本文小编分享一篇文章,关于双光子3d打印在成像光学中的应用,作者团队付出了巨大的努力,这是一篇十分长的文章,
作者全面探讨了双光子聚合物光刻(TPL)及其在成像中的应用,深入剖析了其能力和潜力。
介绍了与TPL相关的基本成像理论、关键材料属性和先进制造技术,为理解其原理和应用提供了坚实基础。
同时也系统分类和总结了TPL的各种成像应用,展示了其在不同领域(如显微镜、纳米光子学和生物医学成像)的多功能性和潜力。
另外也展望了未来的趋势与解决方案:展望了TPL在成像光学领域的未来趋势,并提供了针对当前挑战的潜在解决方案的见解。通过利用高分辨率能力和材料进步,TPL有望彻底改变光学成像技术,为现有限制提供颠覆性解决方案。
本文是对双光子技术在成像光学上应用的一次很好的汇总 ,值得大家一看
下面展示一些,作者汇总的前人打印的一些案例。
平面基底上1-3层折射透镜
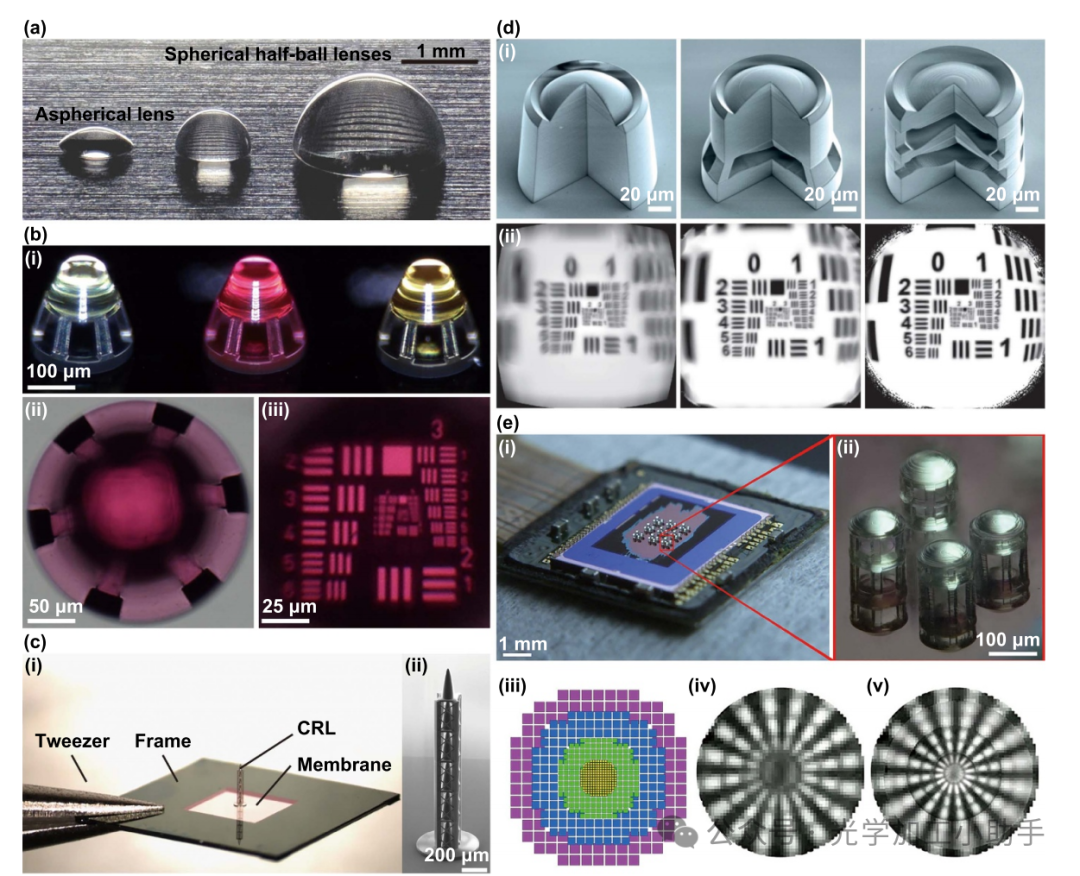
平面基底上1-3层菲涅尔和衍射光学透镜
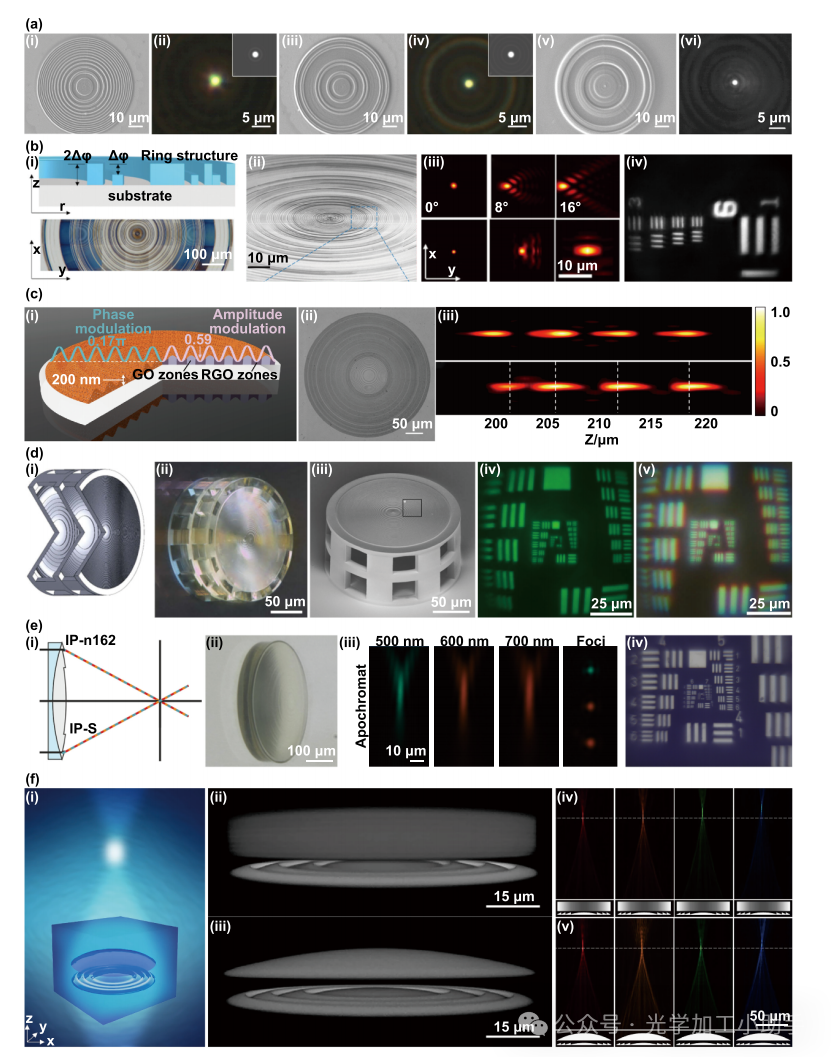
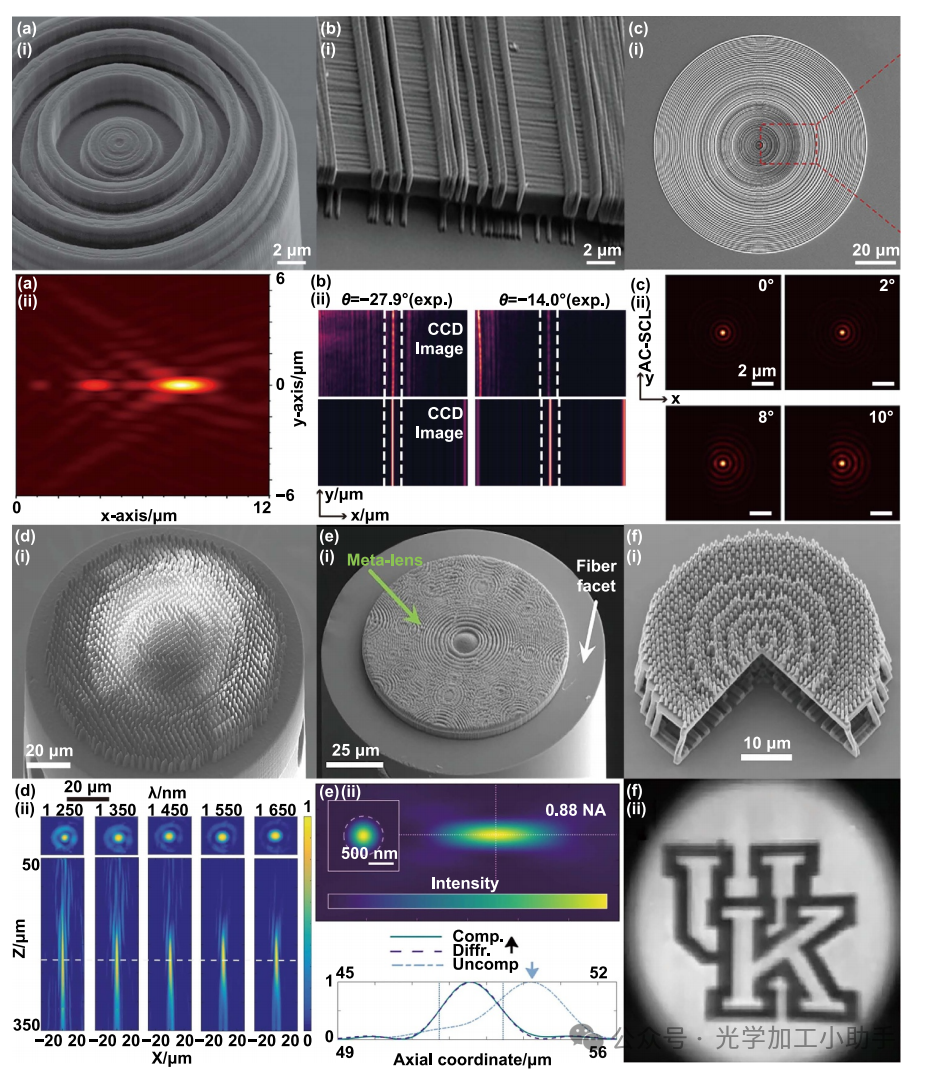
平面基地上微透镜阵列
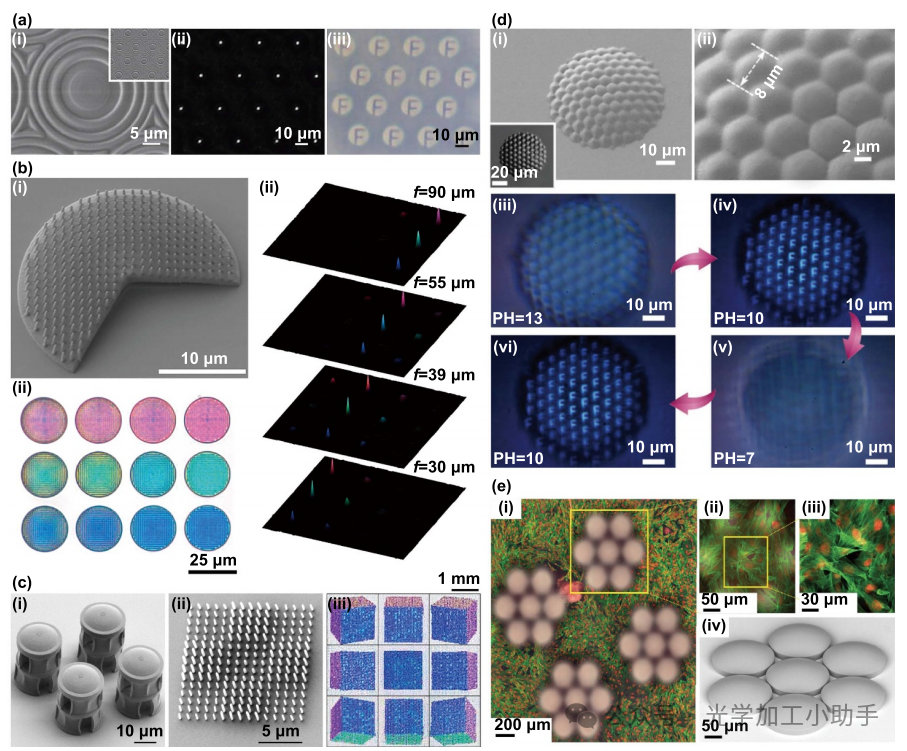
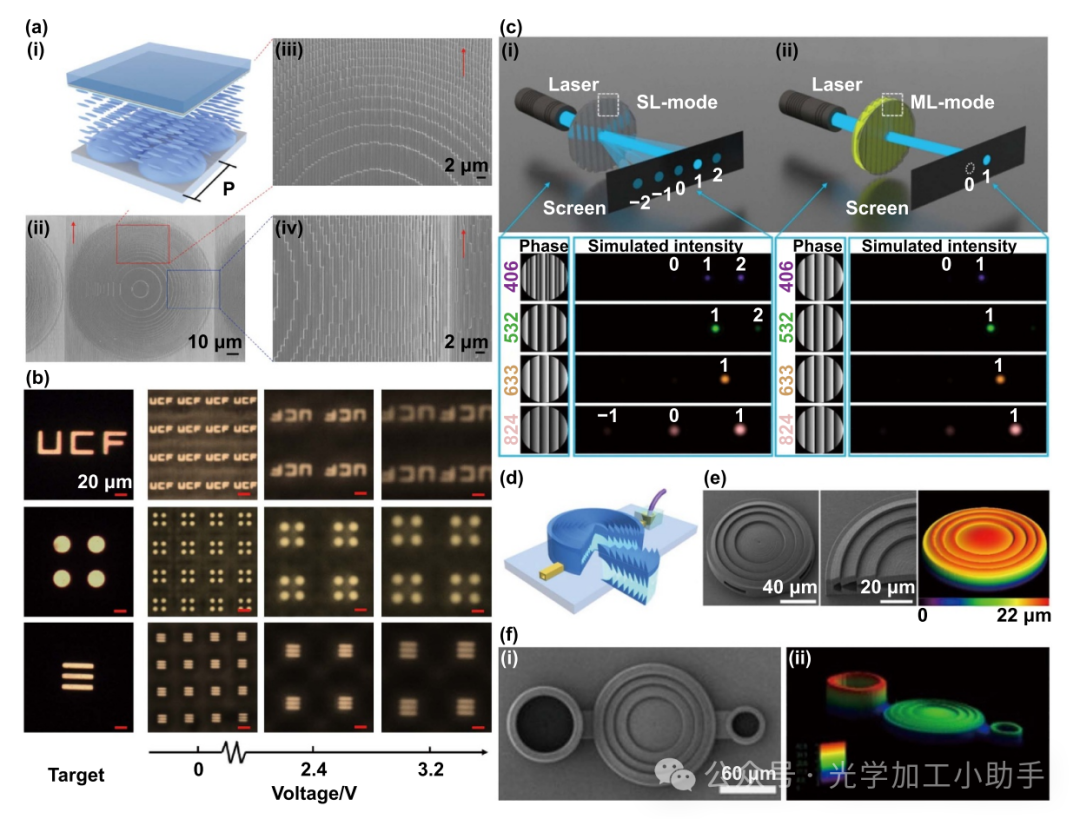
光纤端面超透镜和折射透镜结构
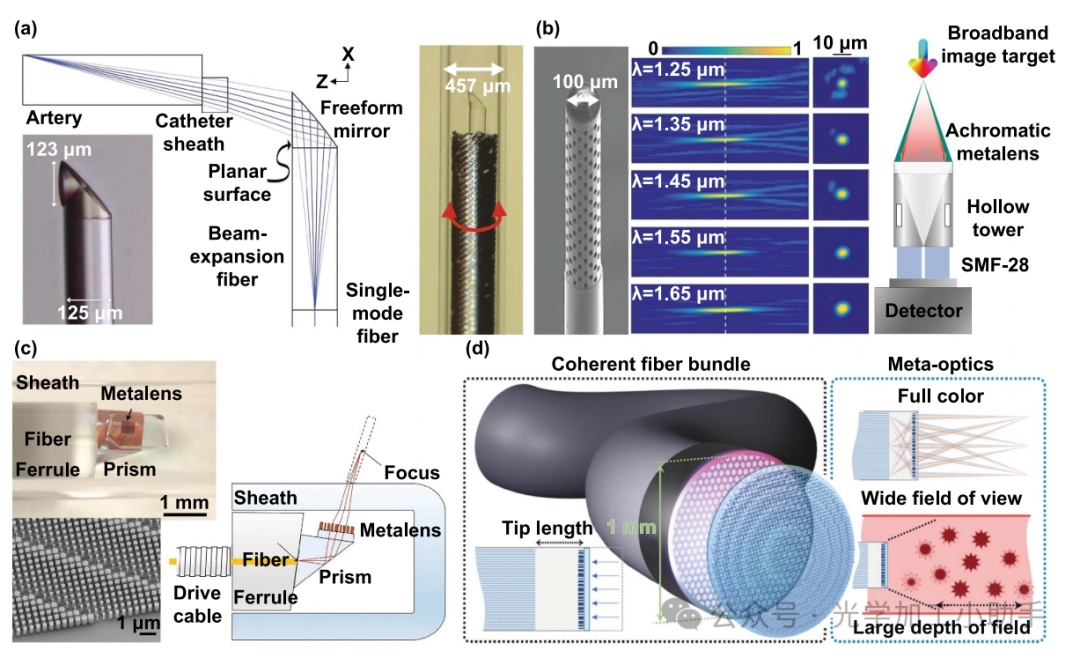
划重点(双光子3D打印设备和代工)
在光纤端面亦或其他基底材料上通过双光子3D打印的方式一直是科研工作者研究的关注点,但是由于高精度双光子3D打印的设备极其昂贵,技术也较为前沿,许多科研工作者乏于寻找可靠的,高效率的加工提供商。。
因此如果您有需求,可以联系小编为您推荐成熟的双光子3D打印企业,加速您的创新。
国产优秀产品免费推广(双光子打印用---紫外钝感双光子打印胶水)
优点1:紫外钝感,就是紫外不敏感,无需避光低温保存
优点2:双光子聚合活性更高,15mw激光功率下打印速度就可以达到100mm/s
优点3:纯国产,兼容国外多款机台,同时在胶水定制开发效率等上面具有极大的优势
如果你也爱好 半导体,光学,光纤,硅光集成等技术及应用,可以添加小编,一起畅聊技术,市场和应用。
看原文请联系小编免费领取
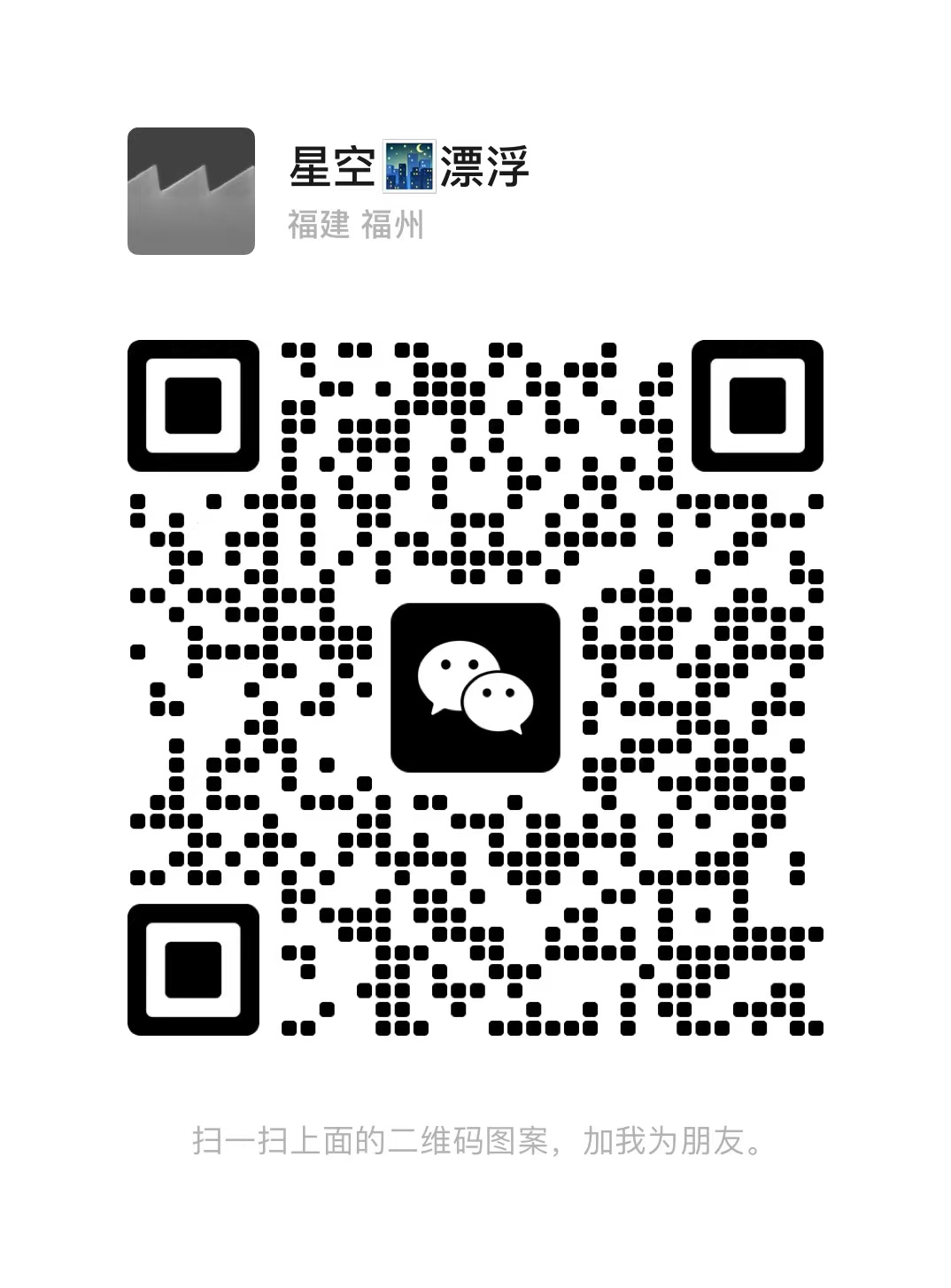
用于成像光学的双光子聚合光刻
光学成像系统大大扩展了人类的视觉能力,使观察和理解各种现象成为可能。成像技术涵盖了从X射线到无线电频率的广泛波长范围,并影响到研究活动和我们的日常生活。传统的玻璃透镜通过一系列复杂的工艺制造,而聚合物提供了多样性和易于生产的优势。然而,现代应用通常需要复杂的透镜组件,推动了微型化和具有微观和纳米尺度特征的先进设计的需求,以超越传统制造方法的能力。三维(3D)打印,或称为增材制造,为这些挑战提供了解决方案,具有快速原型制作、定制几何形状和高效生产的优点,特别适用于微型光学成像设备。各种3D打印方法已经显示出优于传统对应物的优势,但在实现纳米尺度分辨率方面仍存在挑战。两光子聚合物光刻(TPL),一种纳米尺度的3D打印技术,通过液态树脂内的两光子吸收的非线性过程,实现了超越光学衍射极限的复杂结构的制造。它提供了前所未有的能力,例如无需对准的制造、微观和纳米尺度的能力,以及几乎任意复杂3D纳米结构的快速原型制作。在这篇综述中,我们强调了成像设备光学性能评估标准的重要性,讨论了与TPL相关的材料属性、制造技术,并突出了TPL在光学成像中的应用。作为这一主题的首次全景回顾,它将为研究人员提供TPL用于成像光学的基础知识和最新进展,促进对该领域的更深入理解。通过利用其高分辨率能力、广泛的材料范围和真正的三维处理,以及材料、制造和设计的进步,我们预见到对当前挑战的颠覆性解决方案,并有望将TPL成功地融入未来的光学成像应用中。
要点:
全面概述:本综述全面探讨了双光子聚合物光刻(TPL)及其在成像中的应用,深入剖析了其能力和潜力。
基本理解:介绍了与TPL相关的基本成像理论、关键材料属性和先进制造技术,为理解其原理和应用提供了坚实基础。
应用分类:系统分类和总结了TPL的各种成像应用,展示了其在不同领域(如显微镜、纳米光子学和生物医学成像)的多功能性和潜力。
未来趋势与解决方案:展望了TPL在成像光学领域的未来趋势,并提供了针对当前挑战的潜在解决方案的见解。通过利用高分辨率能力和材料进步,TPL有望彻底改变光学成像技术,为现有限制提供颠覆性解决方案。
1. 引言
光学成像是通过光学设备创建物体的准确表示的过程,类似于人类如何用眼睛感知周围环境和物体的方式。这个传统但不断发展的领域已经被研究了几千年,随着理论、材料、设计、技术和各种应用的发展而进步。光学成像系统超越了人眼的视觉能力,通过大口径望远镜探索宇宙,以及显微镜探索微观世界,促进了生物学、化学、医学和其他相关学科的进步,扩大了人类的观察和理解范围。此外,光学成像已经超越可见光谱,包括X射线、紫外线(UV)、红外线、太赫兹、微波和无线电频率。光学成像技术在空间和时间分辨率、光谱敏感度、检测能力和多维成像方面的持续改进,促使它们广泛集成到消费电子产品中,如智能手机、无人机和虚拟现实眼镜,极大地提升了日常生活的质量。
