前面小编跟大家分享了几类利用双光子3D打印技术制造的微纳光学产品,包括,
A.硅光芯片波导出光口打印透镜用来耦合
B.在光纤端面打印超透镜用于光纤成像
C.在光纤端面打印各种结构,实现对光斑的任意整形
除此之外双光子3D打印技术还有很多应用,比如
1.打印复杂的结构
2.打印非球面透镜,菲涅尔透镜,超透镜,自由曲面透镜,衍射透镜,微透镜阵列等等。
大家可能对双光子打印在光学的应用已经有了一个简单的了解,
本文小编将跟大家分享一篇文章,从原理等方面对双光子激光3D打印的技术进行进一步的介绍。
划重点(双光子3D打印代工)
在光纤端面亦或其他基底材料上通过双光子3D打印的方式一直是科研工作者研究的关注点,但是由于高精度双光子3D打印的设备极其昂贵,技术也较为前沿,许多科研工作者乏于寻找可靠的,高效率的加工提供商。
小编也很有幸,曾经见到国内有团队已经实战在光纤端面做各种超结构,并且得到了客户满意的效果。
因此如果您有需求,可以联系小编为您推荐成熟的双光子3D打印企业,加速您的创新。
如果你也爱好 半导体,光学,光纤,硅光集成等技术及应用,可以添加小编,一起畅聊技术,市场和应用。
看原文请联系小编免费领取
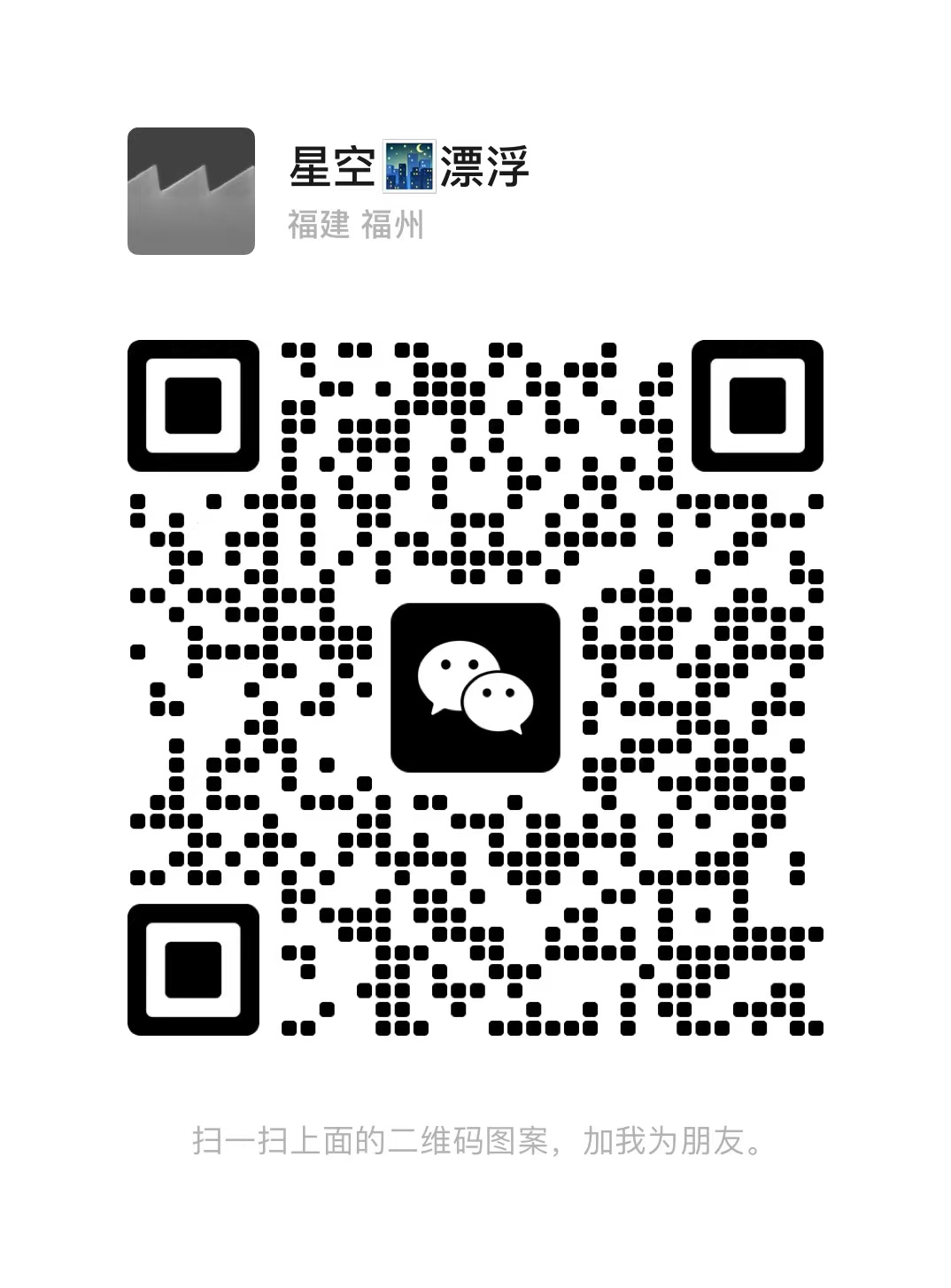
基于双光子直写的微纳光学器件研究进展
摘要 双光子直写技术凭借其高精度、任意三维结构刻写、高成本效益、材料设计高自由度等特点,已被成功应用到多种微纳光学器件的刻写中。基于双光子直写的微纳光学器件应用不断拓展,对刻写分辨率和通量都提出了更高的需求。超分辨激光纳米直写和高通量激光直写技术使得双光子直写具有 nm 级精度与 cm 级尺寸的跨尺度加工能力,进一步拓展了基于双光子直写的微纳光学器件研究领域。本文首先对双光子直写原理进行概述,介绍本课题组在利用双光子直写技术制造衍射光学器件、光纤集成器件方面的研究进展;然后,介绍本课题组在使用超分辨激光直写技术制备纳米光子器件方面的拓展研究,并展示了高精度、高通量激光直写技术在大面积刻写微纳光学器件上的技术优势。
1 引言
