4.1.温度
Au/Si共晶键合是Au和Si之间的相互扩散过程,热量在该过程中起着主要作用。当键合温度超过共晶点(363℃)时,Au和Si相互接触,在扩散过程中可形成具有共晶成分的液相合金。随着时间的推移,液相层变厚。在随后的冷却过程中,液相不断地与这两种金属交替,每种金属分别在其原始固相的基础上生长、结晶和沉淀。因此,两种材料之间的共晶合金将两个晶片紧密地结合在一起。
考察并分析了键合温度对Au/Si共晶键合的影响。粘接温度为380℃,粘接强度为6.7MPa。它非常脆弱,以至于在刀片测试过程中粘合的晶圆很容易分离。观察分离的表面,硅已经发生轻微的深度扩散到金中,并且在分离的表面上看到一些硅颗粒,如图2a所示。然而,粘合质量不足以满足进一步的应用,特别是真空包装。因此,接合温度已升至400℃,测得的接合强度为66.8MPa。刀片测试后,大块硅从体硅上剥离,这表明结合强度高于体硅,如图2b所示。可以得出结论,要获得高接合强度,需要 400 °C 的高接合温度。根据 S. Lani 等人的说法。[14],需要较高的键合温度主要是由于键合材料中存在杂质元素(如氧和氢),或者整个晶圆上的温度不均匀,导致Au和Si之间发生部分反应。此外,SB6e的设定温度与实际温度之间的差异也是导致键合温度较高的另一个因素。正如预期的那样,随着键合温度的进一步升高,键合强度也随之增加,如表 1 所示(样品 3 和 8)。从式(2)可知,较高的接合温度会导致较厚的 Au/Si 合金,因此接合强度会增加。然而,高键合温度总是会导致金属线熔化或温度敏感器件的性能下降[15]。因此,最佳键合温度为400℃。
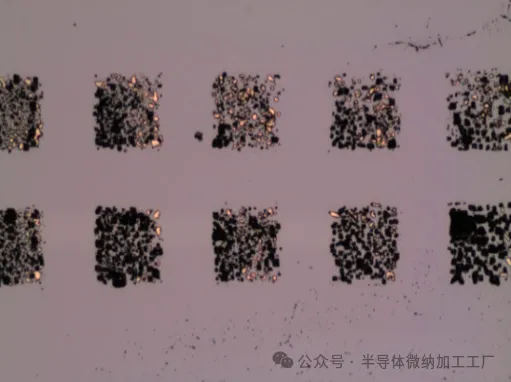