传统的玻璃透镜制造方法涉及多个复杂步骤,如玻璃坯料成型、铸造、退火、金刚石车削和成型,以及粗磨和精磨。此外,要实现复合物的均匀性和精确的相位调制,需要复杂的测量和熔融血统计算。相比之下,作为典型的柔性材料,由于其低成本、轻质、制造灵活性和高透明度,聚合物在过去几十年中已经变得越来越受欢迎,采用了注塑成型和紫外光固化等更简单的技术。它们还可以作为稳定的基体用于各种光学应用的分子、纳米粒子和纳米晶体。一般来说,在大多数应用中,表面粗糙度低于波长的十分之一的透镜就足够了。然而,在当代成像应用中,仅靠一个透镜往往无法满足各种场景下的多样化要求,在这些情况下,需要透镜组来改善成像质量,这是望远镜、显微镜和手机等设备中常用的策略。这必然导致了耗时的组装以及多个透镜与马达、滤光片、图像传感器和其他光学模块的复杂对准。此外,现代光学成像设备更青睐于迷你化、便携化和一体化,这超出了传统的大块透镜的范畴。在这种精神下,透镜设计原理的最新进展从折射光学延伸到衍射光学和纳米光子学,旨在利用薄、轻的光学设备来实现前所未有的成像能力,以补充传统的透镜。对于后者来说,要获得微观和纳米级别的结构尤其困难,从而限制了它们的潜在应用。
三维(3D)打印,也称为增材制造(AM),为传统制造方法所面临的上述挑战提供了一个有前景的解决方案。它消除了制造各种数量透镜的对准要求,并使得能够生产具有小尺度特征的光学器件成为可能。此外,3D打印具有许多优势,包括快速原型制作、定制几何形状、产生的废料量少以及制造时间短等。3D打印所使用的聚合物的固有特性,如高透明度、均匀性和低表面粗糙度,使它们成为微型光学成像设备的理想候选材料,特别是对于可见光波段的应用,因为不存在吸收带。各种3D打印方法,包括基于挤出的熔丝成型、直接喷墨写入、熔融沉积建模,以及光学基础的技术,如数字光处理、激光光固化、连续液体界面制造、聚合物喷射、计算轴向光刻[9]和xolography[10],已经被应用于制造具有优异质量的微米至厘米尺度的光学物体。一般来说,在成像设备制造中考虑AM技术的关键参数包括商用打印机、建造体积、特征尺寸、打印速度、光学材料能力、后处理处理、均匀的光学性质、保留原始材料特性、均匀的表面界面等[11]。尽管这些3D打印方法相比传统制造技术具有优势,但它们在实现纳米尺度的空间分辨率和为复杂的3D设备提供低表面粗糙度方面仍存在局限,因此只限于宏观组件[12]。
在最具前景的纳米尺度3D打印技术中,双光子聚合物光刻(TPL)赋予了制造超越光学衍射极限的任意结构的能力。TPL的原理涉及通过高数值孔径(NA)物镜将飞秒脉冲激光聚焦到未固化的液态光刻胶中,形成一个焦点。只有在诱导了双光子吸收的情况下,光刻胶才会聚合,其概率与光强的平方成正比。这种非线性过程比单光子吸收弱了几个数量级,将光聚合限制在焦点的中心体积内,其中光强超过阈值,形成一个体元。随后,可以通过将设计的3D结构分割成层,并将每一层划分为孵化线来打印。激光束然后沿着这些路径在光刻胶中扫描,以优化的打印速度和激光功率塑造具有体元的模型。
TPL具有多重优势,包括无需对准的单步制造、实现微观和纳米尺度特征的能力,以及快速生产高质量结构[20]。其广泛的应用范围涵盖了光学和纳米光子学领域[21–24],包括折射光学、衍射光学元件、光子电路、拓扑光子晶体、量子光学和光学机器人。值得注意的是,TPL作为一种强大的工具,可用于制造微型光学成像系统,如前文所述。在这篇综述中,我们首先重新审视了评估成像性能的关键参数,主张对3D打印成像设备进行全面的光学表征。随后,我们介绍了TPL的关键材料特性,如转化度、透射率、色散、热稳定性和机械稳定性,这些特性对成像质量产生了重大影响。我们还详细总结了通过TPL在各种基底上制造成像系统所采用的技术,包括玻璃、光纤、芯片和图像传感器(互补金属-氧化物-半导体,CMOS,和电荷耦合器件,CCD)。在此之后,我们报道了TPL在光学成像应用方面的发展,涵盖了各种类别,如折射透镜、衍射透镜、金属透镜、梯度折射率透镜、透镜阵列、复眼、动态透镜、内窥镜透镜、衍射光学神经网络、计算成像和其他光学成像系统(图1)。预计这将为研究人员提供一个全面的综述,使他们能够掌握基础知识和最新进展,促进对该领域的全面理解。最后,利用TPL的高分辨率加工能力、广泛的材料加工范围和真正的三维加工能力,结合新材料[25–28]、制造技术[29]和设计方法[30]的最新进展,我们讨论了解决当前挑战的潜在解决方案,并展望了TPL在成像光学领域的前景。尽管TPL相比传统制造方法具有诸多优势,但其在工业生产中的应用仍处于起步阶段,并面临着各种限制,如合适的材料和直接制造速度。这种缓慢性导致了成本的提高,构成了该技术的主要限制因素。尽管存在这一限制,TPL适用于快速原型制作和为具有特殊形状的成像元素制造模具,从而促进了具有专业功能的设备的生产。我们预见,通过融合统治光学成像、材料、创新设计和新型制造技术的基本原理,TPL将继续革新这一领域,深化我们通过成像对世界的理解。
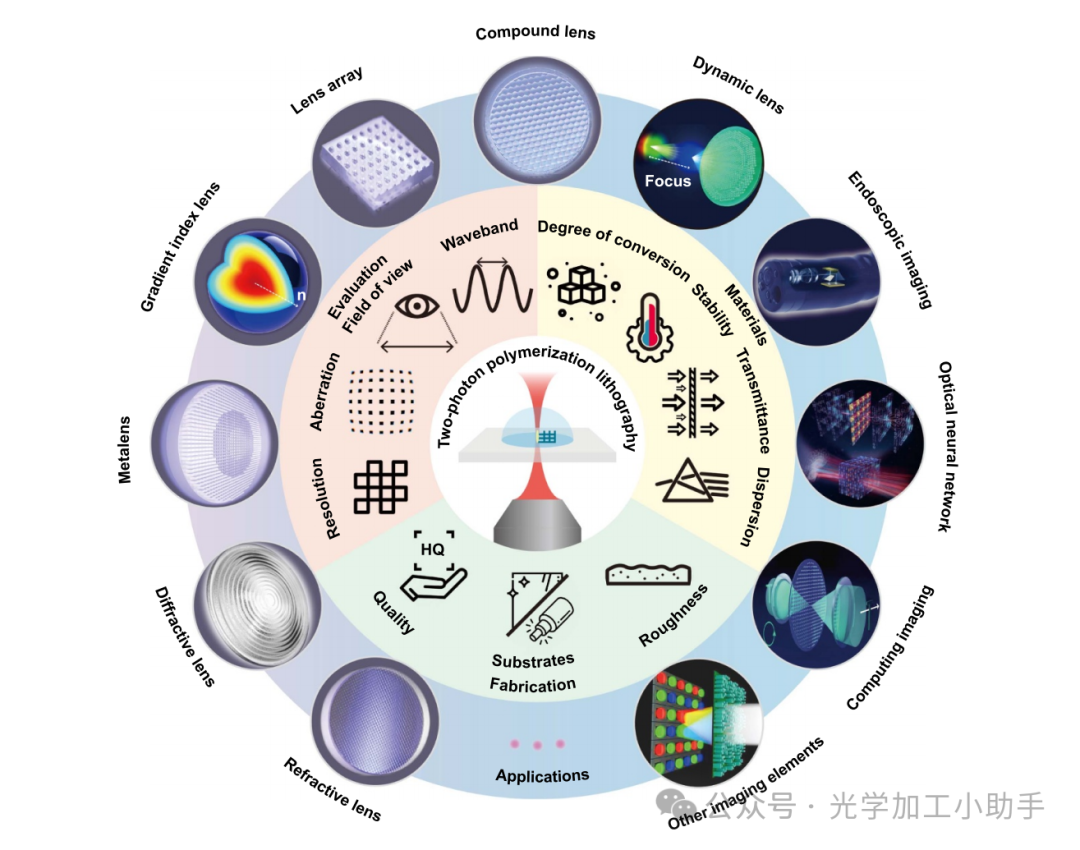
图1. 用于成像光学的双光子聚合物光刻的示意图,包括评价标准的类别、材料、制造技术和各种应用。摘自[32]。CC BY 4.0。摘自[31]。CC BY 4.0。
2. 成像评估
光学成像系统的评价标准对于量化系统的质量并将其性能与其他系统进行比较至关重要。虽然通过TPL制造了各种类别的成像元件和设备,但文献中仍缺乏系统介绍评价方法,并未提及一些关键参数。总的来说,针对传统成像系统建立的评价标准仍然可以应用于微型和纳米尺度的成像系统。如图2所示,我们旨在通过概述成像系统的重要设计参数来解决评价标准,然后介绍基本定义并总结像差理论。在成像系统的设计过程中,减小像差是优化目标,也是图像质量评价指标。最后,我们介绍了基本的成像质量评价方法,这些方法可以反映出成像系统的设计参数和像差,因此可以用来优化设计和制造参数。
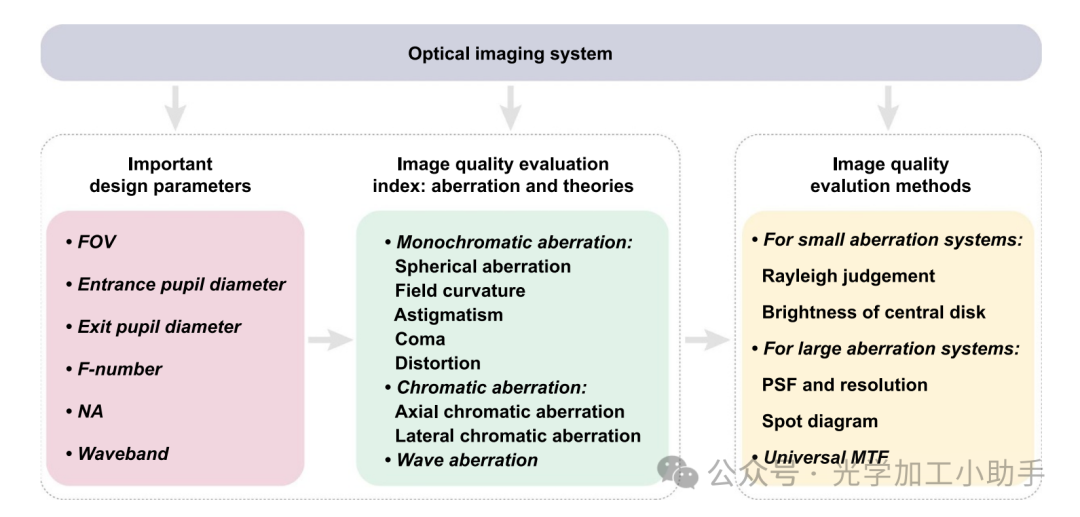
