砷化铟(InP)双异质结双极晶体管(D-HBT)技术可以与硅技术(例如,绝缘体上硅(SOI)、完全耗尽型 SOI(FDSOI)、硅锗双极互补金属氧化物半导体(SiGe BiCMOS))以及天线进行协同集成,从而以具有成本效益的方式(利用 2.5D 和 3D 集成技术)发挥其卓越的高频性能,同时受益于硅集成电路(IC)提供的更高集成度。本文从 InP 制造的角度,介绍了实现毫米波和亚太赫兹应用成功的 2.5D/3D 集成所面临的 InP D-HBT 技术发展的战略和实际挑战。
我们可以提供 6 inch 的 inp-on-si、inp-on-sic键合晶圆,成熟工艺,交付快
晶圆键合--室温下通过表面活化键合法直接键合GaAs-SiC/Si和InP-Si/SIC晶片
INP-SIC INP-SI
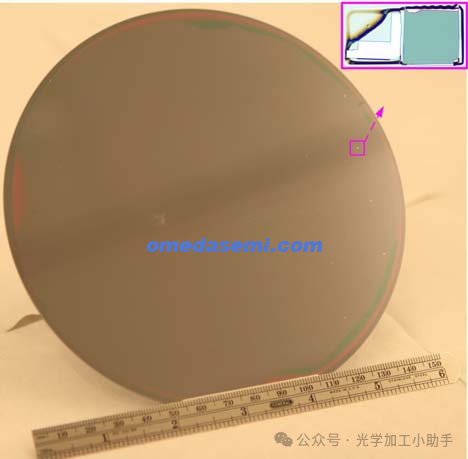
我们常见的键合技术 有硅玻璃键合 金金键合,金锡键合,金硅键合,临时键合等等 。但是当我们遇到一些需要低温键合,或者一些特殊材料时,或者应用场景时,上述键合方式很难满足一些特殊场景的应用,
因此科学家提出了表面活化键合技术,这种技术 使键合技术所覆盖的材料范围更加广泛,比如
GaAs-SiC,InP-Diamond, LN-SiC,Si-Si,GaN-Dlamond,Sl-Diamond,蓝宝石-蓝宝石,金刚石-sic, sic-inp,sic-LN, ic-ga2o3,glass--glass,Si-SiC,Si-GaAs、GaAs- SiC、Si–SiC、SiC–SiC、Ge–Ge 、Al 2 O 3 -Al 2 O 3 ,GaP-InP, GaN-Si、LiNbO 3 -Al 2 O 3 、LiTaO 3 -Si and more(晶体ybyag,ndyvo4,zns,陶瓷,等等)
扩展的多材料的体系,将键合技术扩大了应用范围
*MEMS传感器 *光子集成电路 *半导体激光器
*功率器件 *3D封装 *异质集成
划重点--代工,代工,代工,卖设备
我们为客户提供晶圆(硅晶圆,玻璃晶圆,SOI晶圆,GaAs,蓝宝石,碳化硅(导电,非绝缘),Ga2O3,金刚石,GaN(外延片/衬底)),镀膜方式(PVD,cvd,Ald,PLD)和材料(Au Cu Ag Pt Al Cr Ti Ni Sio2 Tio2 Ti3O5,Ta2O5,ZrO2,TiN,ALN,ZnO,HfO2。。更多材料),键合(石英石英键合,蓝宝石蓝宝石键合)光刻,高精度掩模版,外延,掺杂,电子束直写等产品及加工服务(请找小编领取我们晶圆标品库存列表,为您的科学实验加速。
请联系小编免费获取原文,也欢迎交流半导体行业,工艺,技术,市场发展
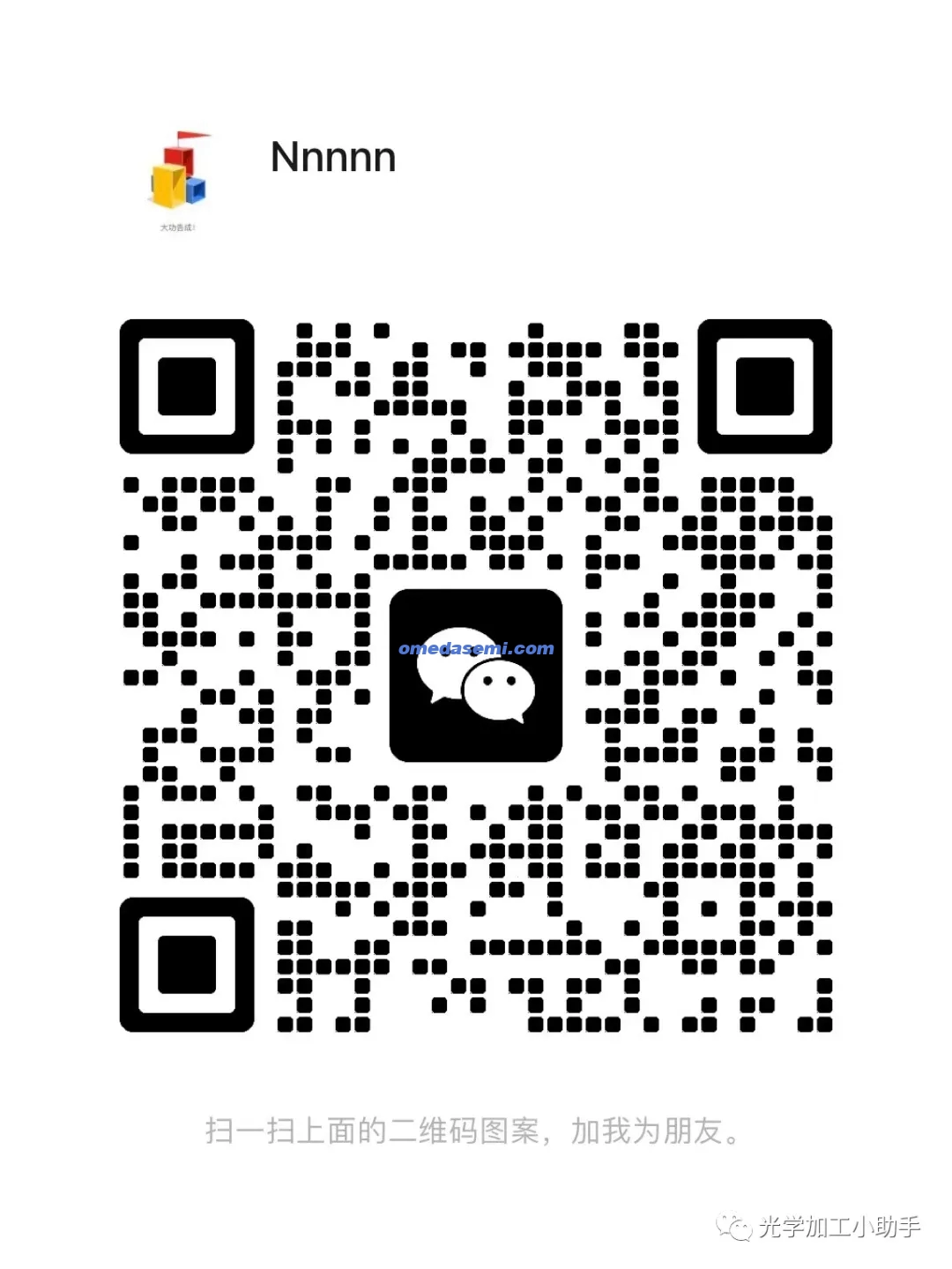