微纳光学器件是光子学与微纳科技相结合的产物[1],是新型光电子产业的重要发展方向之一。微纳光学器件可通过结构设计有效灵活地实现光场调制,目前在许多领域中发挥着重要的作用,如光子集成芯片、光通信、光存储、传感成像、显示、固态照明、生物医学、光伏能源等[2-3]。微纳光学器件应用的不断拓展需要微纳制造技术的发展作为技术支撑,使得理论设计结构得以转化为实际器件。为了满足不同微纳光学器件的刻写需求,器件制备需要采用多种微纳制造技术。这些技术包括激光直写[4]、干涉光刻[5]、掩模投影光刻[6]、纳米压印[7]、电子束光刻[8]、离子束刻蚀[9]等。干涉光刻可通过面曝光实现大面积快速刻写,但不能自由定制刻写图形,适用于光子晶体等周期性结构刻写[5]。掩模投影光刻和纳米压印都适用于具有高分辨率特征的简单快速制造,但其制造都需要先制造模板,结构刻写灵活性较低[7]。使用聚焦的带电粒子(离子和电子)进行刻写可以达到10 nm以内的精度,但电子束光刻和离子束刻蚀都需要真空环境,系统成本较高且难以刻写三维结构。基于双光子聚合的激光直写(以下简称“双光子直写”)技术凭借其亚微米级分辨率、任意三维结构刻写能力、高成本效益等特点,成为制造微纳光学器件的重要技术之一。双光子聚合具有非线性的特性,可以将光化学转换的区域局限于激发光的聚焦中心区域[10]。通过激光焦点与基板之间任意三维位置的相对移动实现复杂的三维结构刻写。光敏材料曝光后的区域会发生聚合,而未曝光区域能溶于显影液,并在显影过程中会被冲洗掉,由此经过曝光与显影后在基板上得到一个独立的微结构[11]。
基于激光直写的器件主要由聚合物材料组成[12],且材料的种类主要取决于所使用的光刻胶成分。用作光刻胶的材料可以是液体、凝胶或固体。此外,光刻胶既可以完全由有机分子组成[13],也可以是有机-无机杂化物[14]。聚合物种类多,可结合新型材料或活性材料实现设定功能等特点[15]。聚合物材料设计的高自由度与双光子直写曝光的高灵活性相结合,使得基于双光子直写技术的微纳光学器件应用得到了广泛的研究[16],并在衍射光学[17-18]、成像光学[19]、光纤光学[20]彩色光学[21]、集成光学[22-23]、光数据存储等领域发挥了重要作用。