图2. 光学系统的设计参数和成像质量评价方法。
2.1. 重要设计参数
基本设计参数的建立在光学系统的设计过程中至关重要,因为它们是根据特定的要求和应用场景量身定制的。在这一部分中,总结了光学系统重要参数的定义和影响,如表1所示。
表1. 重要设计参数总结
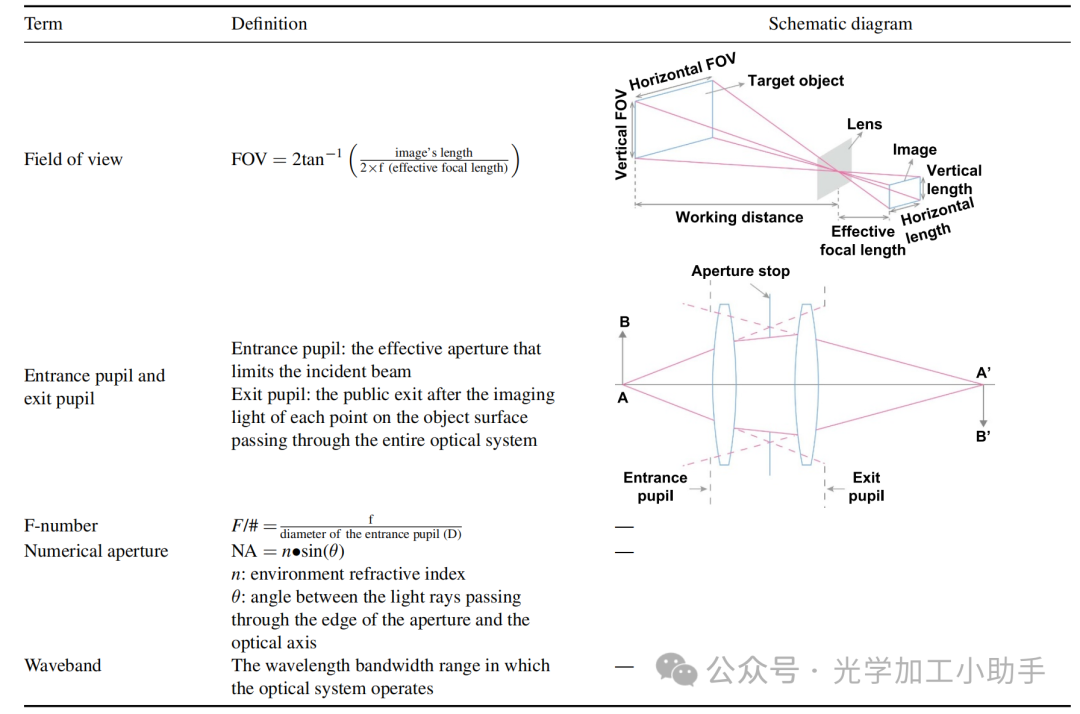
2.2. 成像质量评价指标:像差理论
任何图像的质量都会由于几何像差和衍射的存在而降低。因此,当一个物体点通过光学系统时,在图像平面上呈现的不再是理想点,而是一个混淆圈。因此,分析和优化像差以最小化其影响对系统设计至关重要。像差可以分为两个主要类别:几何像差和波像差。其中,几何像差可以进一步分为单色像差和色散像差,单色像差的具体分类如表2所示,其中与透镜几何参数的关系如表3所示,色散像差的具体分类如表4所示。
表2. 单色像差的定义及相应现象
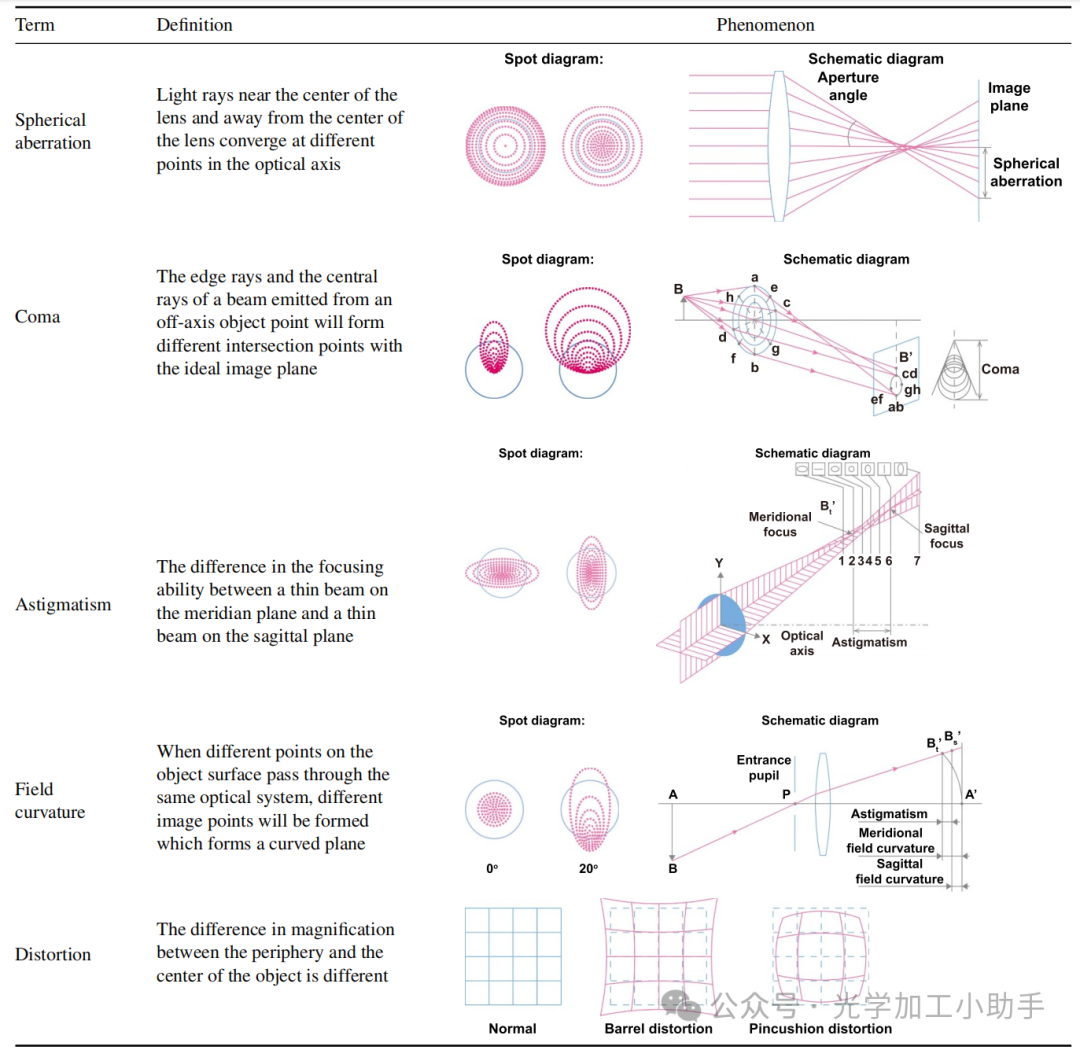
表3. 第三阶单色像差与孔径和视场的依赖关系总结
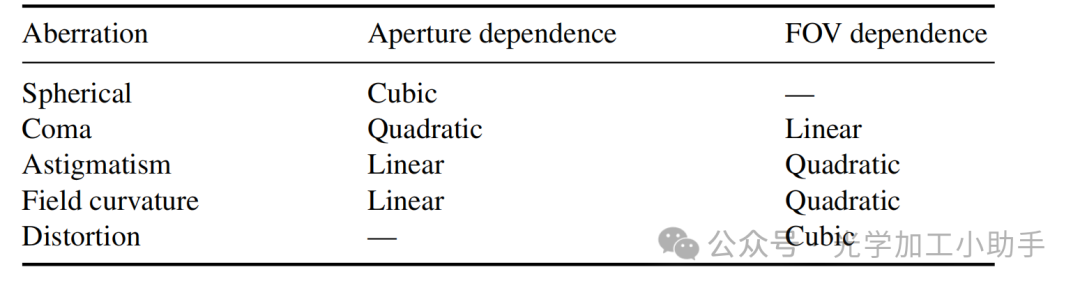
表4. 色散像差的定义及相应现象

2.2.1. 单色像差。
关于上述几何像差,Fischer等人总结如表3所示,反映了视场(FOV)和入瞳直径对上述像差的影响程度[33]。
2.2.2. 色散像差。
参见表4中色散像差的定义及相应现象。
2.2.3. 波像差。
当球面波通过光学系统时,理想情况下将形成一个新的球面波,实际上,该波往往会在某种程度上变形,不是理想的球面波,如图3所示。
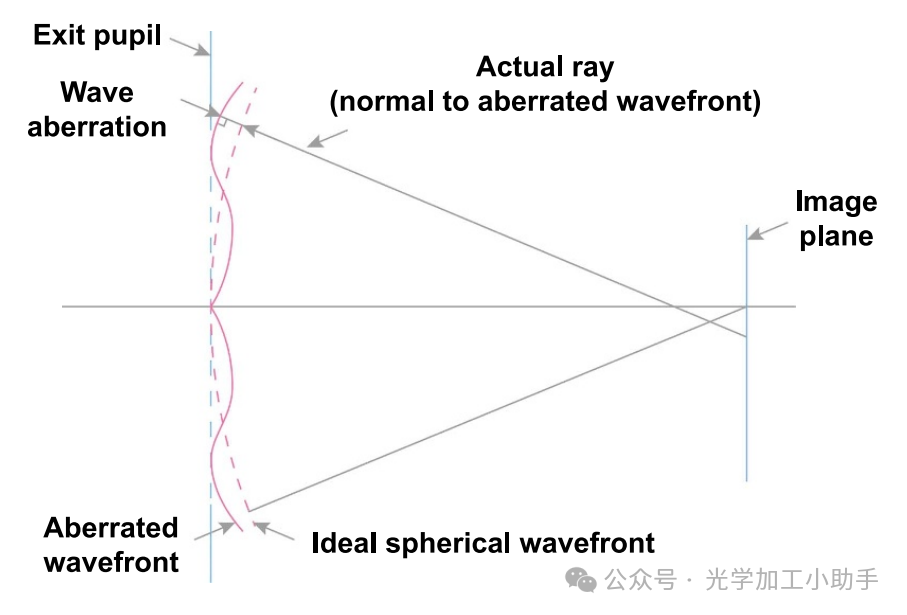
Figure 3. 波像差示意图。
2.3. 成像质量评价方法
在图像质量评价过程中,如果不考虑衍射效应,图像质量主要受到系统像差的影响,在这种情况下,可以基于上述像差理论进行图像质量评估。当衍射和几何光学像差同时存在时,一些更系统的评价方法已经被引入,而评价方法的选择取决于设计的光学系统的像差特性。对于小像差系统,通常使用瑞利准则和中心光斑亮度方法。至于大像差系统,一般通过点扩展函数(PSF)、分辨率、斑图和星测试方法来评估图像质量。调制传递函数(MTF)是一种通用的评价方法,适用于大像差系统和小像差系统。由于TPL适用于制造基于光线追迹的透镜、衍射透镜,甚至是金属透镜,因此这里介绍的评价方法可以用于更有效和可靠地比较它们的性能。
2.3.1. 对于小像差系统
2.3.1.1. 瑞利准则。
瑞利准则是由瑞利勋爵在观察光谱仪成像质量时提出的一个标准,该标准规定,如果由像差引起的最大光学路径差不超过波长的四分之一,则光学系统的性能基本上不受影响。
2.3.1.2. 中心光斑亮度。
Strehl提出了一个比率,即在有像差的衍射图案中最大亮度与没有像差时最大亮度的比值,来代表光学系统的图像质量。这个比值称为中心点亮度,用S.D表示。Strehl指出,当中心点亮度S.D大于或等于0.8时,系统被认为是可用的。
2.3.2. 对于大像差系统
2.3.2.1. PSF和分辨率。
对于一个光学系统,通过系统的点的物体平面上通过系统的点所对应的图像平面上的光场分布称为PSF。PSF的概念也可用于确定光学系统的分辨率。
光学系统的分辨率指的是光学系统能够解析的两个紧密间隔的物体点之间的最小距离。该指标反映了光学系统解析物体的细微结构的能力。瑞利指出,“当一个像的衍射图案的中心恰好在另一个像的衍射图案的第一个极小值上方时,这两个像才能刚好分辨出来”,如图4(a)所示。图中两个峰点之间的距离是:
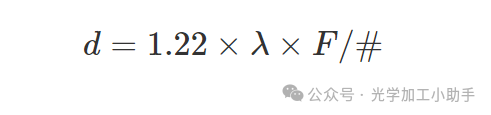
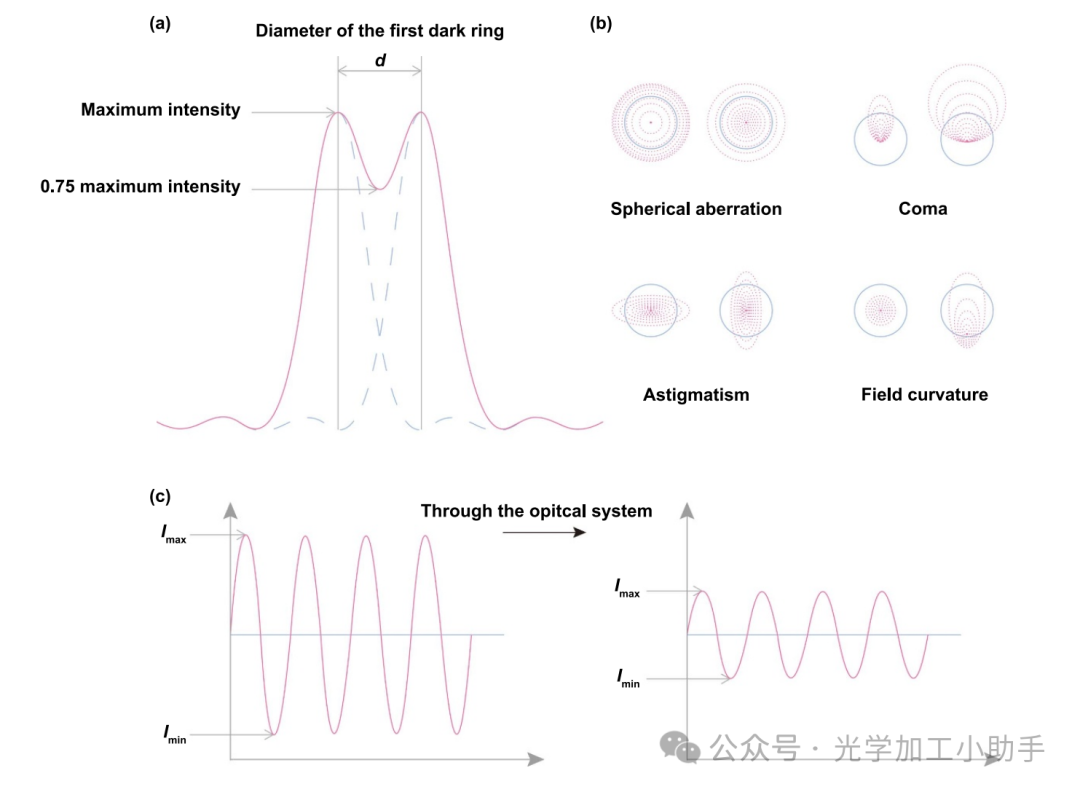
Figure 4. 评价方法示意图。(a) 分辨率。(b) 斑图。(c) 调制传递函数(MTF)。
这个公式是计算光学系统理论分辨率的基本公式。这个公式也是计算艾里盘半径(衍射极限)的公式。由于任何光学系统都受到几何像差的影响,实际的斑点半径很难超过衍射极限。
2.3.2.2. 斑图和星测试。
当一个点的许多光线通过光学系统后,由于像差的存在,它们与图像平面的交点不再是一个点,而是形成一个模糊的图案,称为斑图。可以根据点的密度和分布图案的形状来衡量系统的成像质量。由于斑图忽略了衍射效应,它只反映了系统的像差程度。这里列举了不同像差下斑图的分布,如图4(b)所示。
星测试方法的原理与斑图类似。由于任何物体的分布都可以视为无数个具有不同强度的独立光点的集合,任何物体的图像都是无数个星点图像的集合,因此可以通过星图像的光强分布函数来判断系统的成像质量。与斑图不同,斑图是设计过程中采用的评价方法,而星测试是在光学系统制造后采用的。
2.3.2.3. 通用方法
2.3.2.3.1. 调制传递函数(MTF)。
上述图像质量评价方法在应用中都存在一定的局限性,而MTF涉及到光学系统的几何像差和衍射效应,因此是最通用和综合的评价方法。MTF可以表示为图像平面对物体平面的对比度比值,而对比度由(Imax−Imin)/(Imax+Imin)表示,如图4(c)所示。MTF可以反映不同频率分量的传输能力。高频传输函数反映了传输物体细节的能力,中频传输函数反映了传输物体层次的能力,低频传输函数反映了传输物体轮廓的能力。系统的成像质量可以通过MTF曲线的趋势变化以及曲线和坐标轴之间的区域来判断。
