本研究探究了节距尺寸在超构透镜设计中实现高数值孔径(NA)和聚焦效率方面所起的作用,同时展示了高折射率材料如何通过降低填充比实现更小的节距尺寸,从而提升性能。由于富硅氮化物(SRN)具有高折射率、与互补金属氧化物半导体(CMOS)工艺兼容以及制造成本低等特性,因此被选作材料平台。研究人员设计了两款基于SRN的超构透镜:一款是几何相位超构透镜(GPM),另一款是传播相位超构透镜(PPM),并分别在纵横比为10 : 1和4 : 1的条件下对它们进行了评估。GPM实现了0.99的数值孔径,在纵横比为10 : 1时聚焦效率为26.6%,在纵横比为4 : 1时聚焦效率为17.6%;而PPM实现的数值孔径在纵横比为10 : 1时为0.95,在纵横比为4 : 1时为0.97,相应的聚焦效率分别为65.6%和32.1% 。我们的研究结果表明,更小的节距尺寸能够减少空间离散化误差,提高相位保真度和聚焦效率,这适用于成像和偏振测量等多种应用场景。
针对本文中作者的实验:
*比作者团队更好的加工条件,Jeol9500+DUV-KRF 150nm,
*PECVD SIN薄膜,带折射率数据
*氮化硅可见光波段超透镜全流程加工
大面积超结构及其他微纳结构加工解决方案
背景:
目前在市场上大家加工超结构的加工方式主要为ebl+干法刻蚀。这种加工方式的优点是,精度高,金属类结构可以达到50nm线宽,氧化物和氮化物可以达到80-100nm的最小线宽。
但是由于采用的方式为电子束光刻的方式,因此成本是巨大的,举例,一个1mm*1mm的图案差不多2-3万元,而一个20*20mm的图案,差不多就要20万元左右。
雪上加霜的是,我们付出了如此大的代价,最后只能得到一个样品,这个样品的宝贝程度不亚于金子,这样我们在做实验的时候,就像拿着宝贝疙瘩一样谨慎、生怕弄坏了。
紫外光刻技术相对于电子束光刻技术,具有较好的量产效率和较低的量产成本。
国内有很多超结构企业,目前遇到的一个核心困境就是国内缺足够的高精度的光刻机 比如几十nm线宽的12寸量产型光刻机,因此国内很多超结构企业的流片都在国外fab厂进行。
针对国内的科研工作者的超结构及其他微纳结构加工难题;
小编正式推出
6寸最小线宽150nm 超结构及微纳结构 镀膜+光刻+刻蚀 一站式服务
采用佳能krf紫外光刻机,最小线宽150nm,比例5:1,成本主要包含 掩模版 镀膜 光刻 刻蚀这4套基本工艺流程,其中最贵的掩模版为一次性投入,其余为做单片时的投入。性价比超高,每次加工可得一整个晶圆 。
当然 ,本方案的缺点在于,设备的最小线宽仅为150nm,更高精度可能还是需要寻求更高精度的光刻机或者ebl加工。
设备:佳能150nmDUV光刻机
尺寸:6英寸
最高可加工精度:150nm
6寸超结构整版加工预计成本:3-6万(单片),
其中掩膜版为一次性投入,后续增加片数仅收取光刻,刻蚀费用。
最大单元尺寸:22*22mm
对准精度:40nm
材料:非晶硅,TiO2,SiO2,LiNbO3,Si3N4 GaN,Ta2O5,Al,Au,GaAs...更多材料体系
应用领域:超结构,光栅,mems,光子集成线路,,,,,,
请联系小编免费获取原文,也欢迎交流半导体行业,工艺,技术,市场发展!