基于双光子直写的微纳光学器件应用不断拓展,对双光子直写技术的性能提出了更高的要求。在刻写分辨率方面,双光子直写主要受到光学系统的衍射效应和光刻胶材料中临近效应的限制。为了进一步提升刻写分辨率,受到受激辐射损耗(STED)显微镜技术的启发,研究者们提出了基于边缘光致抑制(PPI)的超分辨直写技术,从而突破衍射效应并减弱临近效应[24]。使用超分辨直写技术可以将双光子直写的加工精度推进至nm尺度,并成功应用于光子超材料、光数据存储、生物医学等领域[24]。在刻写通量方面,双光子直写技术主要受限于单焦点串行的刻写模式,相比于面曝光的投影光刻,其刻写通量较低,难以实现大面积的快速制造。采用多通道的并行刻写可以有效提高双光子直写的刻写通量[25],但非周期性结构的并行刻写需要对多通道进行灵活快速独立调控,这仍然是一个重要的挑战。
浙江大学极端光学技术与仪器全国重点实验室联合之江实验室,以双光子直写技术为出发点,为实现超分辨和高通量刻写,提出了基于单色PPI的超分辨激光直写技术[26]、双通道PPI超分辨激光直写技术[27]和基于转镜的高速并行直写技术[28]等双光子直写增强技术,并将这些技术应用到微纳光学器件中。本文主要介绍刘旭团队近年来围绕双光子直写技术、超分辨激光直写技术和高通量激光直写技术开展的系列微纳光学器件应用研究,详细论述基于激光直写的微纳光学器件研究进展。
2 双光子直写器件
2.1 基于双光子聚合的激光直写技术
基于双光子聚合的激光直写系统结构如图1所示,其关键器件主要包括飞秒激光器、功率控制器(如声光调制器等)、振镜扫描仪、物镜、三维位移台。实现双光子聚合主要依靠飞秒激光与光刻胶材料之间的光化学反应。用于双光子直写的光刻胶材料通常包括光敏剂和单体树脂。飞秒脉冲通过双光子激发将光敏剂分子从基态(S0)激发到激发态(S1),如图1所示。分子被激发到激发态(S1)后,可通过系间窜越(ISC)到三重态(T1),并最终产生自由基[29]。自由基与单体树脂发生交联聚合反应并形成固体聚合物。未形成固体聚合物的部分会溶解于显影液中,而固体聚合物会在显影过程中被保留下来。
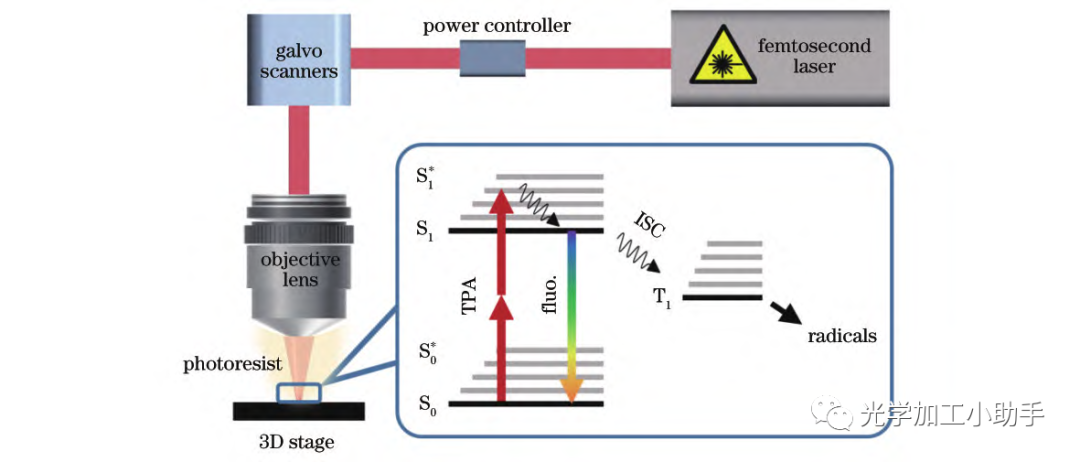
图1 基于双光子聚合的激光直写技术原理