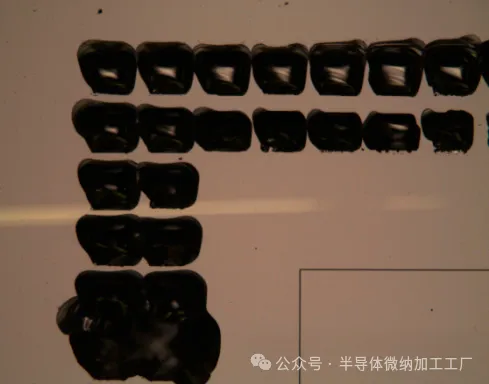
图2.不同粘合温度下分离玻璃表面的光学显微镜照片。(a) 380℃键合,可以看到一些Si颗粒;(b) 在 400 °C 下键合,大块硅从块状硅上剥落。
表 1. 不同参数的粘合质量。
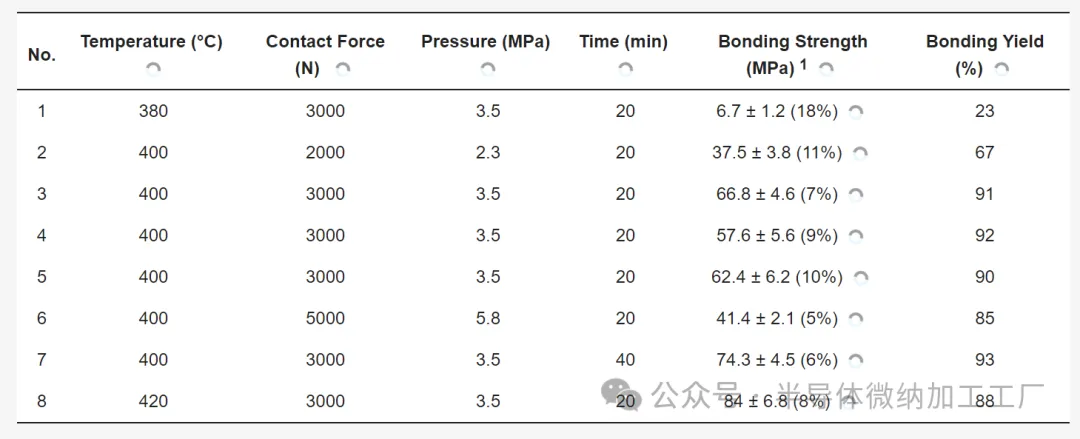
4.2.加热/冷却速率
还研究了温度加热/冷却速率对成功共晶键合的影响。图 3a 显示在 15 °C/min 的高加热/冷却速率下粘合失败。通过刀片测试可以很容易地将键合晶圆从键合界面分离。与 Bokhonov 等人的观察类似。[16],在分离的金表面上看到了一些枝晶结晶。通过EDS分析表面的成分元素。结果显示,点 1 的化学元素如下:Si(29.82 wt%)、Au(52.72 wt%)、Ti(2.8 wt%)和 W(14.67 wt%),如图 3b 所示,而第2点的化学元素如下:Si(10.87wt%)、Au(69.46wt%)、Ti(3.43wt%)和W(16.24wt%)。两种分析都忽略了碳 (C) 和氧 (O) 元素的影响。点2处的少量硅是由玻璃基板引入的。点 1 处 Si 含量的增加表明形成了液态 Au/Si 合金。然而,由于枝晶的形成,结合强度较弱。Au/Si共晶键合是液相转变为固相的过程,并且在凝固过程中发生结晶。当加热/冷却速率较高时,液相中的原子很容易扩散,而固相中的原子由于扩散速率较低而难以扩散。因此,后一个晶体的成分与前一个晶体的成分不同,导致枝晶的形成。枝晶会导致晶体方向偏离其先前的生长方向,并会阻碍Au/Si合金的进一步凝固。结果,无法形成稳定且连续的Au/Si合金。另一方面,低加热/冷却速率延长了凝固过程,表明液态合金时间更长。因此,液态Au/Si合金很容易扩散到非键合区域(称为金属挤压),特别是在高接触力下,这将在下一节中讨论。此外,设备的电气连接可能会因严重的金属挤压而损坏。
