和110–170 GHz频段的射频探针。一个1.5 × 8 µm的单光电二极管展示了140 GHz的3 dB带宽和0.4 A W⁻¹的响应度,如图2f所示。有关响应度的更多细节可见补充说明5。使用矢量网络分析仪在DC–67 GHz的频率范围内测量器件的S参数。通过将测量的S参数拟合到等效电路模型(见补充说明6),提取的电容和电阻分别为11.5 fF和12 Ω。寄生电容估计为6 fF。低电阻得益于n-down外延结构,如前所述。pad电容和电感估计分别为8.5 fF和42 pH。通过优化pad电容(19.5 fF)和电感(65 pH),预测3 dB带宽可达到220 GHz。更多细节请参见补充说明6。此外,开发了1 × N光电二极管阵列以增强输出功率。1 × 4光电二极管阵列表现出了45 GHz的3 dB带宽(见补充说明7)。
使用外差设置,我们固定了拍频,同时改变输入到器件中的光功率,以测量光电流和射频输出功率。图2g展示了1 × 4光电二极管阵列在50 GHz时实现了0.2 dBm的射频输出功率,在100 GHz时为-1.7 dBm,在150 GHz时为-8.5 dBm,且无需主动冷却。这些光电二极管的功率处理能力满足了相干光通信的要求,并实现了无需射频放大器的信号接收。对于微波/毫米波/太赫兹光子学应用,这些高功率和高速光电二极管增强了系统性能,包括提高系统增益、噪声因子和动态范围,增大了毫米波/太赫兹信号功率,以及更长的传感和通信距离。
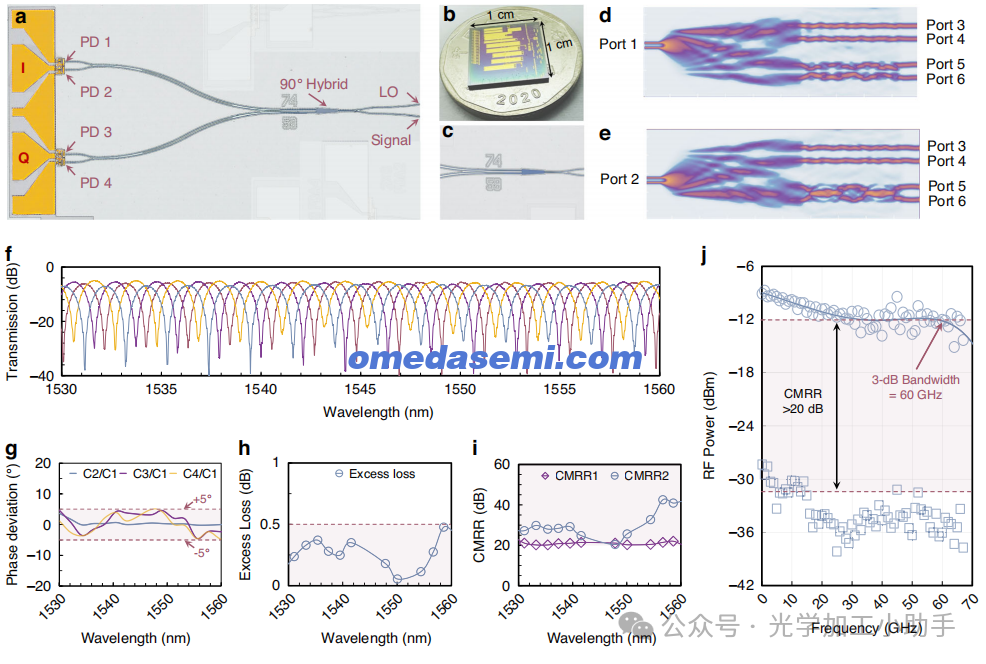
图3 集成在薄膜LiNbO3平台上的异质高速相干接收器。
a 制造的相干接收器的假彩色显微镜图像。
b 相干接收器芯片与硬币的对比。
c 90°光学混合器的假彩色显微镜图像。
d, e 光学90°混合器的光功率演化模拟,具有两个输入端口。
f 在C波段范围内,使用马赫-曾德延迟干涉仪测量的设备四个输出端口的传输光谱。
g 测量的相位偏差。
h 测量的附加损耗。
i 测量的共模抑制比(CMRR)。
j 平衡光电二极管在差分模式和共模模式下的频率响应。
图3a展示了制造的光学相干接收器,该接收器由90°光学混合器和一个平衡光电二极管阵列组成。光学信号和光学本地振荡器(LO)被送入光学混合器,然后由平衡光电二极管阵列进行检测(PD1-PD2对作为同相分量,PD3-PD4对作为正交分量)。产生的I-Q电信号通过数字信号处理(DSP)处理,以恢复原始信息。作为相干接收器中的关键组件,光学90°混合器(图3c)包括一个基于配对干涉的2 × 4 MMI耦合器和一个基于通用干涉的2 × 2 MMI耦合器。紧凑型光学90°混合器具有74 µm长的2 × 4楔形MMI耦合器和59 µm长的2 × 2 MMI耦合器。结构的对称性确保了来自2 × 4 MMI耦合器的两个相邻输出保持同相关系。采用基于通用干涉的2 × 2 MMI耦合器,以通过90°调整输出对的相位关系。这一配置确保了四个输出信号具有0°、180°、90°和270°的相对相位差。这消除了传统4 × 4 MMI 90°混合器所需的交叉波导,使其成为紧凑型集成相干接收器芯片的理想选择。光学90°混合器的光学仿真是使用Lumerical有限差分时域(FDTD)求解器(Lumerical 2023 R1)进行的。图3d和3e展示了光学90°混合器在两个光学输入下的光功率演化。每个光学输入的光功率均匀分布到四个输出端口。紧凑型楔形光学90°混合器的性能通过马赫-曾德干涉仪(MZI)进行实验表征(见补充说明8)。该器件在1530 nm到1560 nm的光谱范围内表现出小于±5度的相位偏差(图3g),小于0.5 dB的附加损耗(图3h)和超过20 dB的共模抑制比(CMRR)(图3i)。其性能与商业90°光学混合器相当。
