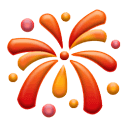
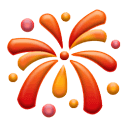
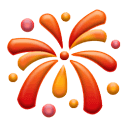
#4-8寸临时键合+减薄抛光+解键合一条龙--键合膜键合解键合摘要——超薄晶圆通常具有小于200 μm的厚度,是半导体器件制造中的重要基础组件。由于超薄晶圆具有特殊的机械性能,其制造和处理过程与传统晶圆有显著不同。因此,本文综述了超薄晶圆技术的进展,包括制造工艺、晶圆运输和器件应用等方面。通过机械研磨结合抛光或刻蚀的应力释放,已成为标准的晶圆减薄工艺。随着TAIKO晶圆的出现,专用设备和载体在超薄晶圆处理中的需求可能会逐渐被淘汰。超薄晶圆在半导体器件制造中具有广泛的应用,并将在半导体产业中产生长期影响。关键词:超薄晶圆、研磨、刻蚀、载体、器件
#用于GaN外延的111SOI晶圆
#全国产SOI晶圆定制加工 #468寸50nm-15um热氧片
库存片:
220nmSI高阻-3umSIO2-675umSI 6寸8寸 用于薄硅硅光
3000nmSI高阻-3umSIO2-675umSI 6寸8寸 用于厚硅硅光
#尺寸4-8寸
#最小起订量1片
#热氧层厚度范围50nm-15um
#膜厚精度最高精度+-5nm
#厚膜SOI-减薄抛光工艺600nm到微米级,加离子束精修,超级高精度膜厚均匀性
#CavitySOI-带空腔SOI晶圆,光刻显影刻蚀键合制作SOI一条龙
#FDSOI -最薄顶层10nm,特殊工艺精修,粗糙度小,膜厚精度高
普通超薄:SMARTCUT+离子束精修
超级超薄:EPI+SMARTCUT+离子束精修
#超平硅片-TTV500nm
我们为客户提供晶圆(硅晶圆,玻璃晶圆,SOI晶圆,GaAs,蓝宝石,碳化硅(导电,非绝缘),Ga2O3,金刚石,GaN(外延片/衬底)),镀膜(PVD,cvd,Ald,PLD)和材料(Au Cu Ag Pt Al Cr Ti Ni Sio2 Tio2 Ti3O5,Ta2O5,ZrO2,TiN,ALN,ZnO,HfO2。。更多材料),键合(石英石英键合,蓝宝石蓝宝石键合)光刻,高精度掩模版,外延,掺杂,6寸DUVKRF电子束光刻等产品及加工服务(请找小编领取我们晶圆标品库存列表,为您的科学实验加速。
请联系小编免费获取原文
文章名:Ultra-thin wafer technology and applications: A review作者:Zihan Dong, Yuanwei Lin单位:Department of Semiconductor Etching, NAURA Technology Group Co., Ltd., Beijing, 100176, China1.引言
硅晶圆对现代电子工业具有重要意义,因为硅具有基础的功能,如强大的机械强度和半导体性质[1-4]。较大的晶圆尺寸可以同时制造更多的器件,从而降低成本。与传统厚度约为700 μm的晶圆相比,超薄晶圆(厚度小于200 μm)的机械稳定性大大降低,可能会由于自身重力的影响而导致弯曲甚至破裂[3]。为了提供大尺寸晶圆的足够机械和热稳定性,晶圆的厚度需要增加,以确保在制造过程中加工步骤中晶圆的安全性(不破裂)。然而,从器件性能的角度来看,晶圆应当被减薄(通常小于200 μm),以保持摩尔定律,尤其对于具有3D堆叠的器件[5-7]。解决上述矛盾的一种方法是将薄化的晶圆与大尺寸的玻璃或塑料载体进行粘合[8-11]。由于粘合晶圆所使用的不同材料之间存在热膨胀系数不匹配,接口承受着高热和/或机械应力,这限制了带载体的超薄晶圆的应用。