虽然已经制定了评价标准,但关键在于弄清楚TPL如何使成像光学更好地满足这些评价标准。确保3D打印的成像元件达到高质量标准依赖于涵盖设计、制造和表征的关键步骤。在初始设计阶段,材料特性和几何形状被预先确定,通过数值模拟便于量化这些评价标准。在制造过程中,主要目标是生产与设计尽可能接近的结构,需要高分辨率的打印方法以减少缺陷。然而,由于体素的固有形状、邻近效应和聚合度的不完全性,实现锐利的边缘和角点是具有挑战性的,这会导致后处理中的轻微收缩。明智的折衷是必要的,错误鲁棒性分析对于容纳这些因素是至关重要的。此外,由于激光功率的波动、重叠的打印路径以及基板/树脂界面处的反射,光学性能可能会偏离设计。此外,制造的设备评估应在标准条件下进行,例如使用白光进行准直照明,并进行精确的功率测量。通过细致的几何和光学特性分析,获得的数据可以迭代地纳入设计过程中,通过调整制造参数来优化成像性能。此外,可以利用反向设计方法或人工智能(如深度学习)来识别最佳设计,考虑到实际制造限制以满足特定的成像标准。
3. 材料和制造技术
3.1. 材料特性
用于成像设备制造的光敏树脂的固有光学、机械和热性能对最终性能至关重要。常用材料包括有机光敏树脂,如丙烯酸酯,其中Nanoscribe GmbH的IP系列是一种成功的商业选择,以及水凝胶,由于其低机械性能,更适合于软性和动态光学元件。另一种值得注意的类型是环氧树脂,例如成本效益高、透光性强的SU-8,具有可调属性和纳米级制造能力。混合有机–无机材料,如硅酸酯树脂ORMOCER®和硅–锆杂化物SZ2080™,也展示出有前景的制造能力。与无机材料相比,虽然由固化聚合物制成的3D打印透镜具有适用于成像光学的有利特性,但对于不同的环境,稳定性分析是必不可少的,考虑到有机聚合物在不同湿度、温度和pH值下的光学性质可能会发生变化。还应考虑聚合物的可用折射率范围、色散关系和激光诱导损伤阈值,以满足特定的应用需求。此外,在TPL过程中的打印参数,如激光功率和写入速度,也会影响所用材料的性能。性质,如聚合度(DC)、折射率、机械和热稳定性、色散和反射率将随后发生变化,可能会降低成像质量。
制造成像设备所用光敏树脂的固有光学、机械和热性能对最终性能至关重要。常用材料包括有机光敏树脂,如丙烯酸酯,其中 Nanoscribe GmbH 的 IP 系列是一种成功的商业选择,以及水凝胶,由于其低机械性能,更适合于软性和动态光学元件。另一种值得注意的类型是环氧树脂,例如成本效益高、透光性强的 SU-8,具有可调属性和纳米级制造能力。混合有机–无机材料,如硅酸酯树脂 ORMOCER® 和硅–锆杂化物 SZ2080™,也展示出有前景的制造能力。与无机材料相比,虽然由固化聚合物制成的 3D 打印透镜具有适用于成像光学的有利特性,但对于不同的环境,稳定性分析是必不可少的,考虑到有机聚合物在不同湿度、温度和 pH 值下的光学性质可能会发生变化。还应考虑聚合物的可用折射率范围、色散关系和激光诱导损伤阈值,以满足特定的应用需求。此外,在 TPL 过程中的打印参数,如激光功率和写入速度,也会影响所用材料的性能。聚合度(DC)、折射率、机械和热稳定性、色散和反射率等性质将随后发生变化,可能会降低成像质量。
在 TPL 过程中,聚合物的聚合度(DC)值可以通过拉曼显微光谱、差示扫描量热法、相干反斯托克斯拉曼散射和傅里叶变换红外光谱确定。在曝光过程中,树脂中的 C=C 键转化为 C–C 键(图 5(a)),因此可以通过测量这种化学结构的变化来确定 DC。DC 与激光功率呈正相关,与写入速度呈负相关(图 5(b))。通常,最大的 DC 在 50% 以下,原因有两个:(1)在聚合过程中,树脂被聚合成固体,阻止了自由基的扩散,进一步的聚合被终止;(2)进一步提高激光功率或降低写入速度会导致树脂沸腾,因为局部热能积累。聚合阈值定义了稳定结构制造的最小激光功率,燃烧阈值表示由于过热或过聚合导致的稳定结构不可达到的激光功率,两者共同形成制造窗口。该窗口代表了在聚合和燃烧阈值之间的范围,在此范围内可以创建具有默认尺寸精度的结构并实现可接受的 DC。过热会导致局部问题,导致蒸发并形成破坏性的大气泡,而不是增加的 DC 值。气泡的程度受热扩散系数的影响,过热表现为局部加热、区域加热和全局加热三种模式。在制造过程中,可以通过调整激光曝光功率、增加填充或切片距离或改进激光扫描速度来减轻过热。对结构几何形状和质量进行迭代测试对于实现具有合适 DC 的所需结构至关重要。打印结构的机械性能与 DC 密切相关。随着 DC 的增加,结构的杨氏模量和硬度都会增加(图 5(c))。拉伸和压缩试验中也观察到随着激光功率的增加,杨氏模量也会增加。
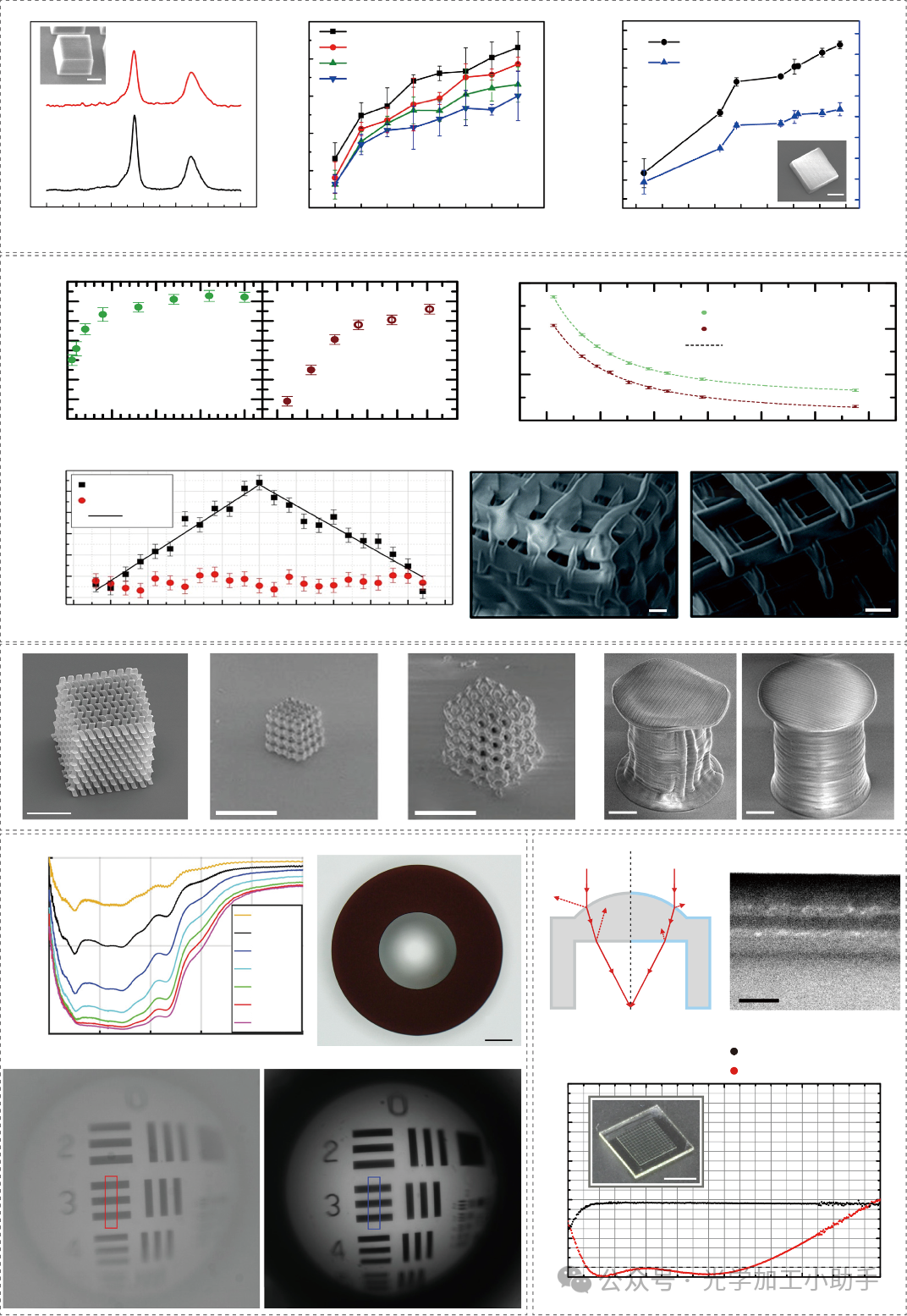

(a)–(c) 影响转化度的材料特性。(a) IP-L 780聚合和未聚合聚合物的拉曼光谱图。(b) 聚合物的转化度与激光功率和写入速度的依赖关系。(c) TPL打印结构的减少杨氏模量和硬度随着转化度的变化情况。插图:打印立方体结构,比例尺:10 µm。(a)–(c) 授权转载自[34],© 光学学会。