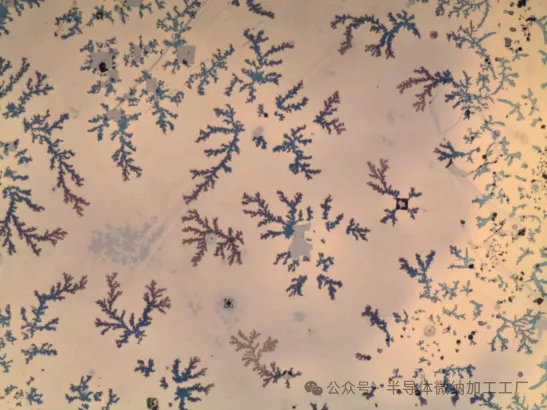
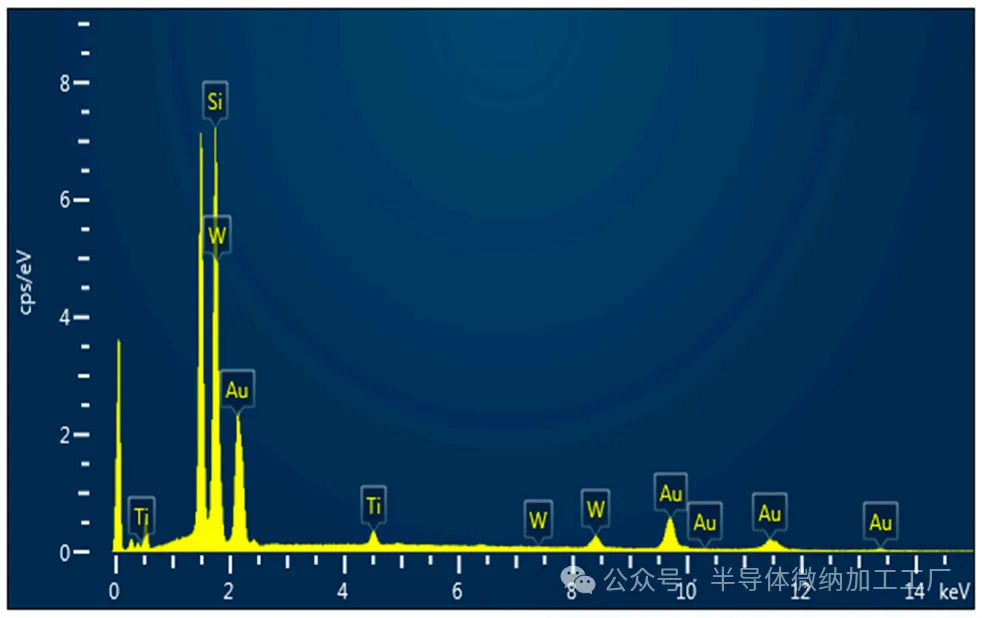
图 3. 高加热/冷却速率下的粘合失败。(a) 刀片测试后玻璃基板的分离表面;(b) 第 1 点的成分分析。
Au/Si共晶键合的优化温度曲线如图4所示。首先,用SB6e的最大功率将样品从室温加热到300℃。然后,温度升至 350 °C 并保持恒定 10 分钟,以均匀加热两个基板。随后,将样品以5℃/min的加热速率加热至400℃,并保持20min。最后,控制冷却速率为5℃/min,使Au和Si充分凝固。当温度高于300℃时施加接触力,同时从顶部和底部加热样品。
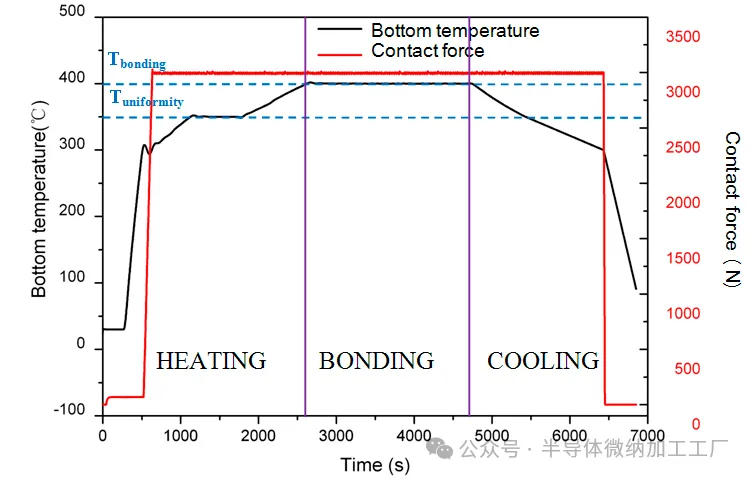
图 4. Au/Si 共晶晶圆键合的优化温度曲线。
4.3.接触力
同时,还考察了接触力对接合质量的影响,如表1(样品2、3和6)所示。可以看出,随着接触力从2000 N变化到3000 N,结合强度从37.5 MPa增加到66.8 MPa。一方面,高接触力可以克服非平面和粗糙的表面,保证Au和Au的良好接触。硅表面。另一方面,高接触力有利于破坏某些点处的自然氧化层[17]。因此,下面的硅中更多的暴露局部位点扩散到金中。直接接触区域的Si会溶解到Au中并沿着Au膜的晶界快速扩散,因此键合强度会增加。然而,随着接触力进一步增加到5000 N,结合强度下降到41.4 MPa。这是因为较高的接触力导致金属被挤出界面,导致界面层均匀性较差,界面处出现凹坑,如图5所示。但键合界面是均匀的,没有金属被挤压。3000 N 的接触力。