光学相干接收器依赖于具有大带宽和高CMRR的平衡光电二极管,以捕获具有最佳信噪比的高速电信号。带宽和CMRR通过外差设置和可变光学延迟线进行表征(见补充说明4)。图3j展示了平衡光电二极管在差分模式和共模模式下的频率响应,揭示了60 GHz的3 dB带宽和超过20 dB的CMRR。高性能平衡光电二极管为实现超高速光学相干接收器奠定了基础。所测得的CMRR通常足以通过抑制共模强度噪声并保持高信号保真度来确保强健的信号恢复。为了新应用如量子传感和通信,可能需要通过最小化制造引起的光电二极管响应度的非对称性、优化具有平衡阻抗和相位匹配的电极设计以及实现芯片上的光功率和相位控制来进一步改进性能。
强度调制直检(IMDD)
图4 单光电二极管IMDD的实验演示。
a IMDD的实验设置,ECL:外腔激光器,PC:偏振控制器,AWG:任意波形发生器,MZM:马赫-曾德调制器,EDFA:掺铒光纤放大器,RTO:实时示波器。
b–e 50 Gbaud(b)、60 Gbaud(c)、80 Gbaud(d)和100 Gbaud(e)PAM4信号在B2B传输中的眼图和相应的BER。
f 接收100 Gbaud PAM4信号时,测量的BER与接收光功率的关系。SD-FEC:软判决前向纠错,HD-FEC:硬判决前向纠错。
为了验证制造器件的性能,我们在IMDD系统中应用了单光电二极管,用于数据中心内光互连的应用,如图1b所示。实验设置如图4a所示(见“方法”部分)。单光电二极管成功解调了具有高速的PAM4信号,波长为1550 nm。图4b–e分别展示了50 Gbaud、60 Gbaud、80 Gbaud和100 Gbaud PAM4信号的回传(B2B)传输的眼图和对应的比特误码率(BER)。所有眼图证明PAM4信号的高质量接收,四级符号的清晰区分。具体来说,50 Gbaud、60 Gbaud和80 Gbaud PAM4信号的BER低于KP-FEC限制2 × 10⁻⁴,分别对应的数据速率为100 Gbit/s、120 Gbit/s和160 Gbit/s。在100 Gbaud符号率(200 Gbit/s)下,器件实现了高性能接收,BER为2.7 × 10⁻⁴,低于硬判决前向纠错(HD-FEC)限制(3.8 × 10⁻³)。随后,通过改变入射光功率,表征了100 Gbaud PAM4信号的BER与接收光功率的关系,如图4f所示。当接收光功率达到-4 dBm时,BER低于25%软判决前向纠错(SD-FEC)限制4 × 10⁻²;当接收光功率为-1 dBm时,BER低于HD-FEC限制。
相干检测
图5 使用光学相干接收器进行相干检测的实验演示。
a 相干检测的实验设置,IQM I-Q调制器,SMF单模光纤。
b 100 Gbaud和128 Gbaud QPSK,80 Gbaud、100 Gbaud和128 Gbaud 16-QAM,80 Gbaud和100 Gbaud 32-QAM,80 Gbaud和100 Gbaud 64-QAM信号在B2B传输中的星座图和相应的BER。