(d)–(g) 折射率的影响。(d) 一个光子过程(左)和两个光子过程(右)中折射率(n)的实部依赖于激光功率的依赖关系。(e) IP-dip树脂制备层的折射率n的色散对比(绿色为一个光子过程,红色为两个光子过程)。(d),(e) 授权转载自[38],© 光学学会。(f) 沿x和y轴的TPL打印渐变折射率微型光学器件的测量折射率。[40]约翰·威利和儿子。© 2015年WILEY-VCH Verlag GmbH & Co. KGaA,魏海姆。(g) TPL打印结构的扫描电子显微镜图像(SEM),其RI分别为1.491和1.5215。比例尺:1 µm。与许可[41]转载自皇家化学学会。(h)–(j) TPL打印材料的收缩。(h) 低收缩树脂TPL打印的三维光子晶体结构。授权转载自[42]。版权所有(2008)美国化学学会。(i) 在1000°C的空气中烧结后的丙烯酸酯基(左)和纳米颗粒基(右)树脂打印结构的SEM图像。[43]约翰·威利和儿子。© 2021年作者。由Wiley-VCH GmbH出版的Small。(j) 在常规(上)和UV后固化(下)开发后的显微型蘑菇形柱子的SEM图像。由[44]转载,© 2018年作者。由Elsevier B.V.出版。(k)–(n) 不透明材料的TPL。(k) 对高吸收树脂的打印层厚度的传输功能。(l) 具有原型IP-Black光圈的TPL打印的混合单透镜。(m) 和 (n) 没有和有原型IP-Black光圈的单透镜的成像性能。(k)–(n) [49]约翰·威利和儿子。© 2022年作者。由Wiley-VCH GmbH出版的Advanced Functional Materials。(o)–(q) TPL打印结构的原子层沉积(ALD)。(o) 未涂层和AR涂层透镜的透射示意图。(p) ALD涂层硅参考晶片的剥离面的SEM图像。(q) 涂层和未涂层的TPL打印平面结构的反射率,图中显示了样品两侧的涂层。(o)–(q) . . 授权转载自[51],© 光学学会。
折射率(RI)是受到打印过程影响的另一个关键光学参数。随着激光功率的增加,折射率也会增加(图5(d) 右),而TPL制备的样品的折射率略低于单光子过程(图5(d) 左)[38]。在单光子过程和TPL制备的聚合物中都存在折射率的色散(图5(e))。通常情况下,可以通过Sellmeier色散函数进行拟合,其中n是折射率,λ是波长,参数A和B可以通过椭圆测量来实验确定[39]。通过调节激光功率,结构的折射率可以在一个结构内局部变化。通过采用“之字形”方法,沿水平方向(x轴)从中心向对立边缘增加曝光剂量,从而可以打印出具有单向折射率调制的透镜。测量证实了单个透镜结构内x方向折射率的连续变化(图5(f))[40],因此,通过调制局部折射率可以实现渐变透镜的制造。此外,未聚合树脂的折射率也会影响打印结构的精度,因为树脂的折射率应与最初设计目标镜头所设计的浸入介质的折射率相匹配。PSF可以用来模拟透过树脂的光的三维衍射模式并提供量化的评价标准。例如,为了匹配TPL配置中常见浸入油的折射率,设计了一个折射率为1.52。折射率的不匹配导致了体素的延伸,其长宽比高达6,并且还导致了打印结构的畸变(图5(g))[41]。
TPL材料的机械稳定性是影响光学性能的另一个重要因素,因为它对几何结构和表面形态非常敏感。已经开发了几种材料和材料加工方法来提高机械性能。对于TPL中使用的大多数树脂,当液体树脂聚合成固体状态时会出现一定程度的收缩。另外,可以使用有机-无机混合凝胶来减少收缩。在这个过程中,与无机部分连接的有机基团通过TPL聚合,这导致了树脂的悬挂甲基丙烯酸酯基团之间的连接,没有释放任何分子,也没有观察到明显的收缩(图5(h))[42]。此外,为了减少烧结型TPL的收缩,可以向有机树脂中添加大量无机纳米颗粒[43]。有机丙烯酸酯基结构显示出线性收缩53%,而纳米颗粒基结构在1000℃烧结时只显示出19%的线性收缩(图5(i))。TPL结构的杨氏模量和硬度可以通过增加DC来增强,如上所述。然而,在打印过程中增加DC需要更高的激光功率,这可能会降低最终结构的分辨率。为了避免牺牲分辨率,可以通过后处理,例如紫外线曝光来调节DC。一项比较研究表明,由于机械强度较低,最终的结构会出现变形,而经过紫外曝光的结构更稳定(图5(j))[44]。
常用的聚合物结构容易发生热降解,不适用于激光光学等高温环境应用。将无机物质添加到树脂中,并在打印后烧结,可以生产光学用的耐热器件,例如,钛[45]、硅、二氧化硅[46,47]、镍[48]和氧化锆[43]等可以添加到聚合物基体中。这些混合材料在空气中烧结可以去除有机部分,并产生相应的氧化物来提高热稳定性。上述大多数材料在可见光和近红外范围内具有低吸收率,具有高透明度。对于某些光学应用,如光圈,不透明材料可以帮助增加成像对比度。为此,开发了一些适用于TPL的黑色材料。一个例子是商用原型光刻胶IP-Black(Nanoscribe GmbH&Co. KG)。通过调节厚度,可以调节透射率以获得不同的灰度级别(图5(k))[49]。光学设备,如光圈和吸收管,可以直接打印(图5(l))。成像结果显示,透明光圈呈现出弱的图像对比度(图5(m)),而黑色光圈可以显著提高对比度(图5(n))。黑色材料也可以通过其他技术,如喷墨,沉积到TPL打印的结构上,用于大面积应用[50]。提高光学性能的另一种方法是通过原子层沉积(ALD)将不同材料添加到TPL打印的结构上。例如,通过ALD,可以在TPL打印的透镜上添加由四层钛(TiO2)和二氧化硅(SiO2)交替组成的防反射(AR)涂层(图5(o)和(p)),或者它们可以用于波导以调节光学性能或保护聚合物结构免受恶劣环境的影响。反射率测量显示,ALD涂层结构的反射率比未涂层结构低得多(图5(q))。
3.2. 制造