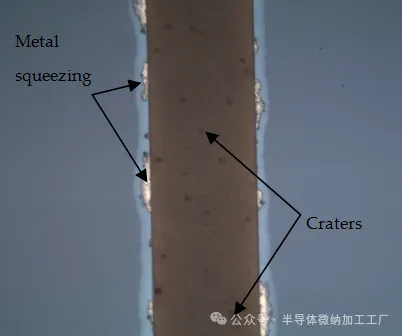
图 5. 在 5000 N 的高接触力下,键合界面出现金属挤压和凹坑。
此外,观察表1中拉伸强度的偏差,可以得出结论,高接触力增加了Au/Si反应的均匀性并提高了键合成品率,这也归因于Au和Si表面的紧密接触。此外,随着粘合时间的增加,粘合强度略有增加,从66.8 MPa增加到74.3 MPa,粘合时间从20 min增加到40 min,如表1(样品3和7)所示。然而,较长的键合时间也会增加 Au/Si 合金回流的风险 [18]。因此,粘合时间必须根据具体应用进行调整。综上所述,设计结构的最佳接触力为3000 N,粘合时间为20 min。4.4.粘合层
Cr 和 Ti 等金属化层通常沉积在基材上,以确保良好的粘附性,并且 Pt 已与粘附层结合使用,作为 Au 和基材之间的扩散阻挡层 [19]。然而,在 400 °C 的 Au/Si 共晶键合过程中,这些材料往往会扩散到 Au 或 Au/Si 合金中。因此,没有留下粘附层,粘附功能消失,导致Au或Au/Si合金从基体上分层,如图6所示。分析Cr/Au结构的合金成分,它含有5.07wt% % Si、91.9 wt% Au 和 3.03 wt% Cr,这与理想的 Au/Si 合金不同。这可以归因于Cr和Si之间的相互作用导致硅成分(CrSi 2 )的形成[20]。
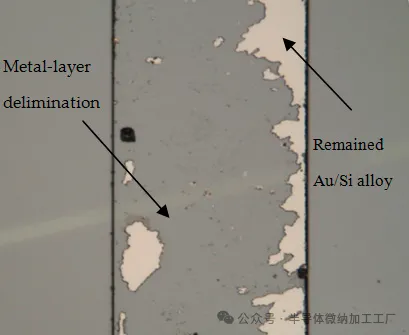
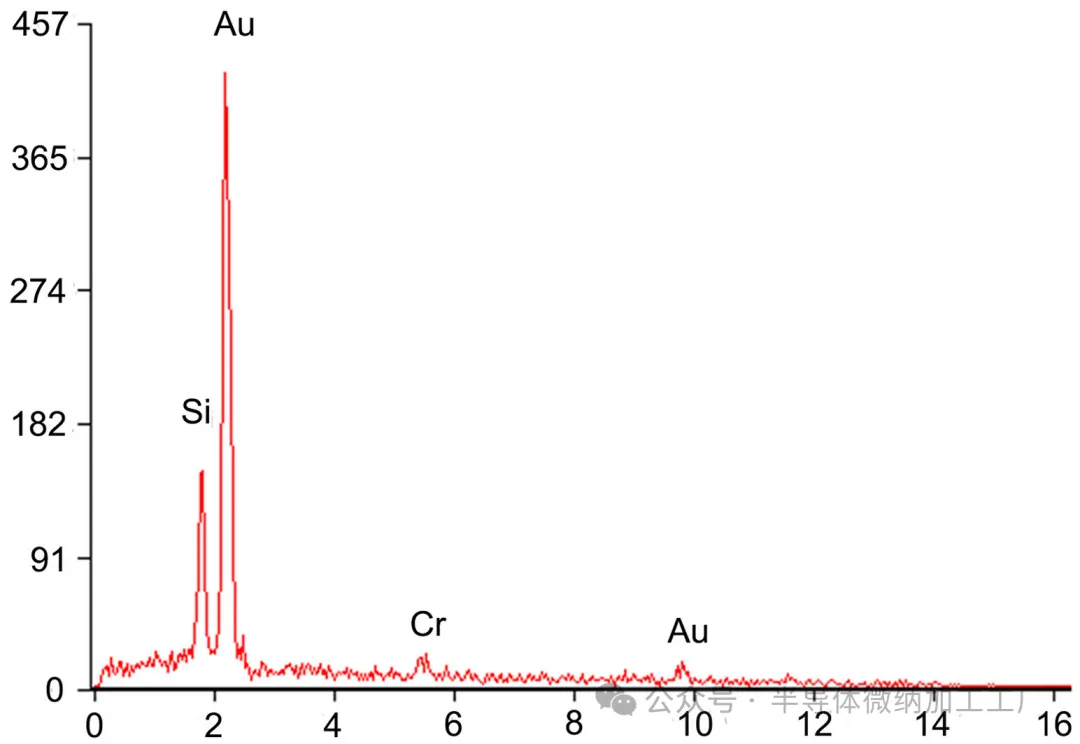