此外,所使用的载体无法帮助克服在背面研磨过程中引入的损伤,因此无法减少在切割过程中晶圆破裂的风险。另一种替代方法是切割前研磨(DBG)技术,其中晶圆被半切,以便在随后的背面研磨过程中自动分离芯片[12-14]。尽管DBG工艺与标准背面研磨工艺的区别仅在于工艺顺序,但实际上,在DBG工艺中由于晶圆被薄化形成分离的芯片,因此并不存在超薄晶圆状态。因此,切割速度可以由于背面碎裂风险的降低而提高,相应地增加生产能力。此外,由于DBG工艺中不使用载体,它可以避免由于热膨胀系数不匹配导致的载体翘曲和真空系统中的气体释放[1,15-17]。然而,DBG工艺仅适用于先进封装,其中器件已经制造成芯片。作为另一种无需载体的超薄晶圆技术,TAIKO晶圆近年来经历了快速发展[18-20]。载体的去除为超薄晶圆技术带来了极大的便利,超薄晶圆有潜力像传统晶圆一样进行加工。与DBG工艺相比,TAIKO晶圆可以同时用于电子器件制造和封装。超薄晶圆对电子器件的意义十分明显,无论是在制造还是封装中。从器件制造的角度来看,超薄晶圆可以减少垂直结构器件的导通电阻。对于具有横向结构的器件,超薄晶圆主要出现在封装过程中,它可以实现晶圆级封装,具有规模经济优势,并为芯片创建通孔接触提供几何优势。然而,TAIKO晶圆也面临一些不足。TAIKO晶圆中的较厚边缘/环区使得晶圆的有效区域减少,而去除TAIKO晶圆中较厚的边缘/环区在封装过程中具有挑战性。
因此,超薄晶圆的制造、处理、切割和封装方法和设备与传统方法有所不同,表明可能需要开发新的工艺和设备。近年来,尽管相关研究人员已经完成了大量工作并取得了丰硕的成果,但关于总结这些成就和展望该领域的综述文章较少,尤其是在从制造工艺到器件应用的超薄晶圆技术的连接方面。在这篇综述中,我们描述了超薄晶圆的制造、运输和应用。这些内容可能为半导体行业带来新的思路,因为器件晶圆的减薄已经成为半导体器件制造的标准实践。
2.超薄晶圆制造工艺
在实际生产方面,Dhadda等人[21]报告了IR(国际整流器公司,International Rectifier Co., Ltd.)的超薄晶圆制造过程,其中已经建立了一个8英寸(200 mm)超薄晶圆生产线。在IR,公司已经实现了120 μm和70 μm厚度的8英寸超薄晶圆的大规模生产。同时,50 μm和30 μm厚度的样品也已被证明是可行的。
2.1. 研磨与抛光
超薄晶圆制造的主流方法是机械研磨和抛光[22–26]。这种方法可以在几分钟内将晶圆厚度从约750 μm减薄到不到100 μm。其均匀性可以在晶圆内部和跨晶圆方向上得到很好的控制。近年来,超薄晶圆正朝着实现无载体方向发展。如图1所示,超薄晶圆没有载体,或者称为TAIKO晶圆,具有一个2–3 mm的边缘区域,这个区域没有被研磨,从而稳定晶圆,避免翘曲或弯曲[18,27] (另见网址:https://www.disco.co.jp/eg/solution/library/taiko.html)。由于自身重力的影响,传统的超薄晶圆容易发生弯曲,而TAIKO晶圆则没有明显的翘曲,能够实现自立(见图1a)。这是因为TAIKO晶圆中的未研磨边缘环提供了机械支撑(见图1b)。因此,TAIKO晶圆可以不使用载体(见图1b),而传统的超薄晶圆通常需要用胶水将其粘合到载体上以保持平整(见图1c)。此外,传统超薄晶圆与载体的锋利边缘也在TAIKO晶圆中被去除(见图1b和1c)。