图1. 全球范围内创建、捕获、复制和消耗的数据/信息量。
为了传输数字世界中存储和处理的不断增加的数据量,从一个点到另一个点,模拟传输通道是不可避免的,并且如今(具有讽刺意味地)成为我们信息社会的真正瓶颈。
未来的6G通信、云计算和人工智能(AI),仅举几个应用,将消耗比光纤和无线通信系统预测的容量扩展所能提供的更多传输容量(见图1)。
为了应对这种巨大的带宽需求和更高的工作频率(以及随之而来的对超高速电子器件的需求),研究人员一直在密集开发高速硅技术。众所周知,自28纳米节点以来,由于栅极长度的缩小,硅CMOS(及其各种绝缘体上硅(SOI)和鳍式场效应晶体管(FinFET)变体)的最大振荡频率(fMAX)不再提高,因此并不是未来毫米波(mmWave)和亚太赫兹收发器前端的首选技术,尽管其具有更高的集成能力和较低的成本。
作为替代方案,SiGe BiCMOS技术在过去的二十年里表现出了显著的性能提升,使其成为当纯CMOS技术无法满足规格要求时(例如高频操作)的射频(RF)前端的首选技术。然而,对于以100−300 GHz频段为目标的下一代通信和传感应用来说,为了补偿大气衰减,必须使用天线阵列和波束控制,这使得SiGe BiCMOS技术的极限逐渐显现。
实际上,对于大功率放大器(PA)–天线阵列而言,功耗是一个关键指标,这使得当前SiGe BiCMOS工艺难以满足PA的功率附加效率(PAE)规格。因此,像砷化铟(InP)异质结双极晶体管(HBT)这样的更具潜力的技术目前被认为是可能的竞争者。值得注意的是,最近在这一领域的研究正在迅速发展,并且关于CMOS或SiGe BiCMOS与InP异构集成(或2.5D/3D封装)的文献大量涌现。
事实上,从纯材料性能的角度来看,InP在速度方面明显优于硅,但为了使其成为未来毫米波和亚太赫兹应用的可行选项,必须克服一些显著的挑战。本文从技术、实践和经济的角度阐述了这些挑战。
第二节将介绍当前的技术现状,并强调InP HBT在其他高速技术上的性能优势。第三节将详细说明InP高产量制造的挑战,而第四节将探讨与2.5D/3D集成相关的挑战。第五节将介绍关于InP HBT高级紧凑建模的要求,最后在第六节给出总结。
II. 技术现状与比较
图2. fT与fMAX的几何平均值与击穿电压的关系。
实心标记表示已知具备单片微波集成电路(MMIC)制造能力的技术,
空心标记表示仅能展示晶体管性能(无已知已发表的电路成果)的技术。
图2概述了适用于毫米波(mmWave)和亚太赫兹(sub-THz)应用的半导体技术的现状(图中未展示氮化镓(GaN)技术,因为其通常被认为更适合用于低于100 GHz和高功率的应用)。图2中,y轴表示fT和fMAX的几何平均值(作为一种平衡指标,这个指标衡量晶体管的高频性能),x轴表示击穿电压(或CMOS的供电电压)。