图 6. Cr/Au 层分离表面的光学照片和成分分析。(a) 基材金属层剥落;(b) Au/Si合金的成分分析。
TiW是一种复合难熔金属,其成分为Ti 10 wt%和W 90 wt%,可以作为成功Au/Si共晶键合的替代材料。TiW不仅是良好的粘附层,而且还是防止金属之间相互扩散的扩散阻挡层[7]。通过光学显微镜从 Pyrex 7740 玻璃背面观察来评估不同粘合层的粘合性能,如图 7 所示。可以看出,对或者
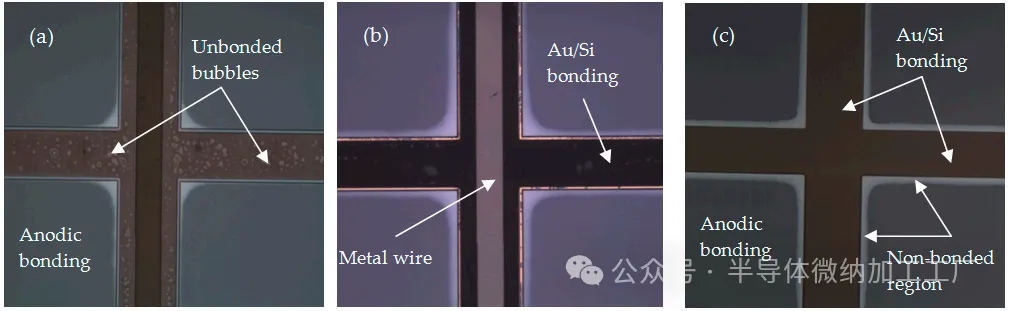
图 7.不同金属层的光学显微镜图像。(a)与Cr/Au层键合,键合界面出现未键合的气泡;(b)与Ti/Pt/Au层键合,由于Pt阻挡层的击穿,金属层的颜色发生变化;(c)与TiW/Au层键合,实现稳定的键合界面。
图 8 显示了 Au/Si 与 Ti/Pt/Au 和 TiW/Au 层键合界面的横截面 SEM 图像。两个样品中都可以看到明亮的键合界面,表明形成了 Au/Si 合金。然而,Ti/Pt/Au 层的键合界面前端不规则,厚度为 176.7 nm。键合界面的不均匀性主要是由于金属层与基材之间的相互扩散造成的。否则,高接触力也会导致金属挤压,并导致 Au/Si 合金厚度减小。然而,TiW/Au键合界面的前端是笔直且连续的,表现出66.8 MPa的高键合强度。与分别为 40 nm 和 160 nm 的 TiW/Au 厚度相比,由于 Si 扩散到 Au 层中,Au/Si 合金的厚度略有增加。
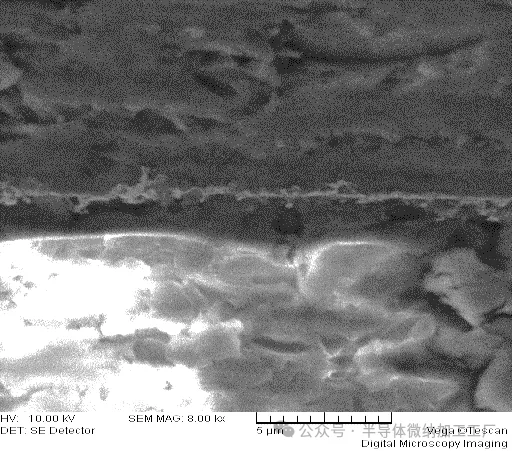
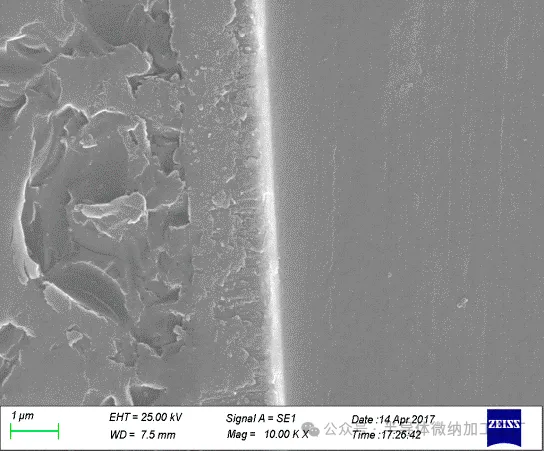