图1. TAIKO工艺和传统工艺制造的超薄晶圆比较:(a) 传统超薄晶圆在自身重力的影响下容易弯曲,而TAIKO晶圆则能够实现自立。(b) TAIKO晶圆示意图。(c) 传统超薄晶圆通过胶水粘附在玻璃基板上的示意图。为了通过机械研磨获得超薄晶圆,通常采用一种研磨机,该研磨机主要包括电动机、研磨轮和夹具(如图2所示)。固定在夹具上的晶圆可以通过旋转的研磨轮进行研磨。正如图2a所示,在传统的晶圆减薄工艺中,研磨轮的尺寸大于晶圆,保证了均匀性[23]。相反,在TAIKO工艺[22]中,研磨轮的尺寸远小于晶圆,研磨仅发生在晶圆的内部分,而边缘部分则被去除2–3 mm(如图2b所示)。在TAIKO晶圆中,内部分的厚度可以减薄到小于200 μm,而边缘部分保持原有厚度。这种结构与一种名为“TAIKO”的日本鼓具有相似形状,其中内部部分由边缘支撑[1]。TAIKO晶圆不使用载体和粘合剂,因此基于TAIKO晶圆制造的器件可以在晶圆的两面进行加工,并承受更高的工艺温度。此外,TAIKO晶圆不需要特殊设备进行运输,这可以减少超薄晶圆处理过程中的成本。
图2. 机械研磨设备:(a) 传统工艺;(b) TAIKO工艺。但是,不可否认的是,TAIKO技术也存在一些缺点。随着晶圆尺寸的增大,标记晶圆方向的方法从平边改为缺口。在TAIKO晶圆中,由于存在缺口,较厚的边缘区域会扩展,这可能会减少晶圆的有效区域,进而限制TAIKO晶圆的发展。TAIKO晶圆的另一个不足是晶圆背面存在不均匀的未研磨边缘环,这在封装过程中会导致测量和切割困难。因此,在测量和分离芯片之前,TAIKO晶圆的较厚边缘/环区需要去除,通常需要特殊的刀片切割工艺或激光切割工艺。
考虑到在机械研磨过程中可能会产生损伤,由于应力集中在浅表损伤区域,超薄晶圆具有破裂风险。因此,需要进行应力释放以减少研磨过程中引入的损伤,这通常通过抛光实现。干抛光是一种环保的应力释放方法,与化学机械抛光(CMP)相比,它具有更低的成本和废料清除的优势。湿/干刻蚀也可以用于应力释放,在接下来的部分将会介绍。目前,机械研磨和随后的应力释放的结合已经成为标准的晶圆减薄工艺。
2.2. 湿法刻蚀
尽管上述提到的无载体晶圆可以增加晶圆的刚性并避免锋利的边缘,但由于使用机械研磨,背面研磨损伤和加工表面上的残余应力仍然是一个问题[28]。为了解决这个问题,采用刻蚀方法减薄晶圆可以减少表面损伤和残余应力。湿法刻蚀是刻蚀方法之一,它使用化学溶液与晶圆反应。将晶圆浸入化学溶液中是湿法刻蚀的常用方式,而如果晶圆只能暴露在化学物质的一侧(如超薄晶圆粘附在载体上),则通常采用旋转刻蚀或喷雾刻蚀。对于单面湿法刻蚀,美国MATECH(材料与技术公司)开发了一种全化学晶圆减薄工艺(WaveEtch™)。WaveEtch™工艺不仅能将晶圆减薄到40 μm或更薄,还能改善晶圆表面均匀性和柔韧性[29,30]。值得注意的是,这个系统能够自然地适应大尺寸和较厚形状的晶圆,这表明湿法刻蚀本身有潜力用于将晶圆从原始厚度减薄。根据湿法刻蚀过程中使用的碱性或酸性溶液,它大致可分为两种类型。Park等人[31]使用KOH溶液进行湿法刻蚀,去除超薄晶圆的表面应力,以便进行器件封装。与酸性溶液相比,使用碱性溶液的湿法刻蚀具有较低的刻蚀速率,但更高的刻蚀选择性。为了减少机械研磨后晶圆表面损伤,Yoshikawa及其同事开发了一种湿法刻蚀晶圆减薄方法,通过HF/HNO3溶液进行刻蚀,在这种方法中,可以实现较高的刻蚀速率(约800 μm/min,6–8英寸晶圆的均匀性为3%)[32,33]。除了减少机械研磨后晶圆表面损伤外,湿法刻蚀还可以用来增强超薄晶圆的芯片强度[34]。Li等人[35]证明了湿法刻蚀过程后,芯片侧壁可以变得更加光滑,其中大部分由切割过程引入的空隙和微裂纹被去除。