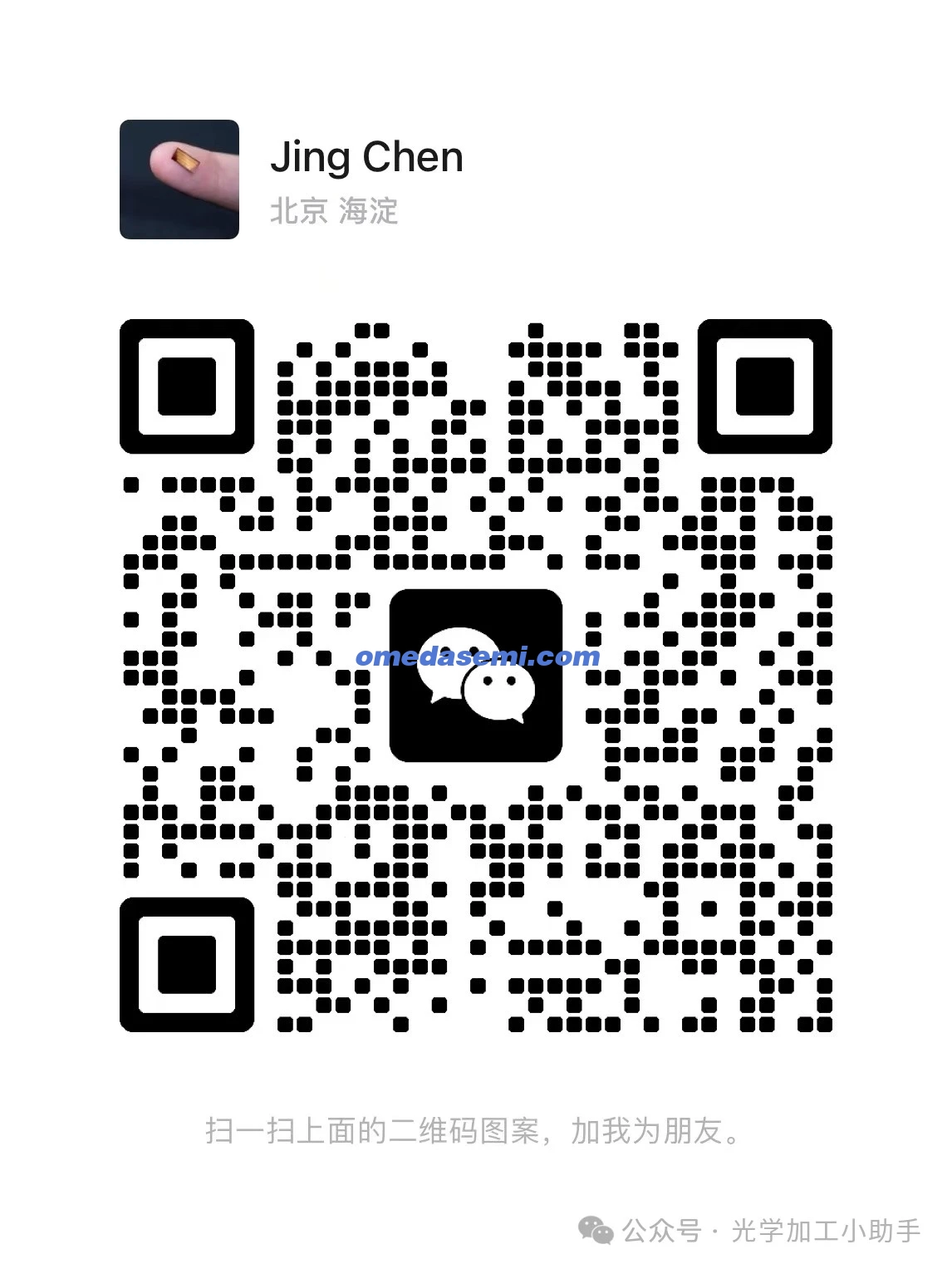
超构透镜凭借其尺寸微小、相位控制精确、具备偏振操控能力、功能多样、材料适用性广以及可能实现低成本制造等特性,相比传统透镜具有诸多实际优势[1]。这为其开拓了广泛的应用领域,涵盖从消色差成像[2]、颜色路由[3]、超全息图[4]到全斯托克斯偏振测量[5]等。在此之后,研究人员提出利用不同材料,如二氧化钛(TiO₂)[6]、晶体硅(c - Si)[7]、非晶硅(a - Si)[8]和氮化镓(GaN)[9],来制造具有高数值孔径(NA)的高效超构透镜。在庄等人的研究中,作者基于矢量衍射理论开发了一个理论模型,并使用二进制粒子群优化(BPSO)算法优化了为实现高效亚衍射聚焦而设计的单层介质超构透镜的相位分布[10]。他们采用TiO₂纳米柱的设计在532nm波长处实现了0.95的高数值孔径,聚焦效率和透射效率分别为17.2%和77.6%。在另一项研究中,桑等人展示了通过拓扑优化开发的高效、超高数值孔径自由曲面超构透镜[11]。作者探讨了传统基于单元结构设计的局限性,这些局限性与离散相位采样、局部周期性近似和法向响应有关,会影响高数值孔径超构透镜的效率。优化后的超构透镜在数值孔径为0.95时实现了34.2%的聚焦效率。范等人提出了一种能够实现超宽视场(FOV)且具有高聚焦效率的超构透镜设计[9]。所提出的基于GaN的超构透镜设计工作波长为532nm,在垂直入射时展示出0.25的数值孔径和高达82%的聚焦效率。在另一项研究中,梁等人[7]介绍了一种基于c - Si的超构透镜,在空气中数值孔径高达0.98,在532nm波长处聚焦效率为67%。尽管使用TiO₂、c - Si和GaN等材料设计的超构透镜展现出优异的光学性能,但其制造工艺通常较为复杂,且与互补金属氧化物半导体(CMOS)技术不完全兼容。这些工艺通常涉及原子层沉积(ALD)或金属有机化学气相沉积(MOCVD)等先进技术,既耗时又成本高昂,限制了其大规模生产的可扩展性。此外,提升超构透镜性能往往依赖于结构参数和功能特性的优化,如相位分布设计、像差校正[12]以及节距尺寸控制。特别是,减小节距尺寸对于最小化波前的空间离散化效应至关重要。然而,这种减小受到填充比的限制,填充比是超原子占据单元面积的比例。像TiO₂和GaN等折射率较低的材料,需要较高的填充比才能实现完整的2π相移。因此,这会导致更大的单元尺寸,限制了可实现的节距大小,并降低了设计效率。在这方面,富硅氮化物(SRN)已成为用于超表面的一种优势材料。其高折射率、制造过程中易于调节、与CMOS兼容、制造工艺简单以及长期稳定性,使其特别适合用于可见光范围内的光学器件[13]。最近的研究展示了SRN在实现人工聚焦图案和惠更斯超全息图方面的潜力[14,15]。我们之前的工作[16]进一步强调了基于SRN的亚波长光栅超构透镜的能力及其在可见光范围内的应用。本研究表明,基于SRN的超构透镜可通过节距尺寸控制实现高数值孔径和聚焦效率。利用SRN与CMOS兼容、制造工艺简单低成本以及高折射率的特性,这些超构透镜克服了许多与其他常用材料相关的限制。通过这项工作,我们验证了节距尺寸对聚焦效率的影响,并展示了SRN的高折射率如何在小节距尺寸内实现完整的2π相移范围,减小单元尺寸并提高相位分辨率。