TPL技术在结构和材料方面具有很大的灵活性。可以使用各种材料,如聚合物[52]、陶瓷[53],甚至金属[54],制造高分辨率的复杂3D结构。TPL是一个三步光化学过程:引发、传播和终止[55]。该过程由飞秒激光束引发(图6(a))。在引发过程中,树脂中的光引发剂同时吸收两个光子并达到激发态(图6(b))。这一步还涉及从光引发剂的分解产生自由基,并且它们与单体结合在传播步骤中生成单体自由基。在最后一步中,单体自由基结合以终止光聚合过程。TPL是一个非线性过程,它使用退化的双光子吸收过程,其中吸收的两个光子的频率相同[56]。只有当曝光剂量超过一定阈值时,才会开始聚合过程,对于恒定的激光功率或反之亦然。这种阈值限制和光学非线性使得能够实现高分辨率,这是其他增材制造技术无法实现的[57]。要制造的结构的计算机生成的3D模型首先在z方向上切片到所需厚度的层,然后将每个切片分割以定义形成激光焦点的激光聚焦点,这些焦点形成激光在x和y方向移动的轨迹。在制造过程中,激光束沿着这个轨迹在液体树脂体积中移动,仅在焦点处暴露树脂以构建所需的结构。然后在开发阶段使用特定的溶剂去除未暴露的树脂以获得最终结构。所获得元素的光学性能受到各种因素的影响,例如内部均匀性、表面粗糙度和结构变形,相关的制造技术已经简要介绍并详细总结在[13]中。在这里,我们主要关注不同衬底和光纤表面的制造方法,这将极大地扩展与TPL相关的成像光学的应用场景。
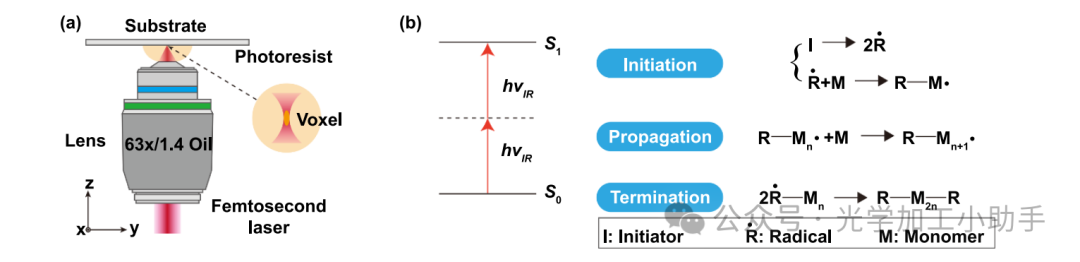
图6. TPL制造的示意图以及在焦点处的三步光化学过程。(a) 飞秒激光束通过高NA物镜聚焦到光敏树脂中,在焦点处诱导聚合过程。(b) 两光子吸收过程和具有引发剂、自由基和单体的三步光化学过程。
3.2.1. 平板基底上的制造。
在硅光子电路和复杂光学系统中,对更高功能集成和微型化的需求主要受到传统制造方法对可实现几何形状的限制。随着TPL和兼容透明树脂的发展,可以实现具有亚100纳米分辨率和任意几何形状的光学组件,这有助于光学的几个领域取得重大进展。此外,该工艺能够在不同的基底系统(如玻璃、硅甚至光纤)上进行制造,使其成为制造集成组件的有希望的技术 [58, 59]。例如,自由形光学元件是芯片和基于光纤的光学中的主要组成部分。使用传统技术,在CMOS芯片或单模光纤(SMF)的端面上制造此类光学元件是困难的。直接在吸收或反射表面上进行激光制造是具有挑战性的,因为存在在聚合阈值处的可能性。研究已经展示了使用飞秒激光写入在具有不同反射率的基底上进行3D打印的能力。在最初的研究中,展示了在具有不同反射率(玻璃、硅和黑硅)的基底上进行印刷,以制造木塔结构。具有最低反射率(b-Si)的基底被看作是为一定范围内的辐照度提供高质量结构。如图7(a)所示,高反射表面会导致损坏的印刷品。
像反射、光场增强和基底-树脂界面的加热等现象会增强聚合反应,从而在结构的基础水平上触发微爆炸。这种爆炸会导致光学性能下降、结构稳定性差以及在反射/金属基底上的脱落。因此,对于这种基底,需要对界面层进行严格的剂量控制。随后在工艺技术和对曝光剂量的精确控制方面的进步使得TPL能够直接在反射表面上制造常规和非常规光学元件,例如具有精确结构控制的LED芯片(图7(b))[63]。另一个先进光学系统的例子是多焦距透镜[64],它是由多焦点衍射区域板和非球面透镜组合而成。图7(c)展示了三焦点透镜以及三个焦点的输出测量。由于这种复合透镜在两个表面上具有特定的曲面轮廓,制造过程是两种工艺的结合。使用TPL在圆形玻璃基板上制造衍射二进制区域板。底部的折射透镜是通过将树脂铸造到所需轮廓的负模具中而制造的。然后,将具有衍射区域板的玻璃基板精确放置在填充树脂的模具表面上,将树脂固化,从而得到最终的复合透镜。对于白内障患者来说,这样的镜头可能特别有用,因为它们可以在不同距离提供更清晰的视觉。对于TPL可用的生物相容材料也使得将该工艺用于这种应用成为可能。将成像光学集成到CMOS平台上,由于可以利用TPL实现的各种镜头轮廓设计,因此越来越受到关注。利用光刻技术制造的MLA构成亚像素图像,将这些亚像素图像拼接在一起形成最终的图像,已经在芯片级成像上得到了证明,这种方式可用于人眼研究[65]。使用TPL直接在CMOS图像传感器上制造的像差校正空气间隔双凸透镜阵列展示了更有效的成像系统[66]。在展示具有90°视场的仿生微型CE摄像机的工作中,使用了一种更简单且对剂量更具容忍性的方法,该摄像机能够成像微生物[67]。在这项工作中,CE透镜首先印刷在盖玻片基板上。这利用了标准的印刷条件,放松了对精确剂量控制以防止结构损坏的需求,这在直接在CMOS上制造时可能是可能的。带有CE透镜的盖玻片随后被切割成较小的尺寸以适应CMOS芯片,使用UV可固化胶粘合(图7(d))。此外,光学元件还可以制造在垂直腔面发射激光器等光源的表面上,以直接执行波前调制[68]。与使用其他制造技术实现的成像系统相比,这种TPL制造的系统在迷你化方面更加优越,对结构轮廓有精确控制,并提供高质量成像。所有这些工作都清楚地定义了TPL相对于传统制造技术的优势,包括过程复杂性,更重要的是,在不同基板上制造成像光学的可实现几何自由度。
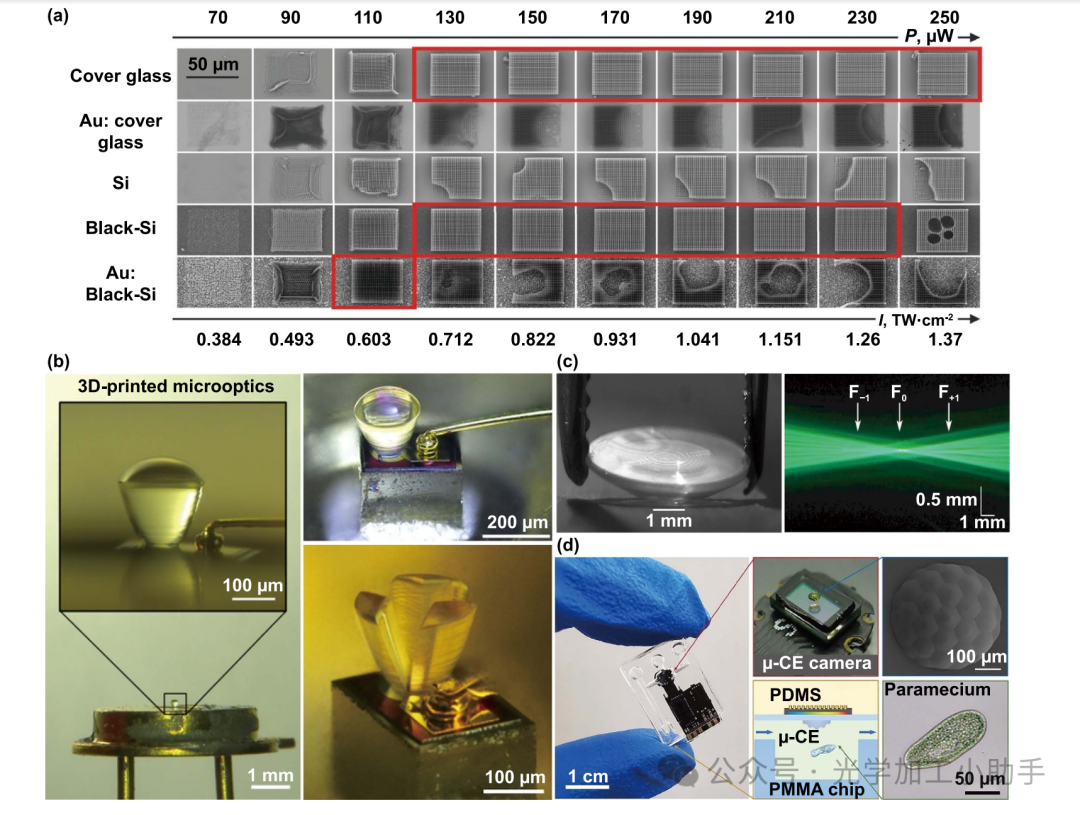
图7. TPL在不同基底上的制备。(a) 在具有不同反射率基底上印刷的木桩结构的SEM图像。红色突出显示框显示了高质量的3D结构。根据[62]的许可重印 © The Optical Society。(b) 封装在TO-18金属封装中的芯片上的3D打印的复合抛物线聚光器(CPC),以及常规CPC(顶部)和非常规准直器(底部)在LED表面的显微图像(右)。根据[63]的许可重印 © The Optical Society。(c) 用TPL制作的多焦点透镜的照片(顶部)和通过透镜后的传播(底部)。重印自[64],© 2016 Elsevier B.V.版权所有。(d) 芯片上CE摄像机系统的照片(左)、CE摄像机(顶部中部)、CE轮廓的SEM图像(右上方)、带有CE摄像机的成像系统的示意图(底部中部)以及使用TPL制作的CE摄像机拍摄的草履虫图像(左下方)。重印自[67]。CC BY 4.0.