2.3. 干法刻蚀
干法刻蚀[36,37]是另一种晶圆减薄/刻蚀方法,它利用等离子体反应来处理晶圆表面,具有较高的表面质量,但相对较低的生产通量。McLellan等人[38]研究了等离子体刻蚀对晶圆表面粗糙度和形态的影响。如图3a和3b所示,晶圆表面的锐利和深刻划痕经过等离子体刻蚀过程后,替换为具有半圆形钝底的U形槽,其中蓝色的立方体和白色的空白分别代表晶圆和划痕。这一重要结果证明了晶圆粗糙度可以通过等离子体刻蚀得到改善,因为裂纹尖端的应力集中σm可以通过裂纹长度a和裂纹尖端半径ρ的函数来估算(σm = 2σ0(a/ρt)¹/²),其中σ0是施加的名义应力。图3c显示了经过干法刻蚀后,带有锐利裂纹尖端的划痕变成了具有半圆形钝底的U形槽。因此,在等离子体刻蚀过程中,随着a/ρt比率的降低,应力集中将变得更低,表明干法刻蚀方法可以改善表面粗糙度。因此,干法刻蚀是最有效的应力释放方法,用于去除背面研磨后的损伤层[39]。此外,类似于湿法刻蚀,干法刻蚀也可以在切割过程后进行正面应力释放[1,35]。
与机械研磨和湿法刻蚀相比,干法刻蚀本身并不适合用于晶圆减薄过程,原因是其刻蚀速率较低,成本较高,并且存在环境和粒子问题。由于机械研磨、抛光、湿法刻蚀和干法刻蚀各自的优势,机械研磨与后续的抛光或刻蚀处理结合,可能成为标准的晶圆减薄工艺,从而同时实现高表面质量和生产通量。一般来说,表面质量可以通过原子力显微镜(AFM)或3D激光测量显微镜给出的均方根粗糙度(Rq)来确定。因此,由减薄过程引入的损伤将按定义恶化表面质量。由于机械研磨后的表面质量较低,因此需要通过抛光或刻蚀的后处理来释放集中在损伤处的应力。值得注意的是,这些应力还可以用于在光伏应用中获得超薄晶圆[40],但最终表面质量应通过湿/干法刻蚀进一步提高,以释放应力并清洁表面[41]。如果能够改善机械研磨过程中的表面质量或干法刻蚀过程中的生产通量,那么晶圆减薄过程的成本将减少,因为只需要一种方法。总的来说,超薄晶圆制造过程中需要解决以下技术挑战:(a)晶圆厚度和总厚度变化(TTV)的控制;(b)表面损伤和残余应力的控制;(c)生产量和成本。
3. 超薄晶圆运输
在制造出超薄晶圆后,它需要进行相关操作,即晶圆的搬运方法。由于超薄晶圆的机械性能较差,因此它们的搬运非常困难。评估机械性能的主要指标包括弹性、塑性、刚度、强度和硬度。对于超薄晶圆,厚度的减小会影响其弹性、刚度和强度,其中超薄晶圆由于弹性增加/刚度减小,容易弯曲;而由于表面损伤引起的强度降低,容易发生破裂。Fukuda[42]发现,随着晶圆直径的增加,硅晶圆的剪切应力也会增大,这可能导致晶圆弯曲/翘曲。Namazu等人[43]报告了硅梁尺寸对(110)方向的杨氏模量影响较小,但对弯曲强度有较大影响。Colleti等人[44]使用环对环破裂测试仪测量了厚度在120至320 μm之间的薄晶圆的机械性能,发现破裂力F与晶圆厚度呈线性关系。考虑到超薄晶圆的机械性能较差,且其强度和刚度高度依赖于直径和厚度,如上所述,因此,开发便宜、高效且稳定的超薄晶圆搬运方法至关重要。
3.1. 超薄晶圆与载体
目前,将超薄晶圆与载体粘接在一起是超薄晶圆搬运的主流方法[45–48]。超薄晶圆与载体通过聚合物胶粘剂暂时粘接在一起,载体保护超薄晶圆免受破裂。当超薄晶圆与载体的相关工艺完成后,超薄晶圆将从载体上脱离。在此方法中,胶粘剂的性质对晶圆级暂时粘接过程的成功至关重要。超薄晶圆与载体临时粘接后,需要确保晶圆表面具有高平整度和较强的粘接强度,同时载体也应易于移除。