为了说明节距尺寸对聚焦效率的影响,我们提出了两种不同的超构透镜设计:一种是为右旋圆偏振(RCP)光设计的几何相位超构透镜(GPM),另一种是为线偏振光设计的传播相位超构透镜(PPM),两者均在685nm波长下工作。这些设计表明,小节距尺寸和高折射率材料的优势与偏振状态无关。在宽高比为4:1和10:1时,GPM在两种情况下均实现了0.99的数值孔径,聚焦效率分别为17.6%和26.6%,而PPM的数值孔径分别为0.97和0.95,聚焦效率分别为32.1%和65.6%。超构透镜的研制基于以特定图案排列亚波长纳米结构,以在透镜表面形成变化的相位分布。这种相位变化由以下公式描述:

其中,\(\phi(x, y)\)表示透镜表面给定位置\((x, y)\)处的相移,\(\phi_0\)是透镜中心的初始相位。参数\(\lambda\)对应入射光的波长,\(f\)是透镜的焦距。这个公式在超构透镜设计中至关重要,通过调制透镜表面的相位,能够实现对光的精确控制。通过使用高折射率材料,并将其分布在亚波长段上,可以调整每个点的有效折射率,从而控制光的透射和相移。在超构透镜设计中,聚焦光的效率从根本上与透镜表面相位操控的精度相关。这个过程中的一个关键因素是节距尺寸,用\(P\)表示,它是相邻纳米结构之间的周期或中心距。控制节距尺寸有助于减轻波前空间离散化的影响,这直接影响散射面积,散射面积由\(P×X_s\)给出,其中\(X_s\)是相邻周期之间的光程差,如图1(a)所示。光程差\(X_s\)可以用数学公式表示如下:

这里,\(x\)是超构透镜上的位置,\(f\)是焦距,\(n\)是介质的折射率。减小节距尺寸\(P\)会减小散射面积,从而实现精确的相位控制并提高聚焦效率。图1(b)展示了节距尺寸和相位保真度之间的关系。顶行显示相位图,其中理想的相位分布形成平滑的同心环,而离散的相位分布呈现阶梯状近似。底行展示径向相位图,理想相位是一条平滑曲线,离散相位是阶梯状近似。小节距类似于奈奎斯特采样定理中的高采样频率,能够更好地捕捉相位信息,减少量化误差并提高效率。大节距类似于信号处理中的欠采样,不满足奈奎斯特准则,会引入偏差,从而降低光学性能。节距尺寸\(P\)和聚焦效率之间的关系还可以通过瑞利 - 甘斯近似进一步说明。当散射体尺寸远小于光波长除以折射率的绝对差值\(\vert n - 1\vert\)时,瑞利 - 甘斯近似是适用的:
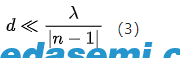
与\(P\)相关的尺寸\(d\)表明,随着\(P\)的减小,每个纳米结构越来越像一个理想的点散射体,根据瑞利 - 甘斯近似,这会减少衍射和像差效应,从而提高聚焦效率。对于GPM和PPM,SRN层的高度\(h\)均设置为600nm,同时调整GPM的角度\(\theta\)(图2(b))以及PPM的长度\(L\)和宽度\(W\)方向的横向尺寸,以实现最佳的相移和透射特性(图2(c)和2(d))。补充材料1(图S1)提供了PPM其他单元节距尺寸的额外相位和透射特性。对于GPM,在所有研究的节距尺寸下,透射率始终保持在92%以上,进一步证实了其稳健的光学性能。此外,为了防止由于相邻超原子之间间距不足而形成共振模式(这会导致场重叠并激发不需要的共振),我们使用以下公式计算最小节距尺寸\(P_{min}\):