可以观察到,各种技术趋势大致遵循“伪”Johnson极限(这里使用“伪”一词,是因为标准的Johnson极限仅指fT):晶体管速度越高,其电压驱动能力越低。需要注意的是,图2中存在一些相对于双曲线趋势的中度偏离,这是因为较小的光刻技术通过减少外部寄生效应对fMAX产生了积极影响。然而,这并未显著改变从该图中得出的结论。
从y轴单独来看,可以首先注意到,引言中提到的CMOS限制清晰可见。同时,可以观察到,最先进的SiGe HBT技术(例如,fMAX > 600 GHz【3】)能够追赶大多数InP HBT技术。这一观察结果无疑是一些“硅独占支持者”认为InP在半导体生态系统中除极少数小众市场(如天文观测、高端表征设备等)之外并不需要的重要原因之一。
III. 实现大规模 InP HBT 制造的挑战
尽管 InP HBT 技术提供了无与伦比的性能优势,其市场应用却局限于少数几个领域,且生产量非常有限。这主要是由于与硅技术相比存在一些显著的制造限制:更高的工艺成本、更低的可制造性、材料的脆性和稀缺性、更小的晶圆尺寸,以及与主流硅封装解决方案不兼容的后端工艺。
A. 制造成本及其他考虑因素
InP HBT 工艺通常仅限于小直径晶圆:许多学术实验室仍然使用2英寸晶圆,而工业实验室和代工厂通常依赖3英寸、4英寸或(少见的)6英寸晶圆。这显然限制了向大规模制造的转变,并无法从硅技术中普遍存在的规模经济中获益。
图4. III-V Lab 的 InP HBT 技术的后端金属互连(上,比例未缩放)与 ST Microelectronics 的 BiCMOS55 技术【9】(下)的对比。
B. 实现大规模制造的替代策略
降低 InP 芯片成本的最简单方法之一是减少芯片面积(即在保证功能的前提下最小化成本)。然而,这一问题的解决并不显而易见,因为模拟和射频功能无法像数字功能那样随着技术最小特征尺寸的缩小而呈二次方规律缩放。
因此,研究正在进行以开发基于InPoSi(硅上的InP)晶圆的InP HBT工艺(例如,MOVE2THZ项目【8】)。InPoSi是一种制造工艺,其核心是在硅晶圆上绑定一片来自InP供体晶圆的薄InP层(见图3)。供体晶圆可以多次回收利用(这有助于缓解铟材料的稀缺性),由此制成的InPoSi晶圆机械性能更加坚固,从而提高了可制造性。此外,通过“晶圆拼接”技术,InPoSi还可以用于生产8英寸或12英寸的晶圆,从而解决了前面提到的晶圆尺寸问题,并降低了原始InP晶圆的成本。
尽管原材料方面取得了这一改进,初始外延步骤仍是一个主要的成本来源,无法通过晶圆尺寸的扩大完全缓解。因此,为了克服这一问题,需要采用其他路径来降低成本。
典型的 InP HBT 技术通常具有 2-4 层相对较薄的金属层。更先进的后端金属互连(BEOL,即更多的金属层、更厚的金属以及金属间介电层)可以显著减少毫米波频段的介质损耗,或者缩小片上匹配网络和功率合成阶段的面积(图4展示了典型 SiGe BiCMOS【9】和典型 InP HBT BEOL【10】的比较示例)。