对于所有的3D打印光学元件,需要特别注意的一个关键点是界面粘附。增强3D打印元件与基底之间的粘附力对于确保打印物件的整体结构完整性至关重要。可以采用各种方法来增强粘附力。表面处理涉及对基底进行细致的清洁,以消除污染物。使用去离子水、丙酮和异丙醇进行顺序清洁可去除灰尘、油脂或油类。对于熔融硅基底,使用Piranha溶液处理可以进一步增强粘附力。粘附促进剂,如专门用于3D打印的粘合剂喷涂剂或薄膜,可以显著提高打印材料与基底之间的粘合力。例如,用TI PRIME或3-(三甲氧基硅基)丙基甲基丙烯酸酯粘附促进剂旋涂基底,然后短暂烘烤,效果显著。将ITO涂层基底暴露于1,1,3,3,3-六甲基二硅氮烷中有助于改善粘附性。
此外,可以在商业光刻胶IP系列的基底上旋涂并全面暴露一层薄的SU-8。在应用树脂之前,通过O2等离子体预处理基底,或者进行硅烷化以使表面疏水,可以在聚合树脂和基底之间建立化学键。优化第一层设置和剂量增加进一步改善了粘附力。在后处理过程中,使用低表面张力和粘度的液体,如六甲基二硅氮烷和非氟丁基甲醚,可以减轻溶剂蒸发过程中引起的毛细管力导致的缺陷和剥离。使用液态CO2进行临界点干燥可最小化干燥过程中毛细管力的影响。需要注意的是,这些方法的有效性取决于特定的3D打印技术、基底类型和材料,需要一些试验和错误来确定特定设置和应用的最佳组合。
光纤通过全内反射原理发挥作用,即光线在超过临界角的角度反射到包层-芯部界面上。通过芯和包层材料之间的折射率变化,实现了光在光纤内的限制。这种现象使得光能够在光纤芯内传播,促进了高效的长距离传输,能量损耗最小。它们具有灵活性、远程可访问性、高效的长距离光传输以及多功能处理等独特特性,而小的芯直径则实现了对传输光的精确控制。因此,光纤在现代光学中具有多样化的应用,包括光纤通信、波导耦合、非线性光发生、传感、内窥镜成像和光学阱等领域。值得注意的是,光纤内窥镜对于体内组织的实时扫描和成像在医学诊断中尤为重要。尽管光纤具有诸多优点,但也存在一些挑战。其中一个突出的挑战是光在光纤端面的发散,这限制了它们在光学囚禁和聚焦等应用中的适用性。此外,将光子结构集成到光纤上可以增强和控制光纤的光学特性,为基于光纤的传感、成像和通信等应用开辟了新的可能性。
TPL 是一种有前景的技术,可以将 3D 微结构集成到光纤端面上,对于实验室光纤技术的发展具有重要潜力。它已被广泛应用于在光纤端面上进行高精度、灵活性的制造,有利于光子学、微流体学和生物医学应用。此外,TPL 还允许在光纤端部直接制造微光学组件,如轴子透镜、聚焦透镜和环形相位掩模等(见图 8(a) 和 (b)),增强了成像、微粒捕获、照明和光束整形等应用的性能。需要注意的是,大多数其他光刻技术方法都是针对晶片类型结构进行优化的,这使得使用标准方法在光纤端面上创建纳米结构变得极为困难。与传统方法(如聚焦离子束铣削、激光微加工和纳米压印)相比,TPL 在光纤端面上制造复杂几何结构具有更高的分辨率。例如,图 8(c)–(g) 展示了使用直接激光写入(DLW)在光纤上制造具有亚微米精度的光学元件。将光纤安装到打印系统并对其中心进行对准的过程,在使用 3D DLW 实现光学元件精确制造中起着至关重要的作用。为了安装光纤,使用带 V 槽的标准光纤支架,直接连接到 DLW 系统。为了实现正确的定位,采用了背面照明技术。通过 CCD 相机监视光纤的端面,确保光纤的纤芯与 DLW 光束对齐。这一步骤对于防止任何倾斜至关重要,保持整个制造过程中光纤纤芯的中心性。在对准完成后,该过程通过在透镜上放置一小滴光敏材料开始。随后,将光纤浸入光敏树脂中,确保附着到端面。图 8(c)–(g) 中展示了这种制造方法的图示。尽管多模光纤可容纳多种空间模式,但单模光纤有利于传输最主要的波导模式,损耗最小,导致输出光束受外部因素影响较小,对波前整形所需的均匀相位模式至关重要。
金属透镜与超高数值孔径(NA)连接到光纤端面上,具有可调光学束缚和高精度扫描显微镜等优势。直接将其应用于光纤上面临着重大挑战。值得注意的是,Plidschun 等人最近展示了一种专用单模光纤端面上超高 NA 金属透镜(UNM)的设计和 3D 激光纳米制造(参见图 8(h)),该金属透镜是使用标准的 3D 打印系统创建的。对于这种创新,选择了负光敏 IP-dip 光敏树脂,因其具有高分辨率 3D 纳米制造的能力,有助于创建基于 3D 纳米柱的双折射超表面,增强了元光纤在操纵额外光学特性方面的功能。随后,利用特定的画线和切片参数进行了 UNM 结构的打印。光纤金属透镜能够实现接近衍射极限的小焦斑尺寸,典型的半峰宽度为几百纳米。金属透镜的带宽取决于其设计和所使用的材料。这些透镜为在紧凑灵活的平台上进行高性能光聚焦提供了有希望的解决方案。这种金属透镜光纤为利用单根光纤装置实现灵活的光学束缚奠定了基础。作者首次将元光纤应用于微珠和与生物相关的物种的束缚[71],如图 8(i) 所示,这在基于双光束光学设置上实现起来会比较复杂。
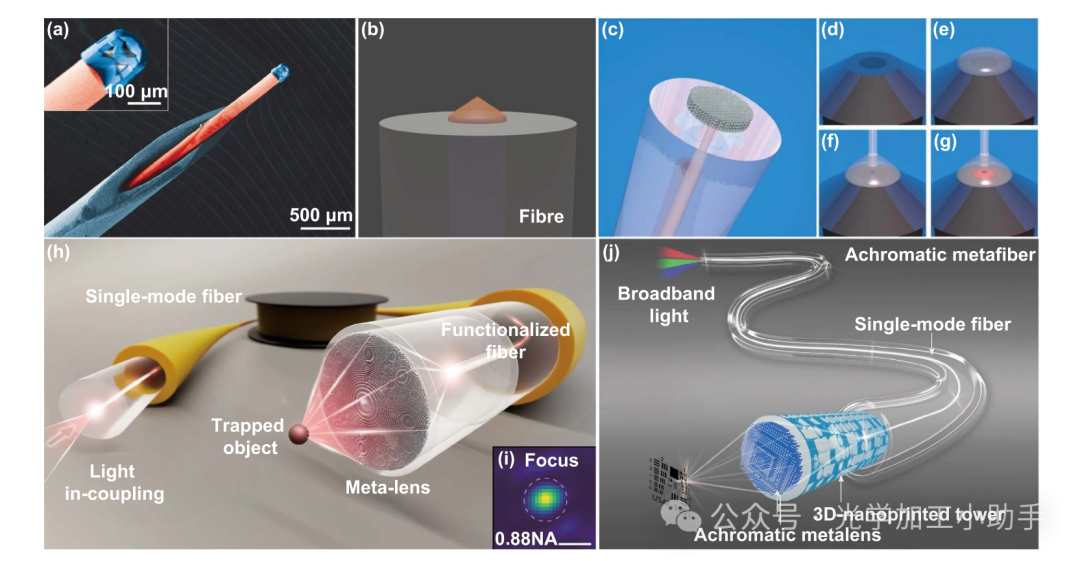
图 8. 光纤上的微光学结构。(a) 直接 3D 激光纳米印刷在单模光纤的核心区域上的锥透镜的 SEM 图像。经授权转载自 [69],Springer Nature。(b) 用 TPL 制造的锥形透镜在光纤上的示意图。(c)–(g) 利用飞秒直接激光书写在光纤上制造的示意图。(c) 通过直接激光书写在结构上细致对准光纤的核心。(d) 在目标透镜上放置光敏树脂珠。(e) 将光纤浸入光敏材料中。(f) 通过 CCD 摄像机查看其照明尖端来微调光纤的位置。(g) 通过 TPL 曝光结构。经授权转载自 [70],CC BY 4.0。(h) 用于光学束缚的金属透镜光纤示意图,在单模光纤上实现了高 NA 金属透镜。(h) 和 (i) 例子显示在水中测得的焦斑强度,使用了一个 500 nm 的比例尺。经授权转载自 [71],CC BY 4.0。(j) 一个色差元光纤的示意图,用于整个通信波长范围的宽带聚焦和成像,在单模光纤的端面上 3D 激光纳米印刷了一个色差金属透镜,与一种用于光纤光束扩展的空心塔结构间隔。经授权转载自 [72],CC BY 4.0。