c 测量的BER与接收光功率的关系,适用于100 Gbaud QPSK、100 Gbaud 16-QAM和100 Gbaud 32-QAM信号。
d 100 Gbaud QPSK和100 Gbaud 16-QAM信号在传输1040 km和25 km后的星座图和BER。
e 多通道相干接收的星座图和B2B BER。
为了验证单极化相干接收器在数据中心间光互连应用中的性能,如图1b所示,我们构建了如图5a所示的实验设置。光学信号通过带宽为30 GHz的I-Q调制器被射频信号调制。经过光学90°混合器混合后,光学信号和LO信号被分成四个输出,具有0°、180°、90°和270°的相对相位差,这些信号通过平衡光电二极管阵列进行相干检测。生成的I-Q电信号直接送入实时示波器(RTO),无需使用射频放大器。实验设置的详细信息在“方法”部分中给出。我们在1550 nm波长下进行了相干接收实验,测试了不同的符号率(80 Gbaud、100 Gbaud、128 Gbaud)和先进的调制格式(QPSK、16-QAM、32-QAM和64-QAM)。接收的信号通过离线DSP(见“方法”部分)处理,以计算其BER。图5b总结了不同符号率和调制格式在回传(B2B)传输中的星座图和BER。对于QPSK信号,在100 Gbaud(200 Gbit/s)时实现了无误码接收。对于符号率为128 Gbaud(256 Gbit/s)的QPSK信号,对应的BER为1.7 × 10⁻⁵,低于KP-FEC限制。80 Gbaud和100 Gbaud 16-QAM信号的BER分别为1 × 10⁻³和2.3 × 10⁻³,均低于HD-FEC限制,相应的数据速率分别为320 Gbit/s和400 Gbit/s。此外,成功接收了128 Gbaud 16-QAM(BER = 3.4 × 10⁻²)、80 Gbaud 32-QAM(BER = 1.1 × 10⁻²)、100 Gbaud 32-QAM(BER = 2.6 × 10⁻²)和80 Gbaud 64-QAM信号(BER = 3.1 × 10⁻²),其对应的最高数据速率达到512 Gbit/s。此外,对100 Gbaud 64-QAM信号的接收实验结果表明,数据速率为600 Gbit/s,BER为4.9 × 10⁻²,低于28% SD-FEC限制(5 × 10⁻²)。
如图5c所示,100 Gbaud QPSK、100 Gbaud 16-QAM和100 Gbaud 32-QAM信号的BER与接收光功率的关系被确定。对于100 Gbaud QPSK信号,当接收光功率分别达到-2 dBm、0 dBm和2 dBm时,测得的BER分别低于25% SD-FEC限制、HD-FEC限制和KP-FEC限制。对于100 Gbaud 16-QAM和100 Gbaud 32-QAM信号,当光电二极管的入射功率分别达到1 dBm和6 dBm时,接收到的BER低于25% SD-FEC阈值。
此外,我们进行了使用相干接收器芯片的长距离传输通信实验。实验结果如图5d所示。经过1040 km单模光纤传输后,接收到的100 Gbaud QPSK信号的BER为3.9 × 10⁻²。对于100 Gbaud 16-QAM信号,经过25 km单模光纤传输后,BER为3.9 × 10⁻²。在长距离通信实验中,每80 km光纤传输(约16 dB损耗)进行一次光学放大(增益16 dB)。最后,使用七通道单极化I-Q相干接收芯片进行多通道通信演示,在B2B传输中,通过25% SD-FEC限制,所有通道成功接收了128 Gbaud 16-QAM信号,使单个芯片的总通信容量达到了3.584 Tbit/s,如图5e所示。