图 8. Au/Si 键合界面的横截面 SEM 图像。(a)与Ti/Pt/Au(40 nm/60 nm/120 nm)层键合,键合界面正面不规则;(b)与TiW/Au(40 nm/120 nm)层键合,键合界面正面平直且连续。
最后,研究了 Au/Si 与 TiW/Au 层共晶键合的重复性,键合温度为 400 °C,施加力为 3000 N,加热/冷却速率为 5 °C/min,键合时间为20分钟所有样品均表现出均匀的粘合界面。粘合强度从 57.6 MPa 到 67.8 MPa 不等,如表 1 所示(样品 3、4 和 5)。结果表明Au/Si共晶键合工艺具有良好的重复性,有利于进一步的应用。
5. Au/Si共晶键合在MEMS加速度计中的应用
5.1.包装设计
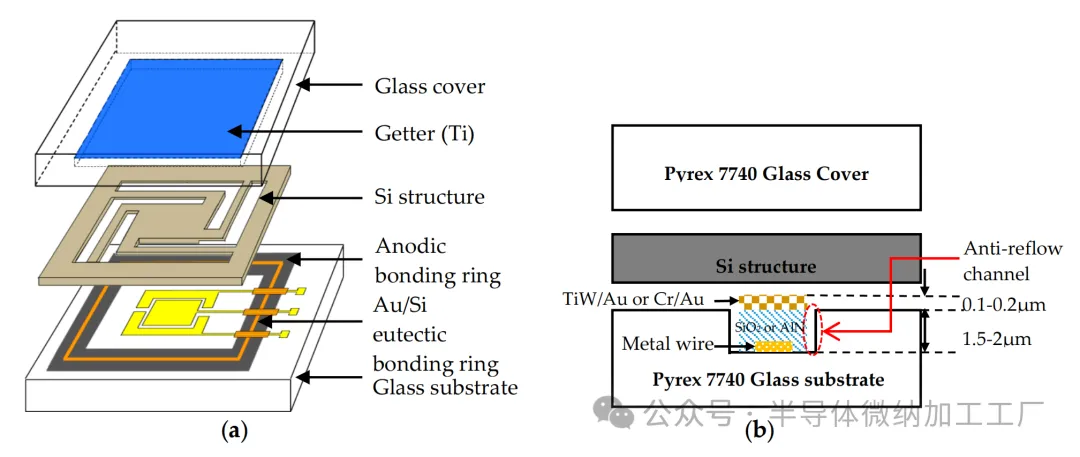
图 9a 显示了 MEMS 加速度计晶圆级封装的三维 (3D) 结构。它是典型的玻璃-硅-玻璃夹层结构。中间的硅器件晶片形成加速度计结构和密封壁,并通过阳极键合和金/硅共晶键合将其与玻璃基板键合。金属电极和金属线沉积在玻璃基板上,用于电压供应和信号传输,以及用于气密封装和金属线互连的键合环。带有图案化凹槽和钛吸气剂的玻璃盖板通过阳极键合与硅器件晶圆接合,提供真空室并确保真空的长期稳定性。图9b示出了从金属线部分观察的MEMS加速度计的横截面图。金属丝与Au/Si共晶键合环之间由厚度大于1.5μm的SiO 2 或AlN绝缘层隔开。防回流通道布置在Au/Si键合环的边缘,防止回流金属挤压到器件区域。另外,Au/Si共晶键合环比阳极键合环高0.1~0.2μm,这保证了键合环与Si器件层的良好接触,并最大限度地减少了Au/Si边缘的非键合区域共晶结合环(如图7c所示)。由于Au/Si共晶键合和阳极键合的加工温度相似,这种结构可以在单一键合工艺中实现气密封装和金属线互连。