双光子直写主要使用的光刻胶材料起初与传统激光直写的相同[15]。随着双光子直写技术的发展,为了进一步提高光敏剂的非线性吸收能力,科研工作者开发了分子结构中具有大共轭结构及电子给受体的高吸收截面双光子光敏剂,如D-π-A、D-π-D、A-π-A等[30]。电子给体及电子受体的给受电子能力越强,分子的共平面性越好,分子结构的共轭性越好,共轭结构越大,越有利于提升其双光子吸收截面。
双光子直写技术与基于单光子吸收的传统激光直写技术的主要区别可归纳为:1)单光子吸收是一个线性过程,其吸收概率与激发光的强度成正比;双光子吸收是一个非线性过程,其吸收概率与激光强度的平方有关。因此,由双光子吸收引发的聚合被限制在激光焦点的中心区域内[11],相比于传统激光直写,双光子直写具有更高精度的三维层切刻写能力[31]。2)单光子吸收选用的激发光波长需要处于材料的吸收带内,多使用紫外或近紫外的波段;双光子吸收的激发波长一般选择在材料吸收带的二倍波长范围内且在吸收带之外,以避免单光子吸收。3)基于单光子吸收的传统激光直写可以选用连续激光器的出射激光作为激发光,而双光子直写技术中的激发光通常需要使用飞秒激光。飞秒激光通常具有如下特点:平均光功率为nJ量级,峰值功率为MW量级,脉冲宽度约为100 fs,以及脉冲间隔约为10 ns。飞秒激光的高瞬时能量显著提高了双光子激发概率,而低占空比则降低了热损伤[32-33]。双光子聚合可以刻写任意的三维结构,并且具有亚微米量级的聚合体素[31],目前已经被广泛应用在激光直写中。
2.2 衍射光学元件
衍射光学元件(DOE)具有衍射效率高、色散性能独特、设计自由度高、体积小且厚度薄、易于多功能集成等特点[34],已被成功应用于激光加工[35]、全息照明[36]、光通信[37]和显微成像[38]等领域。目前,灰度投影光刻、干涉光刻、纳米压印、电子束直写、双光子直写等技术已被应用于衍射光学元件的制造中[34]。其中双光子直写技术凭借其高精度、高刻写灵活性、低成本等优点成为衍射光学元件的重要制造技术之一[39-41]。本课题组使用双光子直写技术在盖玻片基底上刻写了具有聚焦功能的衍射光学元件阵列,并利用差分共焦定焦技术对焦面进行高精度定位。