讨论
如上所述,我们开发了一个晶圆级异质InP-LiNbO3集成平台,实现了大规模制造和高工艺产率以及多功能集成。单光电二极管在薄膜LiNbO3异质集成平台上实现了创纪录的140 GHz带宽,这得益于最小化的寄生电容和串联电阻。通过对光电二极管等效电路中共振效应的详细工程设计,我们预计3 dB带宽可超过200 GHz。这一进展为未来符号率超过300 Gbaud的短距离强度调制直检(IMDD)光互连打开了大门。除了高带宽能力,光电二极管精心设计的外延结构增强了输出射频功率,便于在无需射频放大器的情况下直接或相干接收高速信号,同时提高了微波/毫米波/太赫兹光子学系统的性能。毫米波/太赫兹调制器和光电二极管的集成使数据中心、中心站和基站之间的光互连成为可能,同时促进了毫米波/太赫兹信号的发射和接收,如图1b所示。
薄膜LiNbO3光学相干接收器得益于高性能的90°光学混合器和高速平衡光电二极管阵列,展示了在接收超高速信号时的卓越性能,支持先进的调制格式。据我们所知,这是首次在薄膜LiNbO3平台上进行超高速相干接收器的实验演示。表1总结了迄今为止报道的最新的集成光学相干接收器,包括基于InP/InGaAs、SiGe、石墨烯和LiNbO3等材料的单片集成和异质集成平台。与其他集成平台相比,我们的异质集成相干接收器通过精心设计的修改型单载流子光电二极管外延结构,实现了3 dB带宽提升75%的性能。
在我们的工作中,单极化相干接收器芯片展示了在解调超高速信号方面的强大能力。在B2B传输中,它实现了最高数据速率600 Gbit/sλ⁻¹Pol⁻¹(100 Gbaud 64-QAM)。通过7 × 128 Gbaud 16-QAM信号的多通道相干接收,进一步凸显了它在超大容量短距离光学相干互连中的潜力,总数据容量达到了3.584 Tbit/s。此外,相干接收器展示了在长距离光通信系统中的应用前景,成功接收了经过1040 km的100 Gbaud QPSK信号和经过25 km的100 Gbaud 16-QAM信号。值得注意的是,目前接收能力受到可用I-Q调制器和AWG带宽的限制。未来的改进可以通过利用更高带宽的I-Q调制器和更先进的AWG来实现更大的容量。最后,也是最重要的,相干接收器在不需要射频放大的情况下实现了这些创纪录的大容量,从而实现了超低能耗。我们开发的异质集成相干接收器由两个芯片上的平衡光电二极管组成。每个极化只需要两个通道的高速电子组件,大大减少了电子电路的功耗和复杂性。具体来说,200 Gbit/s时能耗低至9.6 fJ bit⁻¹,400 Gbit/s时能耗为13.5 fJ bit⁻¹,突显了其在高速数据传输场景中的高效性(见补充说明9)。
总之,我们提出的薄膜LiNbO3异质集成光电二极管实现了创纪录的140 GHz带宽。光学相干接收器具有60 GHz的平衡检测带宽、超过20 dB的CMRR和9.6 fJ bit⁻¹的能耗。该能力支持每极化通道达到600 Gbit/s的数据接收,并实现了七个通道的总容量为3.584 Tbit/s。与现有的集成光学相干接收器相比,我们的异质集成相干接收器在带宽、超低能耗和超大容量方面设立了新的基准。此外,我们的InP-LiNbO3异质集成平台具有将激光器、调制器和接收器集成到单一LN芯片上的能力,通过晶圆键合和选择性再生长技术汇聚而成。集成的收发器芯片将显著减少封装组装的复杂性,并提高整个芯片的集成密度。除了为超大规模数据中心提供高性能收发器外,多功能的InP-LiNbO3晶圆级异质集成平台还有望实现微波/毫米波/太赫兹光子学信号生成和处理芯片以及全光子学太赫兹通信和传感集成芯片。