图 9. MEMS 加速度计晶圆级真空封装示意图。(a) 封装MEMS加速度计的3D结构;(b)从金属线截面观察的加速度计的截面图。
5.2.制作流程
MEMS 加速度计制造的主要步骤如图 10 所示。该工艺从 Si 基板上的结构湿法蚀刻开始,然后溅射 40 nm/120 nm TiW/Au 层以形成敏感结构和阴极(图10a)。使用 Cr 和光致抗蚀剂 (PR) 作为蚀刻掩模,在 Pyrex 7740 玻璃上蚀刻出 1.5 μm 厚的凹槽(图 10b)。电极和金属线采用剥离工艺制作,并在金属线和Au/Si共晶键合环之间沉积1.5μm厚的SiO 2 或AlN以达到隔离目的(图10c)。Si器件层和Pyrex 7740玻璃在400℃下通过阳极键合和Au/Si共晶键合结合在一起,施加电压为-1000V(图10d)。通过将硅晶圆减薄至 85 μm 来确定硅器件层的厚度,然后通过深度反应离子蚀刻释放器件(图 10e)。玻璃盖上的 10 μm 深的空腔也用缓冲 HF 溶液蚀刻(图 10f),并通过溅射在空腔内沉积 500 nm Ti 吸气剂(图 10g)。Ti 吸气剂在 350 °C 阳极键合的晶圆级封装过程中被固有地激活(图 10h)。最后,通过切割工艺将加速芯片分离,尺寸为 6.1 mm × 7.5 mm(图 10k)。

图 10. MEMS 加速度计的主要制造工艺流程。
图 11 显示了带有和不带有玻璃盖的制造加速度计的照片。键合晶圆具有高键合强度,可以承受后续的减薄和切割工艺,而不会出现碎片剥落的情况。