刻写系统如图1所示,其中使用的激发光波长为532 nm,脉宽为140 fs,所使用的功率控制器为声光调制器。刻写及表征结果[42]如图2所示。阵列由8×10个相同的衍射光学元件组成,单个元件由一系列同心圆环组成,相邻圆环的半径相差1 μm,最大直径为20 μm,相邻两个衍射光学元件的中心距离为21 μm,刻写功率为6 mW,如图2(a)所示。衍射光学元件阵列通过振镜和压电平台组合运动的方式进行刻写,结果如图2(b)所示。将差分共焦定焦技术应用到双光子直写系统中,定焦精度可以达到5 nm,定焦的重复精度达到15 nm[42]。使用差分共焦定焦技术后,在整个刻写范围内都可以保持较好的刻写效果。图2(c)为衍射光学元件的扫描电子显微镜(SEM)图像。使用FDTD软件对单个衍射光学元件进行建模仿真,并将波长为520 nm的圆偏振平行光入射到衍射光学元件阵列,在其最大光强焦点处得到的光强分布如图2(d)所示。根据表征系统的参数对表征结果进行仿真,得到的截面轮廓如图2(e)所示。可以看到,曲线主瓣的半峰全宽(FWHM)约为0.49 μm,旁瓣间距约为1 μm。对实际刻写的结构进行表征,得到的焦面光强分布的截面轮廓如图2(f)所示,其FWHM约为0.47 μm,且旁瓣间距也约为1 μm。实际结构的表征结果与仿真结果具有高度一致性,说明双光子光刻系统可以实现很高的刻写质量。
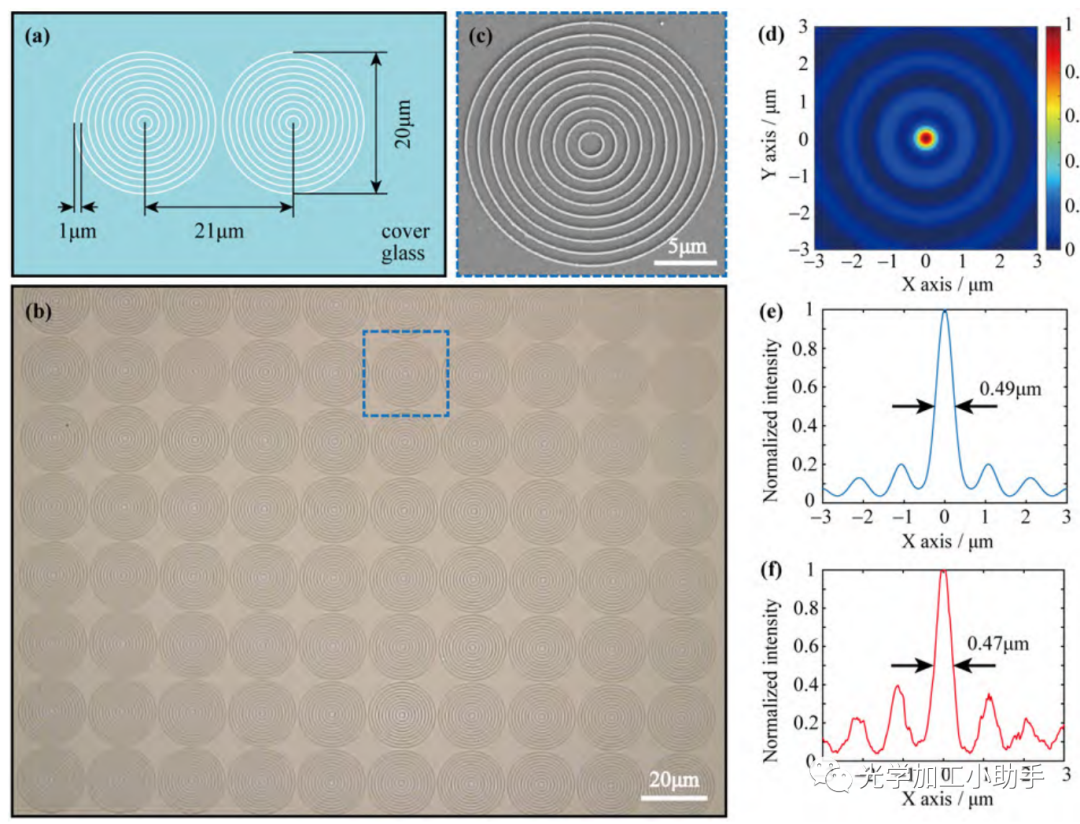
图2 具有聚焦功能的衍射光学元件阵列刻写及表征结果[42]。(a)刻写结构参数;(b)结构阵列刻写结果的光镜图;(c)图2(b)中蓝色矩形虚线框内结构的SEM图;(d)设计结构在最大光强焦点处的归一化光强分布仿真结果;光强分布图的(e)仿真强度分布曲线和(f)实测强度分布曲线,二者的半峰全宽分别约为0.49 μm和0.47 μm
透镜是成像系统的基础,传统透镜利用折射原理实现光场聚焦。因此,随着数值孔径的增大,透镜的厚度和质量也需要不断增加,以满足聚焦要求[43]。衍射透镜作为一种平面光学器件,可以在很薄的厚度下实现甚至超越传统光学元件的性能[44],有着极大的应用潜力。