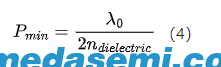
基于这些理论考虑,为GPM和PPM选择310nm作为最小节距尺寸,作为超构透镜设计的基线,这既满足制造限制,又作为评估节距尺寸影响的起点。超原子的尺寸也相应调整,相邻超原子之间的间隙固定为60nm。这种配置产生了10:1的纵横比,确保与制造限制兼容[16]。此外,我们分析了纵横比降低为4:1的超构透镜的性能,这种比例在制造时具有更高的可靠性和更好的重复性。对于这个比例,GPM和PPM均采用390nm的节距尺寸来实现完整的2π相移(见补充材料1中的图S1(i) - S1(k))。如本文后面所示,不同纵横比的两种透镜的性能与其他报道的由各种材料制成的超构透镜相当(表1)。补充材料1的第2节提供了关于单元结构、透镜设计和模拟条件的更多细节 。

图1. (a) 小节距尺寸(P)和大节距尺寸下光程差(Xs)的示意图 。(b) 透镜相位分布的对比:理想的连续相位分布,以及节距为250nm和500nm时的离散近似相位分布。下方的径向相位图显示,节距尺寸越小时,相位变化越平滑。

图2. (a) 单元结构的尺寸与材料。(b) 不同节距尺寸下,几何相位超构透镜(GPM)单元结构的相移随角度(θ)的变化情况。(c) 节距为310nm(纵横比10 : 1)的传播相位超构透镜(PPM)单元结构的相移(单位:弧度)随长度(L)和宽度(W)的变化 。(d) 节距为310nm(纵横比10 : 1)的PPM单元结构的透射率随长度(L)和宽度(W)的变化。
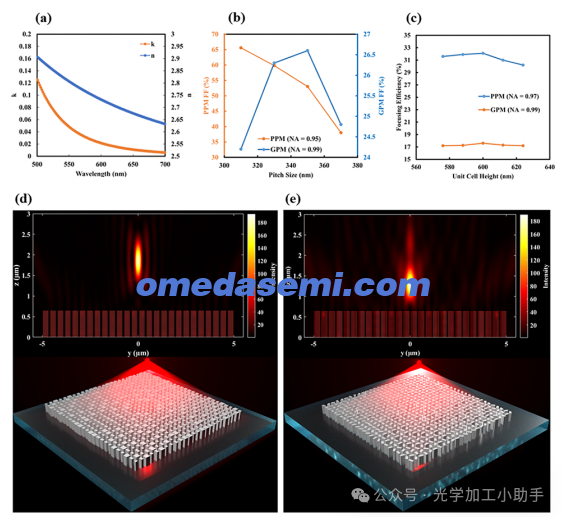
图3. (a) 600纳米厚富硅氮化物(SRN)薄膜的实测折射率n和消光系数k的值。(b) 聚焦效率随节距尺寸的变化情况(纵横比为10:1)。(c) 制造公差对几何相位超构透镜(GPM)和传播相位超构透镜(PPM)设计的聚焦效率的影响(纵横比为4:1)。(d) 数值孔径为0.97的PPM的三维示意图及电场强度平方(|E|²)分布 。(e) 数值孔径为0.99的GPM的三维示意图及|E|²分布。
为确保模拟结果能准确反映超构透镜的实际性能,我们通过等离子体增强化学气相沉积(PECVD)及椭圆偏振光谱测量过程,精确测量了折射率\(n\)和消光系数\(k\)(图3(a))。从\(n\)和\(k\)的值可知,选择685nm波长对于最小化材料损耗至关重要,这使我们能够分离出节距尺寸的影响。此外,该波长广泛应用于荧光测量以及植物叶绿素含量成像,进一步凸显了我们超构透镜设计的实际应用价值[17]。超构透镜的性能评估聚焦于关键指标:聚焦效率、数值孔径(NA)和半高宽(FWHM)(详细内容见补充材料1的第1部分)。通过控制节距尺寸并利用富硅氮化物(SRN)的高折射率,对几何相位超构透镜(GPM)和传播相位超构透镜(PPM)的设计进行优化,以实现高数值孔径、高效率的超构透镜。需要注意的是,本研究中的所有透镜均设计为边长10μm的正方形布局,并以正方形晶格结构排列(圆形布局超构透镜的性能见补充材料1的第4部分)。为研究节距尺寸对聚焦效率的影响,我们对各种节距尺寸进行了系统分析 。