光纤制成的透镜固有地表现出色散,这在光纤应用中使用时显著地阻碍了它们的聚焦和成像能力。为了解决这一挑战,任等人创新了一种色差元透镜,称为色差元光纤(如图8(j)所示),应用于单模光纤。这一发展与二维平面色差元透镜形成对比,后者在调制群延迟能力上受到限制,因为三维色差元透镜引入了额外的高度维度,提供了广泛的范围来调整群延迟。通过使用TPL进行的三维激光纳米打印,实现了在光纤上制造这种色差元透镜的创新方法。这种色差元透镜的创建是通过使用广泛使用的光刻系统,并精心调整打印设置,包括激光强度和扫描速率。为了增强所得结构的机械韧性,采用了一种有条理的策略,包括在三维纳米打印过程中狭窄的生成和切片间隔。这种方法显著增强了聚合物纳米柱的耐久性,使它们能够承受高纵横比。
3D激光纳米打印的开始是将光纤端放置在物镜透镜下方,然后构建一个中空圆柱结构,在其上层叠了色差元透镜。该圆柱结构的侧面被打上了矩形开口,有助于在化学显影阶段消除未反应的光敏树脂。在3D色差元透镜和圆柱结构之间,打印了一个细长的间隔层,确保了结构顶部的平整均匀表面,对于色差元透镜与光纤的无缝融合至关重要。开发的色差元光纤的特点是能够在没有衍射极限的情况下进行聚焦,并且在整个近红外通信频谱(1.25 µm–1.65 µm)上具有色差特性。这使其成为一个紧凑、宽范围的解决方案,非常适合建立超宽带共焦内窥镜系统。此外,基于TPL制造平台,已经实现了一系列光子器件,如光纤布拉格光栅、多模干涉仪和法布里–珀罗干涉仪。TPL和可加工材料的进步使得能够在3D中制造具有不同功能的高度复杂的结构,这可能推动了光纤实验室技术的前沿。
4.成像应用
4.1. 折射透镜
4.1.1. 单个透镜
TPL是一种制造折射微透镜的多功能技术,通过在光敏树脂内部扫描一个紧密聚焦的激光点来形成。这些微透镜是直接由计算机生成的模型通过TPL制造的,不需要任何光掩模,因此可以自由设计任意的三维形状。典型的微透镜形状有球形、非球形和自由曲面形状。微透镜的确切形状控制着光在材料内传播时的相位累积,从而产生一个焦点。对于具有旋转对称轴的球形和非球形微透镜,表面轮廓由以下方程给出:

其中,z是微透镜的凹陷量,r是距离光轴的径向距离,C是透镜的曲率,K是圆锥常数,而A4、A6等则是更高阶的非球面系数,用于校正像差。与其他形状相比,球形微透镜最简单设计和制造,因为其焦距可以通过透镜制造方程轻松预测:
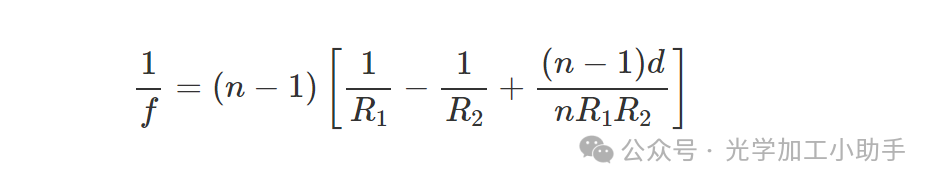
其中,f为焦距,n为折射率,d为厚度,R1和R2分别为透镜两个相对表面的曲率半径。为了简化光学设计和光线追迹模拟,当透镜的厚度远小于曲率半径时,可以将其近似为薄透镜(d = 0)用于剖面成像。Malinauskas等人展示了由折射率与玻璃衬底匹配的光刻胶制成的具有不同曲率半径和焦距的球形微透镜,以最小化光学损失。然而,球形微透镜存在各种像差,尤其是球面像差,即当透镜不同部分的入射光线汇聚到不同的焦点时发生。通过设计和制造非球面微透镜,可以在一定程度上纠正像差。Wu等人展示了椭圆和抛物线微透镜以减小球面像差。此外,Wang等人展示了具有不同数值孔径(0.3、0.6、0.9)且在三个波长(561 nm、590 nm和630 nm)上没有像差的非球面微透镜。通常,数值孔径较高的微透镜更容易产生像差,并且需要优化更高阶的非球面系数来校正像差。与球形和非球面微透镜不同,自由形态微透镜没有旋转对称轴,因此具有独特的光学性能。Lin等人展示了产生大焦深和贝塞尔型光强分布的对数轴面透镜。此外,Li等人展示了一种基于全反射的自由形态光学元件,用于光纤探针的侧视。
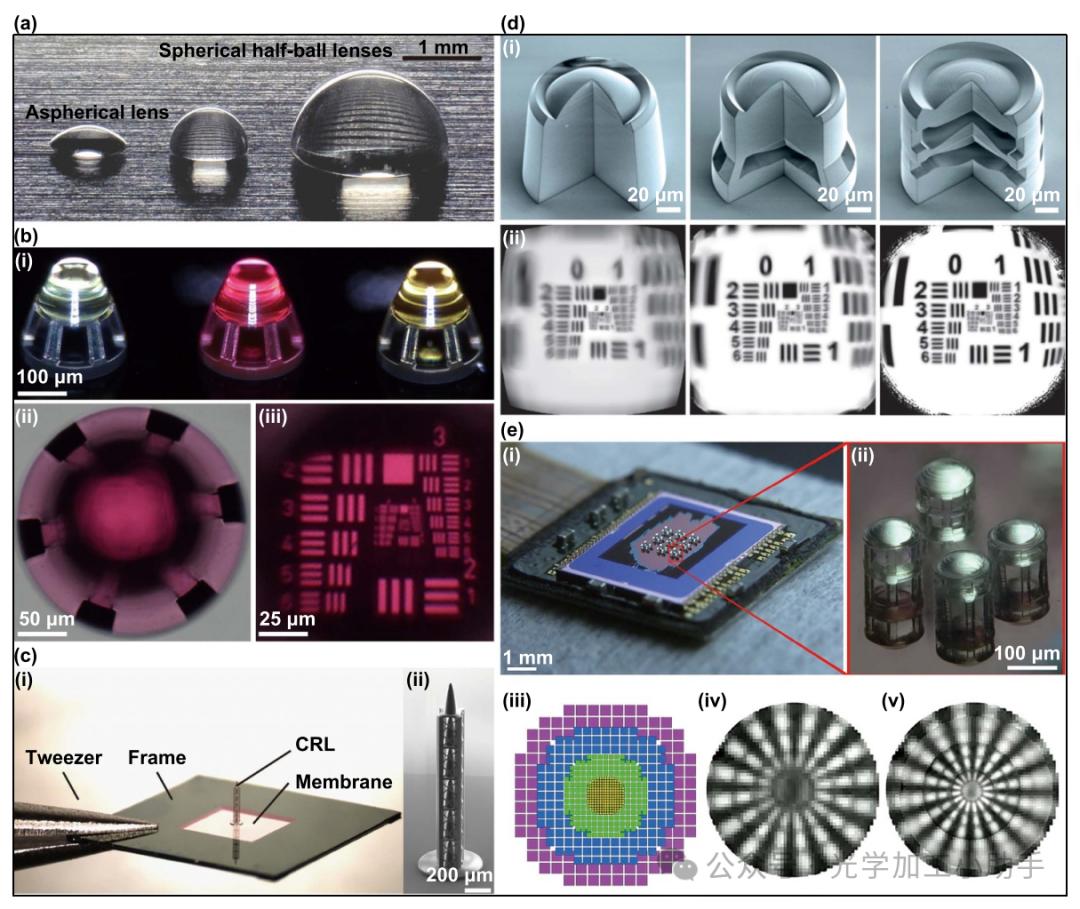
就制造质量而言,所有折射微透镜的一个重要要求是具有光滑的表面轮廓,以减少不必要的光散射并实现高聚焦效率。这里讨论了实现光滑表面轮廓的三种方法。一种方法是通过以更细的离散化步骤打印或变化激光曝光剂量来增加体素重叠的程度,如Takada等人所示。然而,如果重叠度过高,可能会在光刻胶中引起微爆炸并损坏微透镜结构。另一种方法是使用自适应写入策略,例如具有不同垂直离散化步骤的环形扫描。使用这种策略,Guo等人制造了一个具有15 nm表面粗糙度的微透镜(可见光的λ/20)。尽管如此,自适应写入策略仍需要变化的激光曝光剂量来打印高分辨率特征。最后一种方法是使用基于选择性热重流的后处理技术来平滑微透镜的表面,如Kirchner等人所示。虽然这种技术可以实现亚10 nm的表面粗糙度,但也可能改变微透镜的最终形状,因此需要仔细控制的工艺参数。在尺寸方面,由TPL制造的透镜通常具有几十到几百微米的直径,这是由于扫描激光的有限写入场的限制。一个挑战是将透镜直径增加到毫米级别以用于实际设备。原则上,可以通过将其分成较小的可打印区域并逐个打印每个较小区域来打印大型透镜,但这将导致接缝痕迹,从而降低透镜的光学性能。为了最小化接缝痕迹,Dehaeck展示了一种自适应缝合算法,可减少细长物体的总缝合块数量高达40%。Jonušauskas等人展示了同步线性阶段和伽尔瓦诺扫描仪,允许在打印过程中动态移动写入场,以创建无接缝结构。然而,通常最好通过使用具有较低打印分辨率的大写入场目标来完全避免接缝痕迹,从而制造毫米级透镜,正如Ristok等人所示。