消色差衍射透镜的孔径被划分为多个环,每一环的高度是优化变量,评价函数则反映了消色差衍射透镜的调制效率和分辨率,通过优化算法选取每一环的最优高度,可使评价函数达到最大值[45]。在制造方面,消色差衍射透镜可以使用折射率较低(约1.5)的材料,其最小特征尺寸一般在μm量级。双光子直写技术采用点扫和层切的方式进行刻写,无需掩模版,结构刻写方式灵活,加工效率高,非常适用于具有不规则轮廓的衍射透镜的刻写。图3(a)展示了基于双光子直写的消色差衍射透镜,该结构的直径为300 μm,环宽为0.6 μm,最大厚度为2.7 μm,相邻相位阶数的最小高度差为0.1 μm。3个代表性波长480 nm、560 nm和640 nm对应的仿真点扩散函数如图3(b)所示,3个波长都聚焦在z=510 μm处,对应的第 43 卷第 16 期/2023 年 8 月/光学学报数值孔径NA为0.28。3个波长的半峰全宽分别为0.933 μm、1.067 μm和1.200 μm,与衍射极限(0.5λ/NA)非常接近。仿真的聚焦效率分别为85.97%、73.32%和69.19%,平均效率达到76.16%。为满足300 μm直径的透镜刻写要求,本课题组采用NA=1.05的30×物镜进行刻写,以扩大光束扫描视场。使用10 mm/s的速度进行圆周扫描,可在7.3 min内完成整个结构的刻写。图3(c)、(d)展示了剖面轮廓的结构细节,双光子直写结合光束圆周扫描和层切刻写的方法可满足消色差衍射透镜最小环宽和最小高度差的精度要求。本课题组实现的消色差衍射透镜具有可见光波段内消色差、μm级厚度和近衍射极限的特点,有望进一步应用于光纤内窥、显微成像等领域。
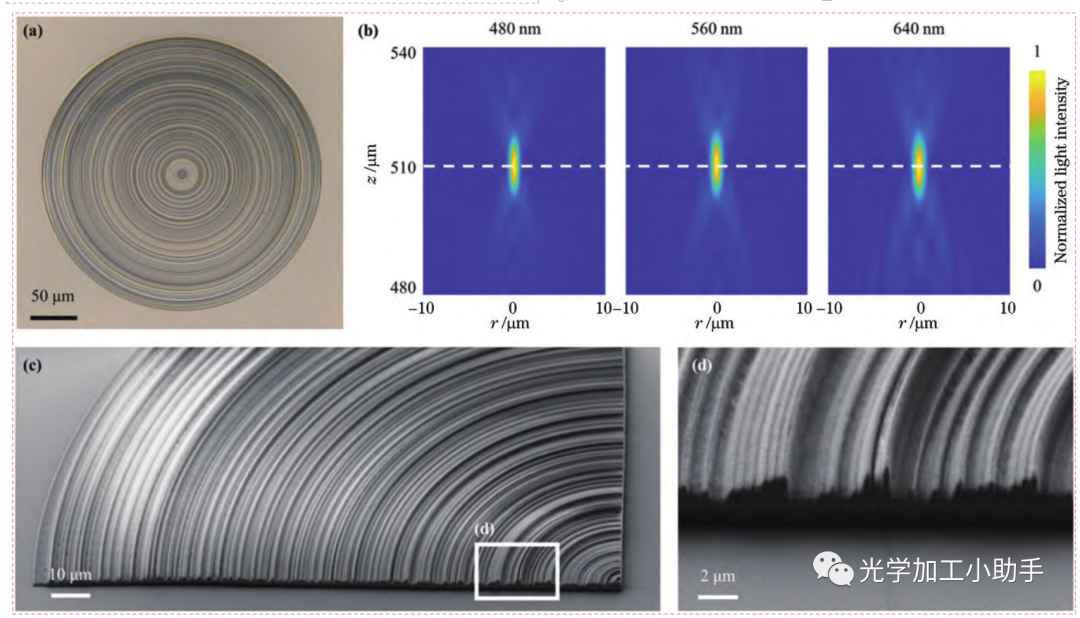
图3 消色差衍射透镜。(a)光镜图;(b)消色差聚焦在最大光强焦点处的归一化光强分布仿真结果;(c)分块结构的SEM图;(d)剖面轮廓放大图
2.3 光纤集成器件应用