Jouve 等人[49]评估了一种新型可移除的高温旋涂胶粘剂在暂时粘接过程中的性能。结果表明,这种胶粘剂的特性,如粘接强度、化学抗性、热力学稳定性、可调脱离温度等,满足了要求,且在脱离载体和去除胶粘剂时不会对超薄晶圆中的通孔硅vias(TSV)结构底部造成损害。电气测量显示,基于临时载体的器件的via电阻与永久载体的值相同。
Pargfrieder 等人[50]详细报告了临时粘接与脱离的具体过程以及相关的考虑事项。超薄晶圆的粘接、脱离与清洗都在同一平台上进行。他们展示了这种技术是一种高效且低成本的方法,可用于超薄晶圆上的TSV制造。
在超薄晶圆通过临时粘接-脱离技术处理时,胶粘剂的去除效果起着决定性作用。目前,胶粘剂去除有两种方法。第一种方法是通过加热改变胶粘剂的粘度,从而将超薄晶圆与载体分离[49,51]。虽然这种方法相对简单,但存在局限性。如果温度过低,去除效果不理想;如果温度过高,可能会损坏器件。另一种胶粘剂去除方法是使用辐射(紫外线或激光)降解胶粘剂,改变粘度并去除粘接[52–54]。这种方法需要特殊的辐射设备,且成本较高,并且载体必须是透明的。
Shuangwu 等人[52]讨论了两种临时胶粘剂(紫外辐射和热固化)的热力学行为、稳定性及其对TSV过程的影响。结果表明,这两种胶粘剂各自有其局限性,需要根据具体的工艺条件选择合适的胶粘剂。此外,在3D超薄晶圆堆叠技术中,需要开发一种通过不同纵横比的vias孔进行连接的工艺。这种TSV工艺要求可靠的超薄晶圆搬运技术。临时粘接技术已成为3D堆叠技术中相对常见的超薄晶圆搬运方法。
Charbonnier 等人[55]描述了如何利用临时粘接工艺在70或120μm的超薄晶圆上制造直径为65μm的TSV。工艺结果表明,采用这种临时粘接工艺制造的8英寸超薄晶圆的参数满足下一步(3D集成切割和堆叠)的要求。Zoschke 等人[56]对临时粘接技术中的晶圆厚度减薄和背面工艺进行了系列评估。结果表明,临时粘接技术可以应用于3D集成系统。
使用临时粘接技术的超薄晶圆的一个问题是,由于存在胶粘剂和载体,难以精确测量晶圆的厚度。当前使用光学方法来测量超薄晶圆的厚度,但这种方法的结果容易受到粘接层材料和晶圆表面图案的影响。Kim[57]通过傅里叶变换红外光谱(FTIR)测量了超薄晶圆的厚度,并讨论了不同胶粘材料对测量厚度的影响。尽管这项研究的结果证明光学方法可以测量超薄晶圆的厚度,但这种方法的局限性仍然存在。例如,光学测量不适用于含有低透光材料的晶圆,对于胶粘剂薄弱或未粘接的晶圆,由于界面不清晰,光学测量的准确性也会降低。因此,需要开发一种能够在多层粘接晶圆系统中准确测量厚度的方法。
除了将超薄硅晶圆粘接到其他基板上外,硅晶圆本身也可以作为载体来粘接其他材料的超薄晶圆[58]。Daix 等人[59]展示了200mm InGaAs-on-insulator晶圆直接粘接到硅接收晶圆上。通过在InGaAs表面和硅接收晶圆上沉积20-30nm厚的Al2O3薄膜来保证粘接能量。粘接后,InGaAs的厚度可以通过后转移的CMP进一步减薄。这项技术将硅基薄膜的低功耗和背偏优势与InGaAs通道的高迁移率(通过霍尔效应测量为6000 cm²/V·s,通过场效应晶体管提取为2000–3000 cm²/V·s)结合起来。
3.2. 无载体超薄晶圆
对于没有载体的超薄晶圆,传统的持有装置通过与晶圆表面接触来固定晶圆,这种方式会导致污染和晶圆的机械应力/损伤。因此,应该采用非接触持有装置来进行超薄晶圆的运输。Siniaguine 等人[60]发明了一种用于晶圆状物品的持有装置,装置内至少有一个环形槽(图4a)。在直径为 d 的槽内气体流动,可以顺时针或逆时针循环(图4b),形成一个紧邻物品表面的涡流。根据伯努利原理(流体流速增加时,流体的压力会减小)[61],该涡流为物品提供动态支撑。