尽管硅技术的大多数(密集布线的)底层金属层在优化的 InP HBT 工艺中可能用处不大,但顶部较厚的金属层可以被用来优势地进行毫米波互连。同时,也需要开展提高布线密度的开发工作,因为大多数 InP HBT 制造商有时采用(不必要的)保守设计规则(例如,InP HBT 工艺中广泛使用的光刻剥离技术部分解释了这些严格的设计规则,但部分布局限制仅源于计算机辅助设计(CAD)验证工具中更简单设计规则的实现)。
另一个限制芯片尺寸缩小的问题是集成电容和电阻占用了芯片上大量空间。相比硅技术中可用的多种集成射频电阻(从几 Ω/□ 到数千 Ω/□)和双密度集成 MiM 电容(通常从 2 到 4 fF/µm²),典型 InP HBT 技术中的单一 NiCr 电阻层(约 50 Ω/□)和 Si₃N₄ MiM 电容(通常低于 0.5 fF/µm²)是另一个限制因素。
最后,通常用于提高集成电路高频稳定性和消除寄生基底模式的基底贯通孔(TSVs),如果某一工艺中有应用,会占用大量空间。寻找替代方案(如使用薄膜微带线(TFMSLs))将有助于整体芯片尺寸的进一步缩小。
图5. PA MMIC 芯片设计,尺寸为 1.2 × 1.5 mm²(III-V Lab)(左);带射频焊盘的多指晶体管结构,尺寸为 260 × 160 µm²(右)。
最终,可以通过将 InP 芯片尺寸减少到晶体管区域及其连接焊盘的大小,进一步推进 InP 芯片面积的缩减【11】。这是一种通过共集成实现的可能选择之一:将芯片尺寸减少到其最低需求,即仅包含单个晶体管的最小面积。
一种可行方案是用单个多指晶体管替代 MMIC(例如,功率放大器 (PA) 或低噪声放大器 (LNA),包括其连接、匹配和稳定输入输出网络、去耦电容、偏置传输线和电阻)。以图5左侧所示的 PA 设计为例,其尺寸为 1.2 × 1.5 mm²,而图5右侧显示的典型 InP HBT 结构尺寸为 260 × 160 µm²,面积缩减比例可高达 40 倍(从而在物料清单中大幅降低 InP 芯片的成本)。
这种方案带来了其他需要解决的挑战:所有被移除的功能需要在 CMOS 或 SiGe BiCMOS 中高效实现,并通过低损耗互连进行连接。此外,为了高效地协同设计硅芯片与 InP HBT 晶体管,必须在 InP HBT 的紧凑建模以及整个系统在复杂多材料环境下的电气–电磁协同仿真方面投入大量精力。
第四章:与 2.5D/3D 集成相关的挑战
A. 异构集成的通用需求
描述所有可能的 InP HBT 技术与硅芯片进行 2.5D/3D 异构集成的方案超出了本文的讨论范围;然而,回顾 InP 技术在后端工艺 (BEOL) 方面的要求仍然具有重要意义。图 6 展示了一些 SiGe/CMOS 与 InP 共集成的可能性。