表 1. 各类超构透镜对比
材料 | 数值孔径(NA) | 效率(%) | 半高宽(FWHM) | 焦距 | 节距尺寸(nm) | 特征尺寸(nm) | 波长(nm) |
---|
[10] 二氧化钛(TiO₂) | 0.95 | 17.2 | 0.429λ | 3.29μm | 320 | 117 | 532 |
[18] 硫化锌(ZnS) | 0.8 | 26 | 263nm | - | 200 | 40 | 405 |
[11] 二氧化钛(TiO₂) | 0.95 | 34.2 | - | - | 350 | 100 | 632 |
[7] 晶体硅(c - Si) | 0.98(实测) | 67(实测) | 277nm(实测) | 0.274μm(实测) | 220 | 20 | 532 |
[19] 富硅氮化物(SRN) | 0.98(实测) | - | 364nm(实测) | 10μm(实测) | 416 | 170 | 633 |
[9] 氮化镓(GaN) | 0.25 | 82 | - | - | 350 | 50 | 632 |
几何相位超构透镜(GPM,10:1)富硅氮化物(SRN) | 0.99 | 26.6 | 0.56λ | 0.69μm | 350 | 90 | 685 |
传播相位超构透镜(PPM,10:1)富硅氮化物(SRN) | 0.95 | 65.6 | 0.83λ | 1.62μm | 310 | 60 | 685 |
几何相位超构透镜(GPM,4:1)富硅氮化物(SRN) | 0.99 | 17.6 | 0.56λ | 0.69μm | 390 | 150 | 685 |
传播相位超构透镜(PPM,4:1)富硅氮化物(SRN) | 0.97 | 32.1 | 0.74λ | 1.24μm | 390 | 150 | 685 |
图3(b)突出展示了节距尺寸变化产生的影响,在纵横比为10:1的情况下,几何相位超构透镜(GPM)的数值孔径(NA)达到0.99,传播相位超构透镜(PPM)的数值孔径达到0.95。对于最佳节距尺寸,节距为350nm的GPM在焦距为0.69μm时实现了0.99的数值孔径以及26.6%的聚焦效率;而节距尺寸为310nm的PPM在焦距为1.62μm时展现出0.95的数值孔径以及65.6%的聚焦效率。使用半高宽(FWHM)来评估分辨率的话,GPM的半高宽为0.56λ,PPM的半高宽为0.83λ。在纵横比降为4:1时,GPM保持0.99的数值孔径,在焦距为0.69μm时实现了17.6%的聚焦效率;而PPM受衍射极限限制,达到了0.97的数值孔径,在焦距为1.26μm时聚焦效率为32.1%。这些设计中,GPM的半高宽为0.56λ,PPM的半高宽为0.74λ。为评估所提出的超构透镜对制造误差的耐受性,我们分析了它们在结构高度变化情况下的性能表现。图3(c)展示了纵横比为4:1的PPM和GPM在设计高度±4%的范围内变化时的聚焦效率。两种设计的聚焦效率都出现了轻微变化,这很可能是由这些高度变化导致的相位失配引起的。GPM设计展现出相对稳定的性能,偏差较小,仅为2.4%,而PPM设计的波动则稍显明显,达到了5.8%。