图4. 基于伯努利原理的超薄晶圆传输夹具:(a)气体流动环形槽集成夹具的俯视图;(b)气体流动环形槽集成夹具的侧视图;(c)夹具的距离依赖压力差;(d)用于超薄晶圆传输的多个环形槽应用的机器人臂
如图4c所示,当半径 r 小于 d/2时,周围的气压高于槽中气体的压力。这一正压差 ΔP 使得晶圆状物品被压向持有装置。另一方面,当半径 r 大于 d/2时,气体压力与周围气压之间的负压差 ΔP 会将晶圆状物品推出持有装置。这就是为什么晶圆状物品可以在不接触持有装置的情况下悬浮的原因。考虑到该持有装置根据上述动力学原理可以以任何方向持有晶圆而不接触持有装置表面,超薄晶圆的运输有两种工作模式:晶圆位于持有装置下方或位于持有装置上方。晶圆与持有装置之间的间隙高度 h 会与晶圆的重量 W 达到平衡。
如图4d所示,实际的超薄晶圆持有装置采用了多个环形槽,且持有装置的末端呈叉形,以防止晶圆旋转,其中蓝色虚线代表正在操作的超薄晶圆。显然,伯努利方法的优点在于能够减少超薄晶圆破损的风险并避免污染,因为晶圆和持有装置之间没有接触。因此,这种技术已经成为光伏工业中一种成熟的超薄晶圆搬运技术[62]。
然而,伯努利方法也确实存在一些局限性。首先,它不适用于大尺寸的超薄晶圆,例如12英寸超薄晶圆。最近,Liu 等人[63]开发了一种分布式伯努利夹持器,用于8英寸超薄晶圆的搬运,其中气流速率和间隙高度是两个关键操作参数。其次,伯努利方法也不适用于真空中的超薄晶圆运输,因为该方法依赖于压力差来操作晶圆。第三,当超薄晶圆在空气中高速移动时,空气阻力和晶圆的惯性力会加剧超薄晶圆的弯曲,甚至导致破损[64]。
另一种处理超薄晶圆的方法,适用于去载体装置晶圆和背面处理后的晶圆,是通过一种具有非粘附和低粘接强度接口的晶圆传输盘,提供全尺寸支持[65]。去载体装置晶圆的厚度通常小于200μm,甚至更优选小于100μm。如图5a所示,晶圆传输装置包含一个晶圆传输盘,盘的末端配有端效应器用于支撑,端效应器上延伸有一个细长的手柄。晶圆传输盘由热稳定材料(如金属、聚合物、玻璃和陶瓷)制成,厚度约为0.3-0.6cm。通过表面改性(如抛光和涂层)实现晶圆接触面的非粘附性质。为了防止超薄晶圆在传输过程中发生翘曲或弯曲,采用一个与晶圆传输盘形状和尺寸相同的顶部盘(图5b)。
图5. 用于薄晶圆传输的全尺寸支撑装置:(a)顶部盘、设备晶圆和晶圆传输盘的三明治结构;(b)从晶圆传输盘延伸出的长柄
上述超薄晶圆运输过程需要特殊设备来支持[49]。由于TAIKO晶圆的兴起以及通过干法刻蚀减小晶圆表面损伤的过程,超薄晶圆的传输将逐步向传统晶圆的处理工艺转变,且不再需要使用特殊设备。Bieck 等人[20]报告了一种带有裂缝结构的超薄晶圆,这种结构非常类似于TAIKO晶圆。由于减少了缺口附近的应力集中,这种没有载体的超薄晶圆的有效面积得到了增加。这种厚度为60μm的超薄晶圆可以在不使用晶圆支撑系统(WSS)的情况下进行搬运。与使用载体的超薄晶圆技术相比,无载体超薄晶圆技术在背面处理技术中同时整合了机械稳定性。
4.超薄晶圆应用
超薄晶圆制造和处理的终极目标是提供小尺寸和高性能的半导体器件制造。超薄晶圆在器件制造中有广泛应用,如3D封装/ TSV工艺[39,49,66–68],功率芯片[21,27],太阳能电池[69–71],射频识别(RFID)设备[1],互补金属氧化物半导体(CMOS)器件[32,72,73]等。
