#先进逻辑电路 #团簇离子束抛光 #GCIB抛光
摘要
在14纳米以下的先进CMOS逻辑技术中,控制晶圆级的平整化或均匀性变得极为关键。这主要是由于CMOS集成方案中使用化学机械抛光(CMP)来形成晶体管栅极。精确的栅极高度控制至关重要,因为晶圆或芯片内任何非均匀的栅极高度都可能导致器件性能和良率的下降。尤其是,在先进CMOS技术中,晶圆级平整化的技术要求已经超出了传统CMP工艺的能力范围。这一技术限制促使了对替代集成方案或平整化技术的需求。使用定位特定的气体团簇离子束(GCIB)进行晶圆级平整化被认为是一种潜在的技术,可以满足这一严格要求。
本文解释了GCIB技术的基本原理,并探讨了其在CMOS集成中的潜在应用。
关键词:气体团簇离子束,化学机械抛光,平整化,定位特定工艺,均匀性
@GCIB抛光代工@
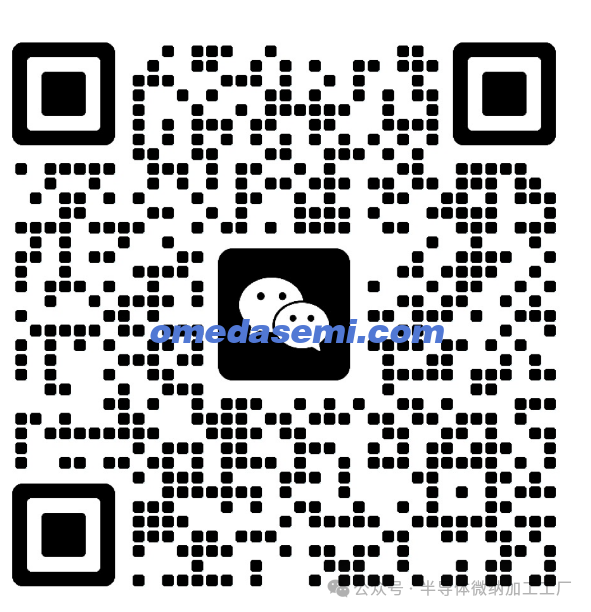
1 引言
GCIB是一种由气体分子团簇组成的聚焦束,可以在分子尺度上去除表面材料。气体团簇是通过高压气体混合物的体积膨胀和绝热膨胀导致的冷凝形成的。然后,气体团簇被电离并加速到晶圆表面。在撞击晶圆表面之前,束流会被中和,以防止因静电放电(ESD)而损坏器件。气体团簇撞击晶圆表面分子,并通过物理和化学方式去除表面材料。去除的材料量由施加在气体团簇上的总能量和气体团簇分子组成控制。尽管总能量较高,但单个团簇分子上的能量较低,且气体团簇不会造成任何表面下的损伤。单个团簇去除的材料深度范围为2纳米到20纳米,如图1所示。GCIB冲击区域内表面的温度可达到10,000°C,但持续时间极短,不超过10皮秒,其余材料仍保持在室温下。[1]
图 1:气体团簇离子束 (GCIB)
特定位置处理 (LSP) 可以显著改善晶圆内的均匀性,其效果远优于 CMP 工艺控制的最佳轮廓(图 2)。每个晶圆都使用机载计量系统进行预处理测量。此预测量确定了晶圆表面“不均匀性”的位置。
晶圆表面特定位置的离子束持续时间由晶圆卡盘的摆动运动控制。当晶圆以最高 150 cm/s 的速度在摆动运动中来回振荡时,晶圆也会在扫描之间以 1-2 mm 的典型间距向上移动。此运动创建了完整的晶圆扫描运动和 LSP 映射,如图 3 所示。LSP 算法通过降低晶圆扫描运动速度,使气体团簇离子束击中非均匀位置时晶圆停留更长时间。GCIB 工艺配方使用自动工艺控制 (APC) 算法,根据预测测量数据针对每个晶圆进行更新。
图 4:GCIB 系统
晶圆从装载口拾取并移动到机载计量系统进行预测测量(图 4)。测量完成后,晶圆通过晶圆传送室移动到工艺腔体,以控制并维持工艺腔体内部适当的真空度。GCIB 工艺结束后,晶圆返回装载口。晶圆可在机载计量系统上进行再次测量,以检查 GCIB 后的膜厚。
2 GCIB 应用
2.1 虚拟多晶硅栅极平坦化
GCIB 在先进 CMOS 逻辑技术中的潜在应用之一是 FinFET 器件的虚拟多晶硅栅极平坦化(图 5)。
图 5:虚拟多晶硅栅极平坦化
10 纳米以下逻辑技术的集成要求给化学机械抛光 (CMP) 工艺带来了重大挑战。采用 LSP 技术的 GCIB 可以作为 CMP 工艺的补充步骤提供工艺支持,以确保晶圆的均匀性符合工艺规范。