光纤光学凭借其高灵活度、紧凑设计、长距离有效传播等优势,已经成为多个科学研究领域的重要技术手段,如长距离通信[46]、生物医学成像[47]、光纤传感[48]等。近年来,随着光纤光学的飞速发展,多功能光纤的需求迅速增长,光纤端面集成功能性器件的研究与制造进入快速的发展阶段[49]。基于双光子直写技术,研究者能够开发出全新的光纤集成功能性器件[20]。双光子直写技术具有高精度和高灵活性,能够在光纤端面上或在光纤内部制造微纳结构。此外,聚合物材料可以突破光纤固有材料的限制,为光纤集成功能性器件材料提供更多的可能性。目前,双光子直写技术在光纤集成应用中已成功制备出微透镜[19,23]、衍射光学元件[18,50]、超表面[51-53]、相位板[54-55]、微机械器件[56]等功能性器件。本课题组目前主要针对光纤集成自由曲面透镜和涡旋相位调制器件展开研究。在单模光纤端面打印自由曲面透镜,实现对光线出射光束的直接整形,此处自由曲面透镜的入射面为平面,并紧贴光线端面,出射面为自由曲面。首先,将来自激光器的光束耦合到光纤,采用光束质量分析仪测量出光分布,即自由曲面透镜的入射光分布。然后,将光纤出射端面作为点光源,并以该发光点为原点建特邀综图片立球面坐标系[57],并结合斯涅耳定律和能量守恒定律建立光束调控MA方程[57],得到式中:θ 和 φ 分别为球坐标系的方位角和极角;r 为光源与 自 由 曲 面 上 离 散 点 的 距 离 ;系 数 Ai(i=1,2,… ,5)为 rφ、rθ、r、θ 和 φ 的函数;Ω1和 Ω2分别为光纤出射光束强度 I(θ,φ)和目标照度 E(tx′,ty′)的分布区域;∂Ω1和∂Ω2分别为区域 Ω1和 Ω2的边界。最后,采用牛顿迭代法求解式(1),得到自由曲面的面形分布。采用双光子直写技术将所设计的自由曲面透镜打印在光纤端面,如图4(a)~(c)所 示 ;将 来 自 同 一 激 光 器 的 光 束 耦 合 入 光纤 ,自 由 曲 面 透 镜 的 出 射 光 束 分 布 如 图4(d)所 示 ,可以看到,光束被整形为方形的照明光斑。在光纤端面直接打印透镜实现光束整形,可进一步推进光束整形系统的小型化,为光纤光束整形带来新的解决方案,得到更紧凑、高效的整形结构,在显微照明、内窥照明、光纤通信等领域具有良好的应用前景。
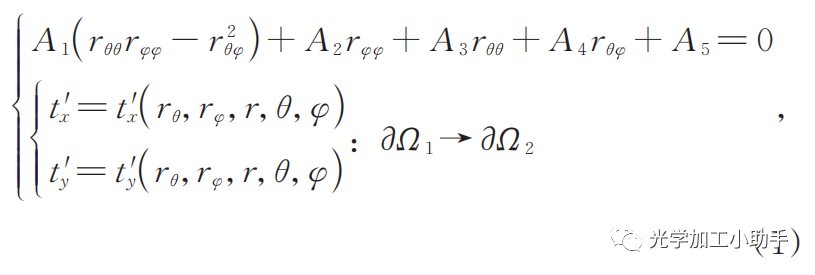
图4 光纤端面上的自由曲面透镜结构。(a)~(c)光纤集成自由曲面透镜的光镜图;(d)光束整形的实验结果