晶圆级芯片尺寸封装(WLCSP)能够实现规模经济,因为所有芯片都在晶圆上同时封装,而不是一次封装一个芯片,这完全符合联合电子器件工程委员会(JEDEC)和表面贴装技术(SMT)标准[66]。因此,在WLCSP中,芯片应以晶圆形式进行薄化,这要求超薄晶圆技术,其中晶圆厚度在各种对尺寸敏感的电子产品中是一个关键因素。此外,超薄晶圆还提供了几何上的优势,可以在芯片中创建通孔。随着市场对更小电子和光学器件需求的增长,减小集成电路封装的尺寸和重量变得愈加重要。对于超薄晶圆的封装过程,如薄化、处理和切割,尤其需要确保超薄晶圆在不破裂的情况下具有足够的强度。Vincent等[39]报告了晶圆薄化参数对芯片强度的影响,这影响半导体器件的完整性和可靠性。他们评估的晶圆薄化参数包括主轴转速、进给率和夹具台转速。研究发现,在粗磨过程中使用不同晶圆薄化参数时,芯片的强度是相似的,因为损伤层足够深。相比之下,当粗磨过程中晶圆的TTV(厚度变化)得到改善时,芯片强度会下降。对于没有承载体的超薄晶圆,Spiller等[18]报道了300毫米超薄晶圆的制造过程,并依次验证了300毫米超薄晶圆的机械稳定性。在超薄晶圆上旋涂、曝光和显影聚合物后,通过物理气相沉积(PVD)和电镀沉积Ti和Cu。这一工艺可应用于TSV封装和功率器件。实验结果还证明,与带有承载体的超薄晶圆相比,通过此工艺制造的超薄晶圆(无承载体)在成本上具有明显优势。此外,DISCO GmbH已开发出一些超薄晶圆技术的先进技术,如TAIKO晶圆、激光切割等。还可以将等离子刻蚀技术引入基于TAIKO超薄晶圆的TSV工艺[74]。
除了在封装过程中的几何优势外,超薄晶圆还可提高功率芯片的器件性能[18,21]。芯片的源极到漏极的开启状态电阻RDS(on)是功率芯片的关键性能指标之一,它应尽可能低,以便将高电流传导到负载(最小化能量损耗)。
图6. 功率器件中电阻的示意图,显示Rsub依赖于晶圆厚度,但不具有关键电气功能。
如图6所示,典型的垂直结构场效应晶体管(FET)主要包含门电极、源电极和漏电极,其中源漏电流可以通过门电极进行调节。具体来说,这是一个NPN型FET的示意图,具有增强模式。当在门电极上施加正电压时,n型半导体中的电子(在源极和漏极中)被驱动到门电极(门电极的氧化层或肖特基接触可以防止门泄漏电流),形成开启状态的源漏电流IDS(on)。当在门电极上施加负电压或零电压时,高通道电阻Rch可以使器件关闭。与传统的机械功率开关相比,功率芯片通过门电极调节开关的方式可以实现高速开关并避免不受控制的火花。虽然RDS(on)由许多单独的电阻组成,但在电流通过整个晶圆的垂直结构器件中,器件的厚度对RDS(on)有很大影响。考虑到器件的主要电气功能是由晶圆表面几十微米深度的区域提供的,晶圆厚度的其余部分仅增加了功率芯片的电阻Rsub,应该尽可能低(如图6所示)。因此,超薄硅晶圆可以在功率芯片中提供更好的器件性能。例如,绝缘栅双极型晶体管(IGBT)是一种典型的功率芯片,具有高开启电流和快速开关速度,要求晶圆厚度为120 μm或更薄。这是因为当IGBT器件的晶圆变薄时,功耗较小,集成密度较大。由于TAIKO晶圆具有翘曲和运输的优势,因此已在场停绝缘栅双极型晶体管(FS-IGBT)制造中得到应用[27]。随着具有宽带隙的第三代电子材料(如氮化镓和碳化硅)的出现,功率器件甚至可以更薄(与硅相比理论上厚度可减至1/10)。