图3(d)展示了GPM的三维模型以及在焦点处的电磁场分布(|E|²)的横截面强度情况,图3(e)则展示了在入射波长为685nm时,PPM对应的三维示意图以及焦点处的|E|²情况。模拟结果显示,当改变单元结构的参数时,聚焦效率还会受到单元结构相位响应函数线性度(通过线性拟合的\(R²\)值来量化)的影响(详见补充材料1的第3部分)。对于PPM单元结构的参数扫描,\(R²\)值相对稳定地保持在0.92左右。相比之下,对于GPM单元结构的参数扫描,\(R²\)值会根据填充比和节距尺寸产生波动。就GPM而言,节距尺寸为350nm时性能最佳,聚焦效率达到26.6%,这与该350nm节距尺寸下观察到的最高\(R²\)值相吻合。然而,对于更小的节距尺寸,尽管节距变小了,但聚焦效率却下降了,同时\(R²\)值也随之降低。相反,对于更大的节距尺寸,尽管\(R²\)值为0.97,但由于节距尺寸的影响,聚焦效率依然会下降。对于PPM来说,在节距尺寸为310nm时,整个透镜的模拟结果显示聚焦效率为65.6%。由于PPM的\(R²\)值始终保持一致,由此可以推断,在较大节距尺寸下观察到的聚焦效率下降主要归因于节距尺寸的增大,而非\(R²\)值的波动。这些数值模拟全面展示了节距尺寸对聚焦效率的影响,验证了所提出的透镜在受控条件下的性能表现。与我们之前的研究[16](该研究在传播相位超构透镜(PPM)的背景下简要讨论了节距尺寸的影响)相比,当前这项工作通过纳入几何相位超构透镜(GPM)和PPM,进行了更详细的研究,使我们对节距尺寸的影响有了更广泛的理解。为评估我们所提出的纵横比为10:1和4:1的超构透镜的性能,我们将其关键指标与此前报道的使用各种材料制造的一系列超构透镜进行了对比,相关内容总结在表1中。在该表中,与互补金属氧化物半导体(CMOS)工艺兼容的材料以蓝色突出显示,不兼容的材料则以红色显示。像晶体硅(c - Si)[16]这类材料由于其高折射率,能够实现较高的聚焦效率(高达67%)以及较小的节距与超原子尺寸之比。然而,这些优势是以制造复杂性为代价的,其制造需要高温工艺以及蓝宝石衬底,这限制了其可扩展性和成本效益。基于二氧化钛(TiO₂)的超构透镜[19]依赖于缓慢且昂贵的原子层沉积(ALD)工艺,这使其在大规模应用方面不太实用。相比之下,本研究中提出的基于富硅氮化物(SRN)的超构透镜实现了CMOS兼容性、成本效益、制造工艺简便以及高折射率之间的平衡组合。尽管我们提出的超构透镜在示例中没有实现最小的节距尺寸或最高的聚焦效率,但它展示了高折射率材料如何在保持制造可行性的同时实现具有竞争力的性能。总之,我们证明了节距尺寸在超构透镜实现高数值孔径和聚焦效率方面起着关键作用,且这一作用与透镜的偏振敏感性无关。以富硅氮化物(SRN)作为材料平台,我们分析了分别为右旋圆偏振(RHCP)光和线偏振(LP)光设计的两种超构透镜结构——GPM和PPM的性能。对GPM和PPM进行评估后发现,它们分别实现了0.99和0.95的最佳数值孔径,聚焦效率分别为26.6%和65.6%。在纵横比降为4:1时,GPM和PPM仍保持了具有竞争力的性能,聚焦效率分别为17.6%和32.1%。此外,分析还揭示了由\(R²\)值量化的单元结构相位响应线性度与节距尺寸在实现精确相位控制方面的相互作用。这些研究结果为高性能超表面的设计原则提供了有价值的见解。