材料与方法
器件制造
整个制造过程中所有的图形化和对准工作均在薄膜LiNbO3晶圆和键合晶圆上使用i线步进光刻系统进行。薄膜LiNbO3波导和被动器件通过电感耦合等离子体(ICP)精确加工,使用氩气刻蚀300 nm的LiNbO3,保留了300 nm的板材层。在键合之前,LiNbO3表面经过化学机械抛光,以确保表面光滑均匀,并最大限度减少纳米尺度波导特征的影响,这对于后续的晶圆键合工艺至关重要。2英寸的InP/InGaAs光电二极管晶圆被键合到4英寸的LNOI晶圆上。晶圆键合后,InP基板的去除涉及研磨和使用HCl/H₂O的选择性湿法刻蚀,精确停止在InGaAs p接触层。使用电子束蒸发器沉积p金属堆(Ti/Pt/Au/Ti),建立欧姆接触。使用基于Cl₂的刻蚀工艺,通过ICP刻蚀将p-mesa刻蚀到n接触层。随后,通过电子束蒸发和剥离工艺沉积n接触金属(AuGe/Ni/Au)。相同的基于Cl₂的干法刻蚀工艺用于定义n-mesa,最终通过HCl/H₂O湿法刻蚀暴露LiNbO3表面。LiNbO3表面进一步用稀释的氟化氢酸处理,以去除潜在污染物和表面损伤。使用等离子体增强化学气相沉积(PECVD)在整个晶圆表面沉积600 nm的SiO2层作为钝化层。此层具有多种用途:减少暗电流、保护锂铌酸盐波导和被动器件,并减轻杂质颗粒的影响。使用ICP刻蚀系统和CF4气体刻蚀p和n金属堆上方的SiO2层,然后通过电镀和剥离工艺形成金属电极。在完成光电二极管制造后,调制器区域的SiO2钝化层首先被干法刻蚀,然后湿法刻蚀以暴露LN波导。在LN上沉积1 µm厚的金属(Ti/Au),形成传输线。整个晶圆上沉积900 nm的SiO2包覆层,以保护波导并调节光学群折射率,然后通过干法刻蚀打开射频pad区域的SiO2包覆层。最后,将晶圆切割成1 × 1 cm的小芯片。由于使用边缘耦合,芯片的边缘进行了侧面抛光。
器件表征
用于测量单光电二极管带宽的实验设置详细信息见补充说明4图S6a。使用两台外腔激光器(Keysight 81940A)通过3 dB耦合器组合,生成具有100%调制深度的光学拍频信号。通过控制激光器之间的波长差来调整拍频信号频率。光功率通过高功率EDFA放大,然后通过带有2.5 μm光斑直径的透镜光纤耦合到LiNbO3波导中。光信号通过单光电二极管进行检测。器件的频率响应使用覆盖DC–67 GHz、75 GHz–110 GHz、90 GHz–140 GHz和110 GHz–170 GHz频段的地-信号-地(GSG)探针进行表征。补充说明4图S6b展示了平衡光电二极管频率响应的测量设置。光学拍频信号被分成两条路径,每条路径中都包括可调光学延迟线,以调整它们之间的相位差。通过调节相位差,获得了共模(π相位差的偶倍数)和差分模式(π相位差的奇倍数)。使用可变衰减器补偿光学路径中的功率不平衡。来自每条路径的光信号通过透镜光纤耦合到平衡光电二极管。使用DC–67 GHz射频探针测量平衡光电二极管的带宽。