图6. 2.5D/3D集成方案示例(SiGe为蓝色,InP为棕色)。
尽管 SiGe 芯片的倒装芯片技术被广泛使用,但 InP 芯片的倒装芯片技术并不简单,尤其是针对功率放大器 (PA),因为需要解决热管理的限制。挑战包括金属后端 (gold BEOL) 和缺乏顶部钝化层(导致 InP BEOL 与铜柱技术不兼容)、散热问题以及高频 (HF) 去调谐效应。
关于热管理方面,目前对于 InPoSi 晶圆的使用仍然存在不确定性,直到第一批 HBT 在 InPoSi 上实现后才可能明确(尽管硅的热导率优于 InP,但 InP 和硅之间的热屏障可能抵消散热性能的提升)。此外,后端工艺需要完成大量工作,以 (i) 使其与主流倒装芯片技术(封装/钝化)兼容,(ii) 提高芯片对去调谐效应的抗扰性。
为此,InP 芯片的 BEOL 应具备优化的后端结构(更多的金属层和更厚的金属),以支持低损耗的薄膜微带线 (TFMSLs),并潜在地配备顶部和底部接地平面,从而将电磁 (EM) 场限制在后端工艺内。
在此方面的最终目标是使 InP 芯片接近“芯粒 (chiplet)”的概念。
嵌入式(见图6)是SHIFT项目[12]中为InP/BiCMOS共同集成演示选择的解决方案。文献[13]中的这一方案提供了一个有趣的设计选项,能够共同集成SiGe BiCMOS芯片、InP功率放大器(PA)和天线,从而演示波束控制功能。该原理的演示目前正在作为SHIFT项目活动的一部分进行。InP技术面临的挑战包括BEOL与激光通孔(金属厚度)、BEOL处理、以及所考虑的InP HBT技术(用于散热)缺乏背面金属化和TSV。
B. 毫米波应用的具体技术要求与硅异质集成
许多InP HBT工艺包括TSV和背面金属化,但III-V实验室的InP D-HBT技术目前并不具备这一特性。III-V实验室的技术[14]是原生优化用于高速模拟-数字电光接口(用于光纤应用):晶体管的优良性能指标被调节以实现快速电流切换、高电压驱动、宽带操作和低工艺步骤数。由于该技术的主要应用具有快速切换的特点,因此TSV和背面金属化并不被视为必要的,考虑到它们会增加工艺复杂性和制造时间。如第III.C节所示,TSV也在芯片空间要求方面存在疑问。TSV和背面金属化主要用于两个方面:(i)微带线设计和(ii)寄生模式抑制。关于(i),随着应用频率的增加,微带线的可行性变得越来越困难,因为基板需要变薄到,例如,低于100微米甚至50微米,以保持在有效线阻抗范围内,这会使芯片变得非常脆弱,并降低工艺的可制造性。在这方面,切换到替代方案,如TFMSL,显然是可取的。