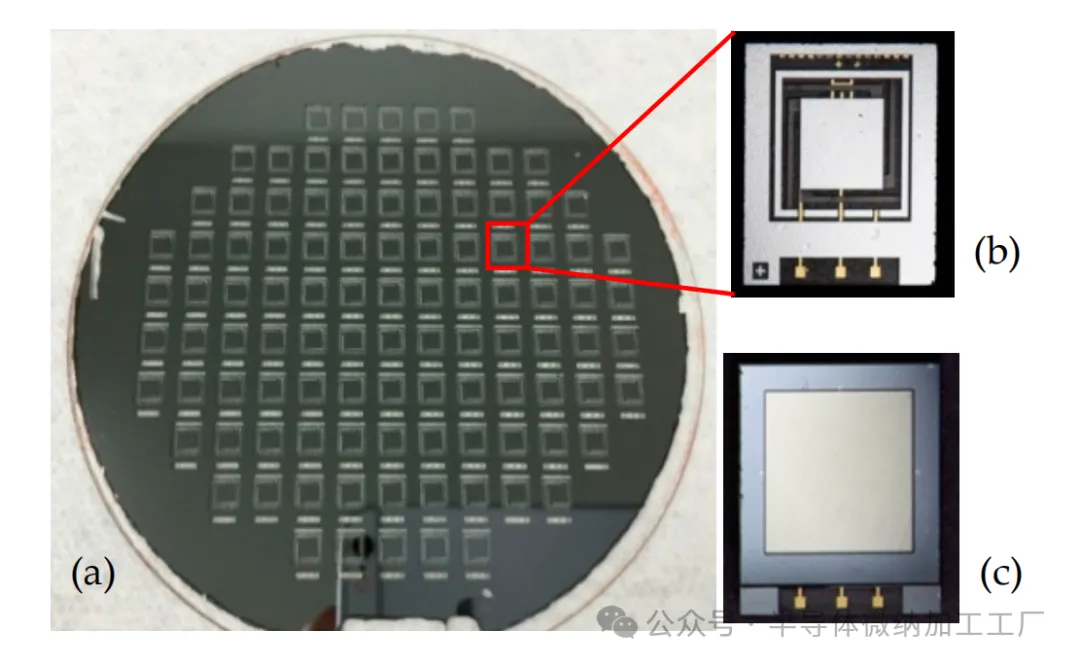
图 11. 制造的加速度计的照片。(a) 整个晶圆上的芯片;(b)没有玻璃盖的信号芯片;(c) 密封封装的芯片。
5.3.加速度计的性能
封装的加速度计的性能如图12所示。加速度计的非线性度为0.91%,加速度从-1g到+1g,灵敏度为1.06 V/g。此外,还分析了加速度计封装前后的/V特性。结果表明,真空封装后发射电流从52.4μA增加到76μA,这主要是由于真空度的提高。结果表明所设计的真空包装结构是可行的。然而,真空的长期保存和可靠性仍需要进一步的工作。
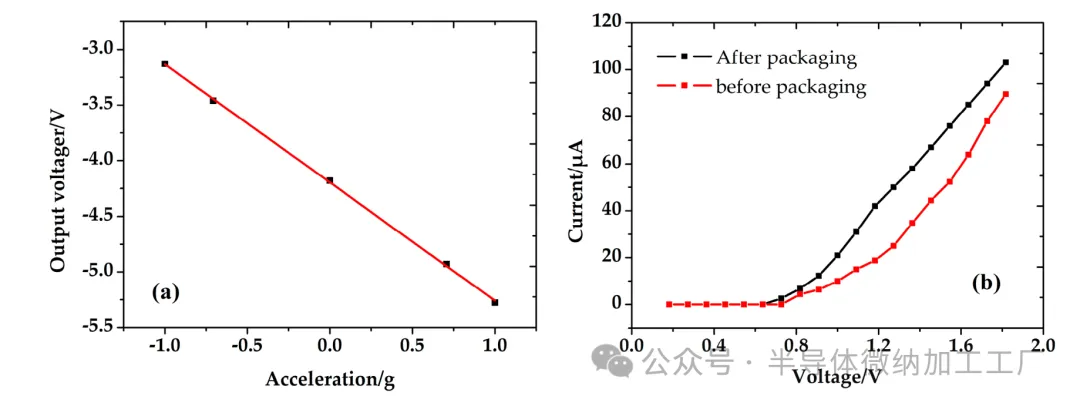
图 12. 加速度计的性能。(a) 加速度与输出电压的输出拟合曲线;(b) 加速度计的/V特性。
6。结论
本文研究了Au/Si共晶键合方法及其在MEMS加速度计封装中的应用。为了获得高的键合强度和均匀的键合界面,对Au/Si共晶键合的工艺参数进行了研究和优化。键合温度和加热/冷却速率被认为是影响Au/Si共晶键合质量的关键参数。为了实现稳定的 Au/Si 共晶键合,键合温度需要设置为 400 °C,加热/冷却速率为 5 °C/min。高接触力有利于键合均匀性,但当接触力从3000N增加到5000N时,由于金属被挤出界面,键合强度和键合成品率下降。TiW/Au层的结合性能明显优于Cr/Au或Ti/Pt/Au层,结合强度高于50 MPa,结合成品率高于90%。特别是基于Au/Si共晶键合和阳极键合实现了MEMS加速度计的晶圆级真空封装,可同时实现气密封装和金属线互连。测试结果显示MEMS加速度计的非线性度为0.91%,灵敏度为1.06 V/g。