涡旋光束在受激辐射损耗(STED)显微成像[58-59]、暗斑单分子定位(MINFLUX)显微成像[60]、超分辨激光直写[61-62]等技术中都起着重要作用。在过去的几十年中,研究者们提出了许多技术来产生涡旋光束,例如使用涡旋相位板、基于空间光调制器或数字微镜器件实现相位或振幅调制、使用超表面或基于光束干涉等[63]。涡旋相位板是一块具有螺旋厚度的相位板,其光学厚度与方位角呈线性关系。使用涡旋相位板产生涡旋光束的一个显著特点是调制效率高,当入射光具有与涡旋相位板相同的旋向时,中心强度可接近于0。涡旋相位板凭借其高调制效率、低成本、易于集成等优点成为产生涡旋光束的常用光学器件之一。相位变化范围为[0,2π]的涡旋相位板的相位分布φ可表示为φ(r,θ)=θ,其中(r,θ)表示涡旋相位板平面的极坐标。涡旋相位板对应高度h可表示为
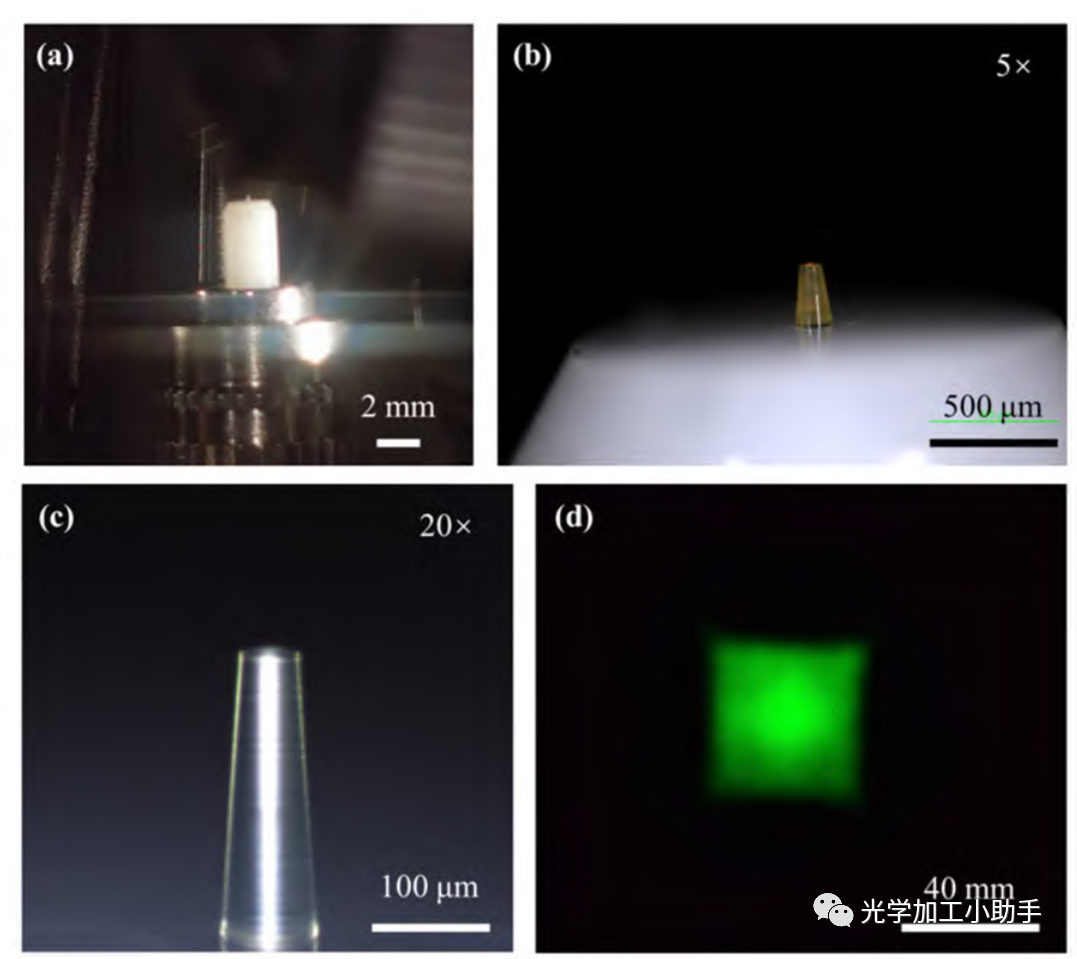
式中:Δn 表示涡旋相位板材料与空气的折射率差;k 为入 射 光 的 波 数 ,可 由 k=2π/λ 计 算 得 到(λ 为 激 光 波长)。由式(2)可知,涡旋相位板的高度分布主要与方位 角 有 关 ,调 制 相 位 为 0 和 2π 时 的 高 度 差 为 λ/Δn。
图 5(a)和(b)展示了使用双光子直写技术刻写的涡旋相 位 板 结 构 ,使 用 的 激 光 波 长 为 640 nm,相 位 板 直 径为 150 μm。相位板离光纤端面的高度为 150 μm,这可以利用光纤端面出射光束的传播特性扩大相位板入射光束的直径。得益于高层切精度和高刻写分辨率,涡旋 相 位 板 呈 现 出 光 滑 的 曲 面 分 布 。 图 5(c)所 示 为640 nm 波长的激光从光纤端面出射,经过该涡旋相位板结构调制后呈现的光强分布。可以看到,出射光束经过光纤集成器件后被调制为涡旋光束,呈现出空心暗斑的强度分布。这有望进一步应用于超紧凑型的超分辨成像系统或超分辨激光直写系统,可以显著缩小系统体积,降低系统结构复杂度。

图 5 光纤端面上的涡旋相位板结构。(a)(b)光纤集成涡旋相位板结构的 SEM 图像;(c)实验中经过涡旋相位调制后的光纤出射光斑强度分布