所有带宽测量中,通过源表(Keithley 2400)通过偏置三通道(SHF BT65R, 65 GHz)为光电二极管提供偏置电压,频率范围为DC–67 GHz。在75–110 GHz、90–140 GHz和110–170 GHz频段内,波导射频探针中集成的内部偏置三通道为单光电二极管提供偏置电压。使用源表和射频功率计(Ceyear 2438CA)测量输出光电流和射频功率。校准时考虑了射频探针、偏置三通道和射频电缆的附加损耗,以确保准确的带宽和输出功率测量。
对于强度调制器的表征,使用矢量网络分析仪(VNA Ceyear 3672)测量S参数。可以通过S参数提取特征阻抗和射频有效折射率。强度调制器的电光响应通过光学测量设置进行测量。使用1550 nm激光通过带有2.5 μm光斑直径的透镜光纤输入光到芯片中。调制器的输出光由高速光电探测器(Finisar XPDV2120RA)接收。VNA用于测量光学链路的总射频响应(DC-50GHz)。通过去嵌光电二极管的光电响应,可以获得强度调制器的电光响应。通过三角波法表征调制器的半波电压。
高速数据接收(IMDD和相干检测)
在IMDD实验中,PAM4信号的长度为220个数据周期,通过AWG(Keysight M9505A,256 GSa/s)生成,并通过带有30 GHz带宽的I-Q调制器(EOspace 50 Gbaud I-Q调制器)调制到信号光上。通过偏振控制器控制I-Q调制器中光的偏振状态,以最大化I-Q调制器的输出功率。随后,调制后的光信号通过EDFA放大,并通过透镜光纤耦合到单光电二极管中。
在相干接收实验中,I和Q通道的射频信号(包含幅度和相位信息)被调制到信号光上。信号光和LO光分别通过EDFA放大,并通过透镜光纤耦合到薄膜LiNbO3相干接收器芯片中,光斑大小为2.5 µm。LO光的功率调整为比信号光高8 dB。经过芯片内的光学90°混合器的光子混合后,光信号被分割并送入平衡光电二极管阵列,生成I和Q电信号。平衡光电二极管阵列的偏置电压通过定制的地-信号-地-信号-地(GSGSG)射频探针施加,频率范围为DC到67 GHz。来自平衡光电二极管阵列的电信号直接送到实时示波器(Keysight UXR0594AP,256 GSa/s)进行处理,无需额外的射频放大。通过离线DSP计算眼图、星座图和BER。
数字信号处理
对于PAM4信号的DSP处理,首先将收集到的样本重新采样四倍。随后,使用Gardner算法恢复时钟,并通过决策导向的最小均方误差均衡(DMMSE)恢复信号。最后,通过符号到比特的映射计算BER。对于相干信号的DSP处理,首先使用Schmidt正交化算法处理I-Q调制信号,以补偿由于调制器和90°光学混合器引起的两个信号路径之间的非正交性,从而减轻相关的损伤。然后,信号以每符号两个样本的频率进行重新采样。进行时钟恢复和恒定模算法(CMA)均衡。随后,执行载波相位估计(CPE)以去除信号中的相位噪声。使用决策导向的最小均方误差(DDLMS)算法进行均衡,以进一步减少符号间干扰。最后,通过将接收到的信号与参考信号对齐计算BER。
作者:Xiaojun Xie1✉, Chao Wei1, Xingchen He1, Yake Chen1, Chenghao Wang1, Jihui Sun1, Lin Jiang1, Jia Ye1, Xihua Zou1,Wei Pan1 and Lianshan Yan1