在 FinFET 器件制造过程中,虚拟多晶硅栅极沉积在 FIN 结构的顶部。为了平坦化该多晶硅表面,需要多个 CMP 步骤和“多个”其他工艺步骤。这是因为我们需要满足严格的工艺规范,以控制芯片内和晶圆尺度内虚拟多晶硅栅极的高度。经过多晶硅 CMP 和平坦化步骤后的多晶硅高度将直接转移到虚拟多晶硅栅极,并最终转移到替代金属栅极模块中的金属栅极。因此,控制CMP和其他平坦化步骤后剩余多晶硅膜的高度至关重要。
我们提出的方案是仅使用多晶硅CMP和GCIB步骤来平坦化多晶硅膜。这简化了整体多晶硅平坦化集成方案,同时保持了芯片内和晶圆内多晶硅高度的规格。
图 6:通过支持 LSP 的 GCIB 进行多晶硅平面化多晶硅沉积后,采用传统的多晶硅CMP工艺对晶圆进行处理,对多晶硅膜进行初步平坦化。CMP后晶圆内非均匀性可高达100-150A。
在GCIB工艺之前对同一晶圆进行测量,以创建特定的LSP图。GCIB后晶圆的晶圆内非均匀性改善了7-10倍。LSP算法能够提供良好且稳定的均匀晶圆表面。
图 7:GCIB 蚀刻量对均匀性的改善
需要去除的材料量取决于我们需要平坦化的薄膜的均匀性范围。随着轮廓的逐渐变化,需要去除的厚度通常与薄膜的不均匀性相对应。薄膜的不均匀性越高,GCIB 需要去除的材料量就越大,如图 8 所示。更大的材料去除量要求会因工艺时间延长而降低工艺产量。
图 8:不同 GCIB 蚀刻量下均匀性改善情况
3 GCIB 在半导体制造中的应用
氧化物表面的表面粗糙度与 GCIB 处理的氧化物晶圆进行了比较。由于材料去除工艺是通过气体分子团簇轰击进行的,因此预计会产生一定的表面粗糙度。然而,SEM 分析显示,无论是否采用 GCIB 工艺,氧化物表面的表面粗糙度几乎相同。
图 9:氧化物表面的 SEM 图像
为了验证 GCIB 工艺的可制造性,我们进行了多次工艺马拉松测试和日常工艺鉴定,如图 10 所示。
图 10:去除速率和缺陷率的工艺鉴定
扩展工艺马拉松测试和每日鉴定也证明了 GCIB 工艺控制的稳定性。由于 GCIB 工艺和系统的先进可控性,去除速率和缺陷率的每日鉴定规范远超传统 CMP 工艺鉴定。在三个工艺参数中,表面均匀性的 sigma 表现出极其一致的可控性。总体偏差小于 5A。
4 结论
本文阐述了气体团簇离子束 (GCIB) 工艺的基本原理、其在半导体制造工艺中的应用及其可制造性。GCIB 工艺展现出卓越的轮廓控制能力,超越了传统 CMP 工艺的极限。
在先进技术节点中,CMP工艺开始用于制造金属栅极后,对晶圆内和芯片内均匀性的要求变得极为严格。特别是,膜内停止CMP工艺可能无法达到如此严格的均匀性规范。在某些集成方案中,需要额外的工艺步骤才能达到这种严格的均匀性规范。GCIB可以作为一种替代工艺,以实现这种严格的晶圆内均匀性。尽管GCIB由于无法平坦化进入的表面形貌而无法取代CMP,但它可以作为一种补充工艺,辅助CMP实现严格的晶圆级均匀性。由于GCIB在实现良好晶圆级均匀性方面具有卓越的能力,其应用范围可以扩展到本文中讨论的虚拟硅平坦化应用之外。