类似地,太阳能电池也是寻求超薄晶圆技术的另一种器件,这是因为较低的晶圆厚度能够降低内部电阻。较大的内部电阻会增加光生载流子的复合概率,这可能降低开路电压[69]。此外,超薄晶圆制造的太阳能电池具有柔性、低成本并兼容薄膜技术。然而,与功率芯片不同,对于太阳能电池制造而言,过薄的晶圆厚度并不一定更好。这是因为晶圆过薄会减少光的吸收,从而降低功率转换效率(PCE)。因此,在工业生产线中,太阳能电池制造用的晶圆通常厚度为120–200 μm。最近,通过理论和实验研究,超薄晶圆在太阳能电池制造中的厚度已被证明具有进一步减薄的潜力。Han等[70]通过群论设计了薄晶体硅太阳能电池中的表面纳米结构,朝着兰伯特极限的吸收方向发展,表明进一步减薄硅的厚度或质量具有潜力。至于实验研究,Zhang等[71]证明了等离子纳米结构是增加光捕获的有效策略,在这种情况下,晶圆的厚度可以减少到原厚度的约10%,而没有明显的PCE损失,证明了在最小效率损失的情况下减小硅晶圆厚度是发展晶体硅太阳能电池的可行方法。
此外,射频识别(RFID)是通过射频识别实体而无需物理接触[1]。超薄晶圆将为RFID集成到薄膜甚至纸质文件中提供可能。薄RFID技术还促进了使用有机化合物制造电子晶体管,其中可以实现高速率的数据传输。
此外,超薄晶圆还被应用于CMOS器件的制造。在湿化学薄化工艺后,Watanabe等[32]通过透射电子显微镜(TEM)和电子能量损失谱(EELS)分析了刻蚀表面和芯片的断裂应力。尽管这种湿刻蚀工艺引入的断裂应力高于其他薄化工艺(如背面磨削工艺),但当将CMOS晶圆通过该湿刻蚀工艺薄化至50 μm时,MOSFET性能变化较小。Kim等[73]使用高分辨率磨削技术,并配备Auto-TTV和非接触测量仪(NCG)方法,将晶圆厚度减至10 μm以下。对超薄晶圆对CMOS逻辑和FRAM器件电性能的影响的测量表明,粘接、薄化和解粘过程对器件的电性能没有影响。在此基础上,他们[72]首次将300毫米晶圆薄化至4 μm,用于40纳米节点的2GB DRAM,并且超薄晶圆表面均匀性约为1 μm。晶圆薄化后,2GB DRAM的保持和分布特性没有恶化,表明粘接和解粘过程不会对器件造成损伤。这些结果表明,CMOS逻辑器件、FRAM和DRAM存储器器件可以实现3D集成。
5.结论与展望
总而言之,随着近年来半导体器件集成密度、器件性能和市场需求的不断增加,超薄晶圆已成为半导体器件制造中的重要组成部分。晶圆厚度的减少意味着相应的超薄晶圆制造和操作的难度增加。这些过程是集成的,不能单独考虑,并与超薄晶圆的应用一起进行。机械研磨后通过抛光或刻蚀进行应力释放已成为标准的晶圆薄化过程,并且随着TAIKO晶圆的兴起,超薄晶圆的运输将不再需要特殊设备。因此,超薄晶圆对半导体工业产生了重大影响,在当前的状态下具有广泛的应用。
展望未来,超薄晶圆的研究仍然是一个热门话题,相关研究将全力开展。对于超薄晶圆制造,毫无疑问,超薄晶圆将变得越来越薄,未来的厚度可能只有几个微米甚至数百纳米,在这种情况下,干法刻蚀应成为获得超薄晶圆的必不可少的方法。相应地,干法刻蚀的发展主要有两条路线。一条是提高刻蚀速率或制造吞吐量,另一条是扩展其固有的有效应力释放或去除损伤的优势【75】。
遵循摩尔定律,由于器件越来越小,对晶圆表面质量的需求也在增加。通过干法刻蚀改善晶圆粗糙度可以减少外延过程中的问题,甚至消除这些问题。对于超薄晶圆的操作,伯努利方法将得到改进,以处理大尺寸的超薄晶圆。随着半导体工业中自动化水平的提高,寻求减少超薄晶圆运输的时间和距离。对于超薄晶圆的应用,更多种类的器件可能采用超薄晶圆。例如,在微机电系统(MEMS)器件中,超薄晶圆能够带来灵活性,使可穿戴设备与传统硅电子兼容。超薄晶圆还可以减少可植入设备在活体生物体中的退化时间。总之,超薄晶圆技术对科学和工业界都具有重要价值,并将在不久的将来具有更广泛的应用。