关于(ii),我们考虑一个基于共面波传输线的测试结构中的寄生模式激发示例(见图7中149 GHz的电磁仿真结果,对应于约8 dB的传输衰减)。这些寄生模式的激发对功率放大器(PA)和低噪声放大器(LNA)在例如D波段和G波段中的性能非常不利,因为它们在集成电路响应中产生了衰减和共振(在某种程度上,这对于快速切换的数字电路来说不那么有害)。图8展示了AMUX驱动IC的S参数测量示例[15],该IC分别安装在镀金陶瓷载体和硅载体上。事实上,寄生模式的激发在硅载体上显著减少,表明具有损耗的硅起到了吸收器的作用。因此,未来基于InP HBT技术的InPoSi基板可能对寄生模式激发的敏感性较低,这将消除对TSV的需求。
V. 紧凑建模挑战
InP HBT技术的紧凑(类似SPICE)建模在硅以外的技术中显然存在不足。历史上,由于缺乏适合的III-V HBT紧凑模型,III-V社区大多依赖于手工制作和/或手动定制的模型,这些模型使用行为源或符号定义语言。这些模型,尽管有时对于特定应用和/或偏置与温度操作范围来说相当复杂且准确[9],但通常无法满足各种设计需求,正如BiCMOS模型和工艺设计工具包(PDK)所做的那样。这些模型是基于物理的、可扩展的,
图7. 共面波传输线中的差分直通电路的电磁仿真(对应于电路接入)。在149 GHz时可见激发的寄生模式。
图8. InP D-HBT AMUX驱动IC的测量S参数。S11(左)和S21(右)与频率的关系,IC安装在金属化陶瓷载体上(红色)和安装在硅载体上(蓝色)。
图9. 220 GHz SiGe BiCMOS集成LNA的S21参数测量/仿真对比。使用HiCuM/L2模型的仿真结果(实线)与不考虑NQS效应的仿真结果(虚线)之间的差异。
统计模型和预测模型[14][16][17]在毫米波和亚太赫兹应用中尤为重要,能够为设计师提供更大的搜索空间和灵活性,尤其是在每一分贝增益都至关重要的情况下。此外,像HiCuM/L2[18][19]这样的标准化模型几乎在所有的CAD专有或开源软件中都可以使用,因为其Verilog-A代码可供用户使用。对于诸如HiCuM等基于物理的紧凑模型的需求,典型的例子是非准静态(NQS)效应在例如140-300 GHz频率范围内对高频线性增益预测的影响[20],这一影响常被低估。如图9所示,忽略NQS效应(当应用频率接近约fT/3时,这些效应变得显著)可能导致在放大阶段预测线性增益时出现严重的差异。
VI. 结论
如今,InP HBT技术仍然局限于小众市场,从而限制了对大规模制造的投资,进而限制了该技术在中大型市场中的应用。通过对InP生态系统的战略性投资,可以打破这一循环,而这一投资仅占硅工艺开发所需资金的一部分。虽然InP HBT将继续作为一种低集成度的技术,但它无疑可以通过异质集成,作为一种补充工具集,受益于要求高的毫米波应用以及超过Tb/s的光通信。InP HBT不会也不可能取代SiGe BiCMOS,但可以充分补充它们已经强大的能力,前提是能够实现适当且雄心勃勃(但并非遥不可及)的开发。